Method for coating copper on surface of iron powder
A technology of surface coating and iron powder, applied in the field of chemical displacement copper plating method to coat a layer of copper, and the surface of iron powder to coat copper, which can solve the problem of uneven copper coating, easy falling off and easy agglomeration of copper coating Agglomeration and other problems, to achieve the effect of controllable copper layer thickness, preventing copper layer oxidation and particle agglomeration
- Summary
- Abstract
- Description
- Claims
- Application Information
AI Technical Summary
Problems solved by technology
Method used
Examples
Embodiment 1
[0010] Replacement copper plating solution composition: copper phytate 7g / L, sulfuric acid (98%) 20g / L, composite additive 3.0g / L; The composition (quality) of composite additive: thiourea 5%, propenylthiourea 5%, benzene Triazole 28%, 8-hydroxyquinoline 12%, sulfosalicylic acid 15%, OP emulsifier 1%, sodium dodecylbenzenesulfonate 2%, saccharin 8% and polyethylene glycol 24% ;At room temperature, adjust the stirring speed to 500rpm, add iron powder with a particle size of 20-30um, plating time is 45min, and the thickness of the copper coating layer is 0.6-0.8um; after sedimentation, separation from iron phytate precipitation, washing and drying to obtain copper-clad iron powder. The iron powder coated copper process is as follows:
[0011] Iron powder → degreasing → water washing → pickling → water washing → displacement plating → water washing → precipitation and separation of copper-clad iron powder and ferric phytate → water washing → dehydration → drying → copper-clad ir...
Embodiment 2
[0013] Replacement copper plating solution composition: copper phytate 17g / L, sulfuric acid (98%) 60g / L, composite additive 4.5g / L, composite additive is formed with embodiment 1; At room temperature, adjust stirring speed to be 400rpm, add particle diameter It is 40-50um iron powder, the plating time is 60min, and the thickness of the copper cladding layer is 1.0-1.2um; after settling, separating from iron phytate precipitation, washing and drying, the copper-clad iron powder is obtained. The iron powder coated copper process flow is the same as in Example 1.
Embodiment 3
[0015] Replacement copper plating solution composition: copper phytate 20g / L, sulfuric acid (98%) 70g / L, composite additive 5.0g / L, composite additive is formed with embodiment 1; At room temperature, adjust stirring speed to be 300rpm, add particle diameter It is 60-80um iron powder, the plating time is 90min, and the thickness of the copper cladding layer is 1.5-1.7um; after settling, separating from iron phytate precipitation, washing and drying, the copper-coated ultrafine iron powder is obtained. The iron powder coated copper process flow is the same as in Example 1.
PUM
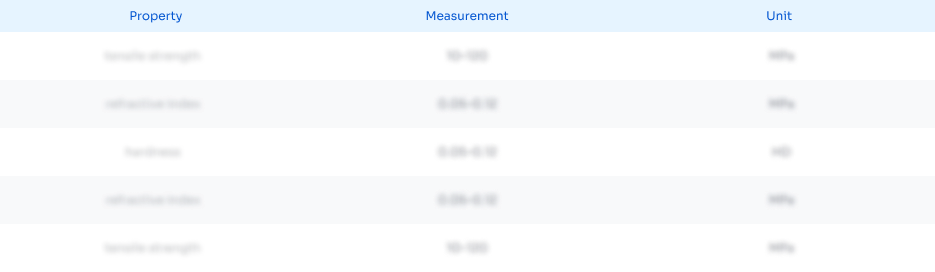
Abstract
Description
Claims
Application Information

- R&D
- Intellectual Property
- Life Sciences
- Materials
- Tech Scout
- Unparalleled Data Quality
- Higher Quality Content
- 60% Fewer Hallucinations
Browse by: Latest US Patents, China's latest patents, Technical Efficacy Thesaurus, Application Domain, Technology Topic, Popular Technical Reports.
© 2025 PatSnap. All rights reserved.Legal|Privacy policy|Modern Slavery Act Transparency Statement|Sitemap|About US| Contact US: help@patsnap.com