Method for achieving germanium precipitation through metallic oxide
An oxide and germanium precipitation technology, applied in the direction of improving process efficiency, can solve the problems of low germanium grade, high raw material requirements, harsh operating conditions, etc. Effect
- Summary
- Abstract
- Description
- Claims
- Application Information
AI Technical Summary
Problems solved by technology
Method used
Image
Examples
Embodiment 1
[0018] Take 50L sulfuric acid leaching solution from cobalt-copper smelting as the pre-precipitation solution for germanium, in which the concentration of Cu is 0.73g / L, the concentration of Fe is 22.97g / L, the concentration of Ge is 1.09g / L, and the concentrations of other impurities are shown in Table 1, and heated to 72°C , add metal oxide and water to the germanium pre-precipitation liquid, adjust the pH value to 5.0, carry out the alkaline one-stage germanium precipitation reaction for 1 hour and then filter, wash the first-stage filter residue and dry it for detection; heat the first-stage filtrate to 70°C and then add the metal oxide and water, adjust the pH value to 6.0, carry out the second-stage germanium precipitation reaction with alkali for 1 hour, and then filter, wash the second-stage filter residue, dry and test it, and test the second-stage filtrate. The test results are shown in Table 1.
[0019] Table 1 Example 1 detection result
[0020] Element ...
Embodiment 2
[0023] Take 50L of sulfuric acid leaching solution from cobalt-copper smelting as the pre-precipitation solution for germanium, in which the concentration of Cu is 0.55g / L, the concentration of Fe is 24.04g / L, the concentration of Ge is 1.28g / L, and the concentrations of other impurities are shown in Table 2, and heated to 75°C , add metal oxides and water to the germanium pre-precipitation liquid, adjust the pH value to 4.5, carry out the first-stage germanium precipitation reaction of alkali for 1.5h and then filter, wash the first-stage filter residue and dry it for detection; heat the first-stage filtrate to 72°C, add metal oxide matter and water, adjust the pH value to 5, carry out the alkali second-stage germanium precipitation reaction for 2 hours, then filter, wash the second-stage filter residue and then dry it for detection, and the second-stage filtrate for detection. The test results are shown in Table 2.
[0024] Table 2 embodiment 2 detection result
[0025] ...
Embodiment 3
[0029] Take 50L sulfuric acid leaching solution from cobalt-copper smelting as the precursor solution for germanium precipitation, in which the concentration of Cu is 0.46g / L, the concentration of Fe is 3.68g / L, the concentration of Ge is 0.79g / L, and the concentrations of other impurities are shown in Table 3, and heated to 70°C , add metal oxide and water to the germanium pre-precipitation liquid, adjust the pH value to 6, carry out the alkaline one-stage germanium precipitation reaction for 1 hour and then filter, wash the first-stage filter residue and dry it for detection, heat the first-stage filtrate to 75°C and then add the metal oxide and water, adjust the pH value to 7, carry out the alkali second-stage germanium precipitation reaction for 1 hour, then filter, wash the second-stage filter residue and dry it for detection, and the second-stage filtrate for detection. The test results are shown in Table 3.
[0030] Table 3 Example 3 detection results
[0031]
[00...
PUM
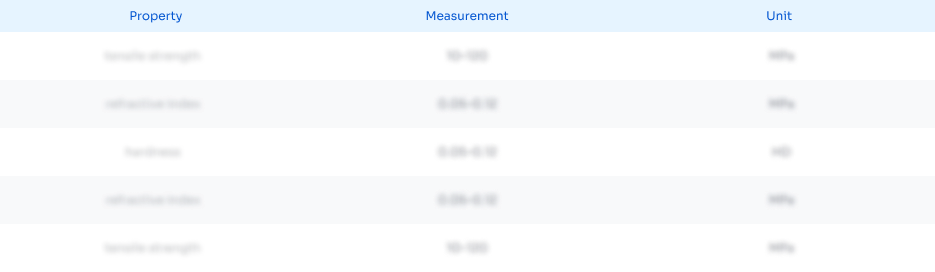
Abstract
Description
Claims
Application Information

- R&D
- Intellectual Property
- Life Sciences
- Materials
- Tech Scout
- Unparalleled Data Quality
- Higher Quality Content
- 60% Fewer Hallucinations
Browse by: Latest US Patents, China's latest patents, Technical Efficacy Thesaurus, Application Domain, Technology Topic, Popular Technical Reports.
© 2025 PatSnap. All rights reserved.Legal|Privacy policy|Modern Slavery Act Transparency Statement|Sitemap|About US| Contact US: help@patsnap.com