Preparation of sic/iron nitride nanocomposites from agricultural waste and method thereof
A technology of nanocomposite materials and agricultural waste, applied in the direction of nanotechnology, nanotechnology, nanotechnology for materials and surface science, etc., can solve the problems of increasing silicon carbide production costs, increasing energy consumption, and high equipment requirements. To achieve the effect of novel material structure, low cost and wide application
- Summary
- Abstract
- Description
- Claims
- Application Information
AI Technical Summary
Problems solved by technology
Method used
Examples
Embodiment 1
[0027] Embodiment 1: Take rice husk as raw material
[0028] 1) Fully pulverize 100 g of rice husk and put it into 400 o Calcined in the C furnace for 8 h in isolation from the air, and the main component was SiO 2 and silicon carbon powder of C;
[0029] 2) The obtained silicon carbon powder is fully mixed with 10 g metal magnesium powder, put into the furnace, and under the protection of high-purity nitrogen, 500 o C calcined for 12 h;
[0030] 3) Add the product of step 2) into 0.05 M hydrochloric acid solution and soak for 4 h; the product is centrifuged, washed with water, and dried in solid phase to obtain porous silicon carbide powder;
[0031] 4) Put 5 g of porous SiC powder in 20 mL of 1.0 mol / L ferric nitrate solution, 60 o C dried and placed in muffle furnace, 450 o C was calcined for 2 hours and then reduced by introducing nitrogen / hydrogen for 60 minutes; after the end, the furnace temperature was maintained, and the ammonia gas was quickly cut in for 60 minu...
Embodiment 2
[0032] Embodiment 2: Take rice straw as raw material
[0033] 1) Fully pulverize 100 g of rice straw and put it into 1200 o Calcined in furnace C for 0.5 h under the protection of high-purity nitrogen to obtain SiO 2 and silicon carbon powder of C;
[0034] 2) Fully mix the obtained silicon carbon powder with 2 g of metal aluminum powder, put it into the furnace, and isolate the air for 800 o C calcined for 0.5 h;
[0035] 3) Add the product of step 2) into 2 M hydrochloric acid solution and soak for 0.5 h; the product is centrifuged, washed with water, and dried in solid phase to obtain porous silicon carbide powder;
[0036] 4) Put 5 g of porous SiC powder in 100 mL of 0.05 mol / L ferric nitrate solution, 150 o C dried and placed in a muffle furnace, 750 o After calcination of C for 0.5 h, introduce nitrogen / hydrogen gas for reduction for 15 min; after the end, maintain the furnace temperature, quickly cut into ammonia gas for 10 min; take it out after natural cooling in n...
Embodiment 3
[0037] Embodiment 3: Taking wheat bran as raw material
[0038] 1) Fully pulverize 100 g of wheat bran and soak in 1 L of 25% concentrated sulfuric acid for 24 h to obtain SiO 2 and silicon carbon powder of C;
[0039] 2) The obtained silicon carbon powder is fully mixed with 5 g metal magnesium powder, put into the furnace, and under the protection of high-purity nitrogen gas, 700 o C calcined for 3 h;
[0040] 3) Add the product of step 2) into 0.2 M hydrochloric acid solution and soak for 2 h; the product is centrifuged, washed with water, and dried in solid phase to obtain porous silicon carbide powder;
[0041] 4) Put 5 g of porous SiC powder in 30 mL of 0.1 mol / L ferric nitrate solution, 70 o C dried and placed in muffle furnace, 550 o After calcination of C for 0.6 h, nitrogen / hydrogen gas was introduced to reduce for 25 min; after the end, the furnace temperature was maintained, and ammonia gas was quickly cut in for 20 min; after natural cooling in nitrogen flow, ...
PUM
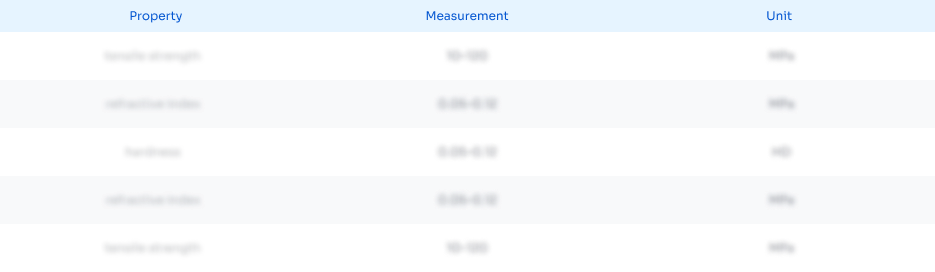
Abstract
Description
Claims
Application Information

- Generate Ideas
- Intellectual Property
- Life Sciences
- Materials
- Tech Scout
- Unparalleled Data Quality
- Higher Quality Content
- 60% Fewer Hallucinations
Browse by: Latest US Patents, China's latest patents, Technical Efficacy Thesaurus, Application Domain, Technology Topic, Popular Technical Reports.
© 2025 PatSnap. All rights reserved.Legal|Privacy policy|Modern Slavery Act Transparency Statement|Sitemap|About US| Contact US: help@patsnap.com