Anode material for lithium ion battery and preparation method thereof
A technology for lithium-ion batteries and negative electrode materials, applied in battery electrodes, chemical instruments and methods, circuits, etc., can solve problems such as complex operation, poor electrical conductivity of negative electrode materials for high-current charge and discharge, and easy aggregation of particles
- Summary
- Abstract
- Description
- Claims
- Application Information
AI Technical Summary
Problems solved by technology
Method used
Image
Examples
preparation example Construction
[0030] The invention discloses a preparation method of a negative electrode material of a lithium ion battery, which comprises the following steps:
[0031] Step a) mixing titanium dioxide and lithium carbonate, ball milling evenly, keeping the temperature at 750-850° C. for 10-180 minutes, and obtaining lithium titanate after cooling;
[0032] Step b) mixing the lithium titanate with a solid nitrogen source compound, then calcining under the protection of a protective gas, and obtaining a lithium ion battery negative electrode material after reaction.
[0033] In the above preparation method, the present invention firstly prepares lithium titanate, and then nitrates the lithium titanate to obtain TiN-surface-modified lithium titanate, that is, the lithium ion battery negative electrode material.
[0034] In the step a), the present invention uses titanium dioxide as the titanium source compound and lithium carbonate as the lithium source compound, and heats the titanium dioxi...
Embodiment 1
[0042] Li 4 Ti 5 o 12 Preparation of materials: Weigh Li according to the ratio of Li:Ti molar ratio of 0.8:1 2 CO 3 and anatase TiO 2 , acetone was used as a solvent, ball milled in a planetary ball mill at a speed of 300 rpm for 3 hours, the resulting mixture was dried at room temperature, placed in a muffle furnace at 800°C for 30 minutes, taken out, and cooled to room temperature to obtain Li 4 Ti 5 o 12 .
[0043] Li 4 Ti 5 o 12 Preparation of / TiN negative electrode material: according to the ratio of urea to the above-mentioned Li 4 Ti 5 o 12 The weight ratio is 6% to add urea, acetone is a solvent, with 300 revolutions per minute rotating speed in planetary ball mill ball mill 3 hours, after the gained mixture material is dried at room temperature, be placed in tube furnace, under argon atmosphere The temperature was raised to 800°C at a rate of 10°C / min, kept for 30 minutes and then cooled to room temperature to obtain Li 4 Ti 5 o 12 / TiN anode materi...
Embodiment 2
[0050] Li 4 Ti 5 o 12 The material was prepared in the same manner as in Example 1, and was fired in a muffle furnace at 800° C. for 10 minutes.
[0051] Li 4 Ti 5 o 12 The preparation of the / TiN negative electrode material is the same as in Example 1.
[0052] The XRD test results of the negative electrode material prepared in this embodiment are as follows: Figure 5 As shown, it can be seen from the figure that a large amount of reaction product Li has been produced after the mixed material is burned at 800°C for 10 minutes 4 Ti 5 o 12 generated, but there are still more TiO 2 No response.
[0053] Li 4 Ti 5 o12 The preparation and electrochemical testing of the / TiN negative electrode material are the same as in Example 1.
[0054] The electrochemical performance testing method of the negative electrode material prepared in this example is the same as that in Example 1. Li prepared by this example 4 Ti 5 o 12 The battery made of / TiN negative electrode ma...
PUM
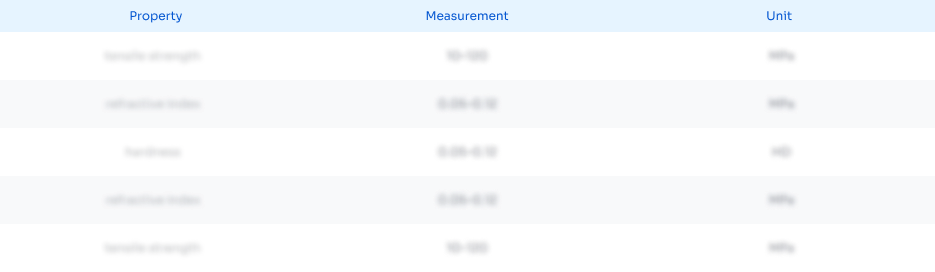
Abstract
Description
Claims
Application Information

- R&D
- Intellectual Property
- Life Sciences
- Materials
- Tech Scout
- Unparalleled Data Quality
- Higher Quality Content
- 60% Fewer Hallucinations
Browse by: Latest US Patents, China's latest patents, Technical Efficacy Thesaurus, Application Domain, Technology Topic, Popular Technical Reports.
© 2025 PatSnap. All rights reserved.Legal|Privacy policy|Modern Slavery Act Transparency Statement|Sitemap|About US| Contact US: help@patsnap.com