Iron-making method for producing granular iron by smelting reduction of high-phosphorus oolitic low-grade hematite in rotary hearth furnace
A technology of rotary hearth furnace and hematite, which is applied in the ironmaking field of smelting reduction of high-phosphorus oolitic-poor hematite in a rotary hearth furnace to produce granular iron, can solve problems such as raw material limitations, and achieve short process, high efficiency, and high efficiency. The effect of practical value
- Summary
- Abstract
- Description
- Claims
- Application Information
AI Technical Summary
Problems solved by technology
Method used
Examples
Embodiment 1
[0024] 1), batching: the following raw materials are batched by weight:
[0025] 5 parts of high phosphorus oolitic lean hematite; 1 part of coal and 0.9 part of flux;
[0026] Wherein, the weight content of iron in the high-phosphorus oolitic lean hematite is 44.90%, and the weight content of phosphorus is 0.76%; the coal is non-coking coal; the calorific value of the coal is 4000kcal / Nm 3 ; The flux is limestone.
[0027] 2) Rotary hearth furnace smelting reduction reaction: Mix the above three raw materials evenly, granulate and dry, put the green balls into the rotary hearth furnace, heat to 1250-1450°C, keep for 25-40 minutes, and then turn the bottom Furnace smelting reduction reaction, high-temperature intermediate iron and slag are discharged from the rotary hearth furnace;
[0028] Wherein, the granulation method is granulation by using a double-roller high-pressure briquetting machine; the extruded carbon-containing pellets have a particle size of an oblate spheroi...
Embodiment 2
[0036] 1), batching: the following raw materials are batched by weight:
[0037] 7 parts of high phosphorus oolitic lean hematite; 3 parts of coal and 0.1 part of flux;
[0038] Wherein, the weight content of iron in the high-phosphorus oolitic lean hematite is 30%, and the weight content of phosphorus is 2%; the coal is non-coking coal; the calorific value of the coal is 9000kcal / Nm 3 ; The flux is quicklime.
[0039] 2) Rotary hearth furnace smelting reduction reaction: mix the above three raw materials evenly, granulate and dry, put the raw balls into the rotary hearth furnace, heat to 1450°C, keep for 25 minutes, and carry out the rotary hearth furnace smelting reduction reaction , discharge high-temperature intermediate grain iron and slag from the rotary hearth furnace;
[0040] Wherein, the granulation method is granulation by using a double-roller high-pressure briquetting machine; the extruded carbon-containing pellets have a particle size of an oblate spheroid with...
Embodiment 3
[0045] 1), batching: the following raw materials are batched by weight:
[0046] 8 parts of high phosphorus oolitic lean hematite; 1 part of coal and 3 parts of flux;
[0047] Wherein, the weight content of iron in the high phosphorus oolitic hematite is 60%, and the weight content of phosphorus is 0.5%; the coal is non-coking coal; the calorific value of coal is 1000kcal / Nm 3 ; The flux is calcium carbonate.
[0048] 2) Rotary hearth furnace smelting reduction reaction: mix the above three raw materials evenly, granulate and dry, put the green balls into the rotary hearth furnace, heat to 1250°C, keep for 40 minutes, and carry out the rotary hearth furnace smelting reduction reaction , discharge high-temperature intermediate grain iron and slag from the rotary hearth furnace;
[0049] Wherein, the granulation method is granulation by using a double-roller high-pressure briquetting machine; the extruded carbon-containing pellets have a particle size of an oblate spheroid wit...
PUM
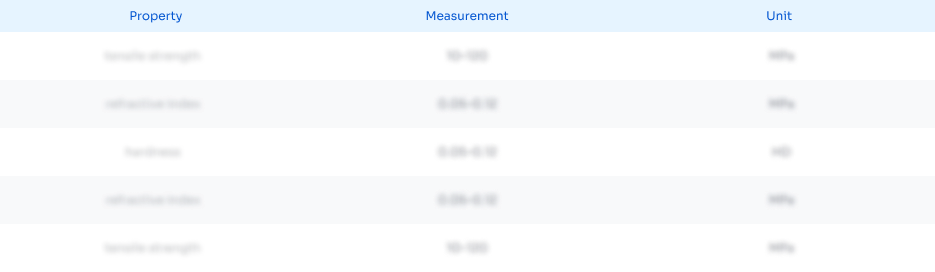
Abstract
Description
Claims
Application Information

- R&D
- Intellectual Property
- Life Sciences
- Materials
- Tech Scout
- Unparalleled Data Quality
- Higher Quality Content
- 60% Fewer Hallucinations
Browse by: Latest US Patents, China's latest patents, Technical Efficacy Thesaurus, Application Domain, Technology Topic, Popular Technical Reports.
© 2025 PatSnap. All rights reserved.Legal|Privacy policy|Modern Slavery Act Transparency Statement|Sitemap|About US| Contact US: help@patsnap.com