High-basicity refining slag for slag washing of revolving furnace steel-making
A converter steelmaking and refining slag technology, applied in the field of iron and steel metallurgy, can solve the problems of low desulfurization rate, unfavorable aluminum deoxidation, steel refining desulfurization, deoxidation and removal of non-metallic inclusions, adverse effects on production rhythm, etc.
- Summary
- Abstract
- Description
- Claims
- Application Information
AI Technical Summary
Problems solved by technology
Method used
Examples
Embodiment 1
[0032] Weigh the required raw materials according to the ratio shown in Table 1, and mix them with a disc mixer to make high-alkalinity refining slag. The obtained high alkalinity refining slag composition (percentage by weight) is: CaO: 72.2%, SiO 2 : 2.7%, Al 2 o 3 : 3.2%, Na 2 O: 2.8%, CaF 2 : 11.6%, MgO: 3.5%, and the rest are ignition components and trace impurities such as P and S, among which CaO / SiO 2 = 26.7.
[0033] When the high-basicity refining slag is used to smelt 20CrMoH steel in a converter, the sulfur content of molten steel at the end of smelting is 0.010%, the total iron (TFe) content of the slag at the end of smelting is 30.5%, and CaO / SiO 2 = 6.0. The amount of slag in the tapping process is 10kg / t 钢 Under the condition of 7kg / t at the beginning of tapping 钢 The amount of the high alkalinity refining slag is added for slag washing, the desulfurization rate of the tapping process is 50%, the nitrogen addition amount of molten steel is 0.00050%, and...
Embodiment 2
[0035] Weigh the required raw materials according to the ratio shown in Table 1, and mix them with a disc mixer to make high-alkalinity refining slag. The obtained high alkalinity refining slag composition (percentage by weight) is: CaO: 74.6%, SiO 2 : 1.8%, Al2 o 3 : 2.6%, Na 2 O: 2.7%, CaF 2 : 9.4%, MgO: 4.4%, and the rest are ignition components and trace impurities such as P and S, among which CaO / SiO 2 = 41.4.
[0036] When the high-basicity refining slag is used for smelting 20CrMoH steel in a converter, the sulfur content of molten steel at the end of smelting is 0.008%, the total iron (TFe) content of the slag at the end of smelting is 25.6%, and CaO / SiO 2 = 6.1. The amount of slag in the converter tapping process is 10kg / t 钢 Under the condition of 7.8kg / t at the beginning of tapping 钢 Add the high alkalinity refining slag to carry out slag washing, the desulfurization rate in the tapping process is 75%, the amount of nitrogen increase in molten steel is 0.00040...
Embodiment 3
[0038] Weigh the required raw materials according to the ratio shown in Table 1, and mix them with a disc mixer to make high-alkalinity refining slag. The obtained high alkalinity refining slag composition (percentage by weight) is: CaO: 73.3%, SiO 2 : 2.4%, Al 2 o 3 : 2.7%, Na 2 O: 2.8%, CaF 2 : 10.5%, MgO: 4.0%, and the rest are ignition components and trace impurities such as P and S, among which CaO / SiO 2 = 30.5.
[0039] When the high-basicity refining slag is used for P510L steel converter smelting, the sulfur content of molten steel at the end of smelting is 0.011%, the total iron (TFe) content of slag at the end of smelting is 30.6%, and CaO / SiO 2 = 4.8. The amount of slag in the converter tapping process is 9.5kg / t 钢 Under the condition of 5.3kg / t at the beginning of tapping 钢 Add the high alkalinity refining slag to carry out slag washing, the desulfurization rate in the tapping process is 45.5%, the amount of nitrogen increase in molten steel is 0.00030%, an...
PUM
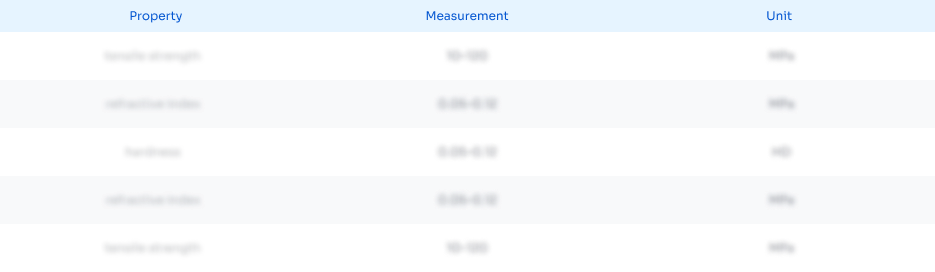
Abstract
Description
Claims
Application Information

- R&D Engineer
- R&D Manager
- IP Professional
- Industry Leading Data Capabilities
- Powerful AI technology
- Patent DNA Extraction
Browse by: Latest US Patents, China's latest patents, Technical Efficacy Thesaurus, Application Domain, Technology Topic, Popular Technical Reports.
© 2024 PatSnap. All rights reserved.Legal|Privacy policy|Modern Slavery Act Transparency Statement|Sitemap|About US| Contact US: help@patsnap.com