Process for comprehensively recovering high arsenic polymetallic material
A technology for polymetals and materials, applied in the field of comprehensive recovery process of high arsenic polymetallic materials, can solve the problems of low direct yield of valuable metals, arsenic pollution, and low comprehensive recovery rate, and achieve high comprehensive recovery rate, Low cost and the effect of eliminating blower equipment
- Summary
- Abstract
- Description
- Claims
- Application Information
AI Technical Summary
Problems solved by technology
Method used
Image
Examples
experiment approach 1
[0030] (1) Take 500g of raw material and grind it finely, which contains 15.3% arsenic, 13.6% bismuth, 12.5% copper, and 18.6% lead ;
[0031] (2) Add 150g of sodium hydroxide, 2000g of water, and 25g of hydrogen peroxide to the raw material, heat and stir for 3.5 hours, then filter to obtain 308.1g of dearsenic mud (containing 0.8% arsenic), 1930mL of leachate, the filtrate contains 38.25g / L of arsenic, and the arsenic is recovered The rate is 96.5%. Sodium arsenate is obtained after impurity removal and purification of the leaching solution.
[0032] (3) Heat and stir the arsenic-removed mud with 900g of water, 93g of sulfuric acid, 31g of hydrochloric acid, and 15g of hydrogen peroxide for 3.5 hours, then filter to obtain 203.5g of filter residue, which contains 45.1% lead and a lead recovery rate of 98.7%. Bismuth copper solution 983 mL.
[0033] (4) Add lye (containing 30% sodium hydroxide) to the bismuth-copper solution to adjust the pH to 2.5, and share 150g of lye...
experiment approach 2
[0036] (1) Take 10kg of raw material and grind it finely, which contains 19.8% arsenic, 15.2% bismuth, 16.3% copper, and 15.8% lead;
[0037] (2) Add 3kg of sodium hydroxide, 50kg of water, and 500g of hydrogen peroxide to the raw material, heat and stir for 3.5 hours, then filter to obtain 6.16kg of arsenic-free mud (containing 0.92% arsenic), 48.30L of leaching solution, and the filtrate contains 39.7g / L of arsenic. The recovery rate is 96.8%. Sodium arsenate is obtained after impurity removal and purification of the leaching solution.
[0038] (3) Heat and stir the arsenic-removed mud with 18.5kg of water, 1.8kg of sulfuric acid, 616g of hydrochloric acid, and 310g of hydrogen peroxide for 3.5 hours, then filter to obtain 4.12kg of filter residue, which contains 37.6% lead and a lead recovery rate of 98%. Bismuth copper solution 18.01L.
[0039] (4) Add lye (containing 30% sodium hydroxide) to the bismuth-copper solution to adjust the pH to 2.5, and share 1760g of lye to ...
experiment approach 3
[0042] (1) Take 500g of raw material and grind it finely, which contains 5.2% arsenic, 14.2% bismuth, 15.8% copper, and 20.5% lead ;
[0043] (2) Add 150g of sodium hydroxide, 2000g of water, and 10g of hydrogen peroxide to the raw material, heat and stir for 3.5 hours, then filter to obtain 314.2g of dearsenic mud (containing 0.7% arsenic), 1830mL of leachate, the filtrate contains 19.01g / L of arsenic, and the arsenic is recovered The rate was 97.1%; the leach solution was purified to obtain sodium arsenate.
[0044](3) Heat and stir the arsenic-removed mud with 900g of water, 94g of sulfuric acid, 31g of hydrochloric acid, and 20g of hydrogen peroxide for 3.5 hours, then filter to obtain 210.4g of filter residue, which contains 48% lead and a lead recovery rate of 98.9%. Bismuth copper solution 983 mL.
[0045] (4) Add lye (containing 30% sodium hydroxide) to the bismuth-copper solution to adjust the pH to 2.5, and share 144g of lye to remove lye; obtain 97.12g of bismuth...
PUM
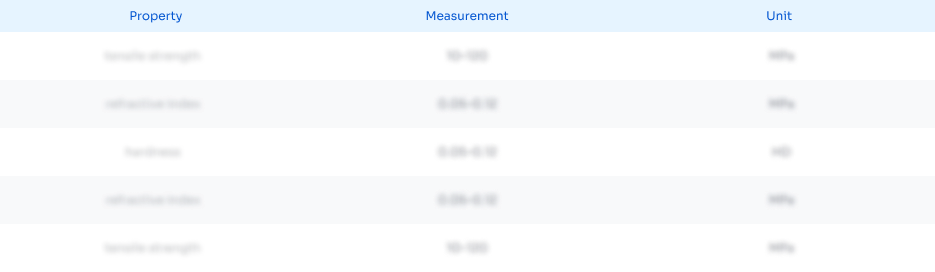
Abstract
Description
Claims
Application Information

- R&D
- Intellectual Property
- Life Sciences
- Materials
- Tech Scout
- Unparalleled Data Quality
- Higher Quality Content
- 60% Fewer Hallucinations
Browse by: Latest US Patents, China's latest patents, Technical Efficacy Thesaurus, Application Domain, Technology Topic, Popular Technical Reports.
© 2025 PatSnap. All rights reserved.Legal|Privacy policy|Modern Slavery Act Transparency Statement|Sitemap|About US| Contact US: help@patsnap.com