Wet-process treatment method of tungsten-containing molybdenum oxide rough concentrate
A technology for wet processing and rough concentrate, applied in chemical instruments and methods, wet separation, solid separation, etc., can solve the problems of high impurity content, high production and production costs, and achieve the effect of high precipitation rate
- Summary
- Abstract
- Description
- Claims
- Application Information
AI Technical Summary
Problems solved by technology
Method used
Image
Examples
Embodiment 1
[0030] The raw material is taken from Shengyuan Mining Henan Sanmenxia Chemical Plant, molybdenum oxide and tungsten coarse concentrate molybdenum and tungsten content Mo5.27%, WO 3 1.34%, grind molybdenum and tungsten oxide raw ore to -0.074mm, accounting for 60%, and carry out flotation; combine the use of hydrocyclone classification, cyclone screen, vibrating screen and water flow classifier to classify the obtained mineral particles, Those larger than 0.031mm are coarse-grained grades, and those smaller than or equal to 0.031mm are fine-grained grades. Add fine-grained molybdenum-tungsten oxide ore to water and sodium carbonate for high-pressure leaching. The leaching temperature is 130°C, and the leaching time is 80 minutes. Na 2 CO 3 It is 3 times the theoretical amount, and the liquid-solid ratio is 3; then filter and wash, add mineral acid (pH 3.5) to the obtained filtrate and 1-2 times of washing water for pretreatment, and return 3-4 times of washing water to high ...
Embodiment 2
[0032] The raw material is taken from Jingang Mining Industry, molybdenum oxide and tungsten coarse concentrate molybdenum and tungsten content Mo5%, WO 3 1.4%, grind molybdenum and tungsten oxide raw ore to -0.074mm, accounting for 60%, and carry out flotation; combine the use of hydrocyclone classification, cyclone screen, vibrating screen and water flow classifier to classify the obtained mineral particles, Those larger than 0.031mm are coarse-grained grades, and those smaller than or equal to 0.031mm are fine-grained grades. Add fine-grained molybdenum-tungsten oxide ore to water and sodium carbonate for high-pressure leaching. The leaching temperature is 200°C, and the leaching time is 30 minutes. Na 2 CO 3 It is 1 times the theoretical amount, and the liquid-solid ratio is 1.5; then filter and wash, add mineral acid (pH value 4) to the obtained filtrate and 1-2 times of washing water for pretreatment, and return 3-4 times of washing water to high pressure Leach ingred...
Embodiment 3
[0034] The raw material is taken from a factory of China Railway Resources, molybdenum oxide and tungsten coarse concentrate molybdenum and tungsten content Mo5.02%, WO 3 1.0%, grind molybdenum and tungsten oxide raw ore to -0.074mm, accounting for 60%, and carry out flotation; combine the use of hydrocyclone classification, cyclone screen, vibrating screen and water flow classifier to classify the obtained mineral particles, Those larger than 0.031mm are coarse-grained grades, and those smaller than or equal to 0.031mm are fine-grained grades. Add fine-grained molybdenum-tungsten oxide ore to water and sodium carbonate for high-pressure leaching. The leaching temperature is 150°C, and the leaching time is 60 minutes. Na 2 CO 3 It is twice the theoretical amount, and the liquid-solid ratio is 2; then filter and wash, add mineral acid (pH value 5) to the obtained filtrate and 1-2 times of washing water for pretreatment, and return 3-4 times of washing water to high pressure ...
PUM
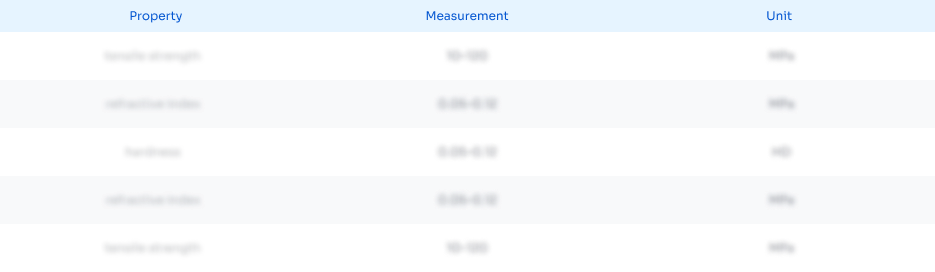
Abstract
Description
Claims
Application Information

- R&D
- Intellectual Property
- Life Sciences
- Materials
- Tech Scout
- Unparalleled Data Quality
- Higher Quality Content
- 60% Fewer Hallucinations
Browse by: Latest US Patents, China's latest patents, Technical Efficacy Thesaurus, Application Domain, Technology Topic, Popular Technical Reports.
© 2025 PatSnap. All rights reserved.Legal|Privacy policy|Modern Slavery Act Transparency Statement|Sitemap|About US| Contact US: help@patsnap.com