Gold recovery technology for processing arsenious S-C gangue coated gold concentrate by microwave fluidized roasting
A technology of boiling roasting and wrapping gold, applied in the direction of improving process efficiency, can solve the problems of harsh production conditions, high equipment requirements and high maintenance costs, and achieve the effects of promoting monomer dissociation, reducing energy consumption and improving recovery rate.
- Summary
- Abstract
- Description
- Claims
- Application Information
AI Technical Summary
Problems solved by technology
Method used
Image
Examples
Embodiment 1
[0026] (1) Preparation of ore pulp: The gold concentrate containing arsenic, sulfur, carbon and gangue with a particle size of less than 200 meshes and 60% of the gangue is properly blended to prepare a slurry with a liquid-solid weight ratio of 1:2.5. Add sodium carbonate according to 20kg / t gold concentrate and stir fully for 4 hours;
[0027] (2) Preliminary microwave boiling roasting: the slurry obtained in step (1) is pumped into the preliminary microwave boiling furnace, and an appropriate amount of air is blown into the preliminary microwave boiling roasting (microwave frequency 2.45GHz, power 600W) for 1.5 hours, and the furnace temperature is adjusted by adding water At 610℃, most of the iron in the gold concentrate is oxidized to Fe 3 O 4 , Arsenic uses As, As 2 S 3 , As 3 O 4 , Sulfur to SO 2 , S 2 Into the flue gas;
[0028] (3) Deep microwave boiling roasting: the calcine produced in step (2) and the dust collected in the flue gas are sent into a deep microwave boiling...
Embodiment 2
[0033] (1) Preparation of ore pulp: The gold concentrate containing arsenic, sulfur, carbon and gangue with a particle size of less than 200 meshes and accounting for 80% is coated with a reasonable ore mixture to prepare a slurry with a liquid-solid weight ratio of 1:3.5. Add sodium hydroxide at 15kg / t gold concentrate, and stir fully for 3 hours;
[0034] (2) Preliminary microwave boiling roasting: the slurry obtained in step (1) is pumped into the preliminary microwave boiling furnace, and an appropriate amount of air is blown into the preliminary microwave boiling roasting (microwave frequency is 1GHz, power is 200W) for 2 hours, and the furnace temperature is adjusted by adding water 625°C;
[0035] (3) Deep microwave boiling roasting: The calcine produced in step (2) and the smoke collected in the flue gas are sent into a deep microwave boiling furnace, and a large amount of air is blown into deep microwave boiling roasting (microwave frequency is 2.45GHz, power is 400W) 1 h...
Embodiment 3
[0038] (1) Preparation of ore pulp: the gold concentrate containing arsenic, sulfur, carbon and gangue with a particle size of less than 300 meshes and accounting for 70% is coated with a reasonable ore mixture to prepare a slurry with a liquid-solid weight ratio of 1:2.8. Add sodium nitrate at 10kg / t gold concentrate, and stir thoroughly for 2 hours;
[0039] (2) Preliminary microwave boiling roasting: The slurry obtained in step (1) is pumped into the preliminary microwave boiling furnace, and an appropriate amount of air is blown into the preliminary microwave boiling roasting (microwave frequency is 20GHz, power is 400W) for 1 hour, and the furnace temperature is adjusted by adding water 600°C;
[0040] (3) Deep microwave boiling roasting: The calcine produced in step (2) and the smoke collected in the flue gas are sent into a deep microwave boiling furnace, and a large amount of air is blown into deep microwave boiling roasting (microwave frequency is 10GHz, power is 5000W ) ...
PUM
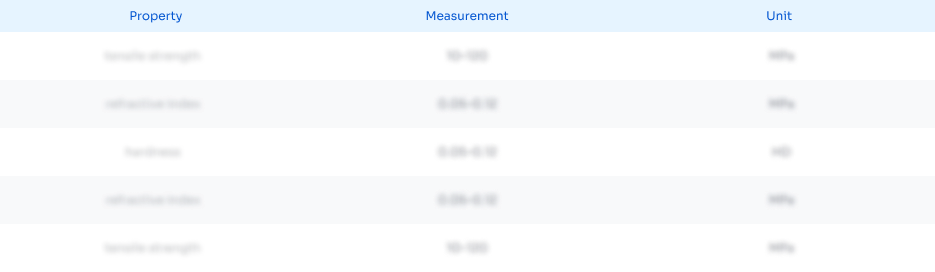
Abstract
Description
Claims
Application Information

- Generate Ideas
- Intellectual Property
- Life Sciences
- Materials
- Tech Scout
- Unparalleled Data Quality
- Higher Quality Content
- 60% Fewer Hallucinations
Browse by: Latest US Patents, China's latest patents, Technical Efficacy Thesaurus, Application Domain, Technology Topic, Popular Technical Reports.
© 2025 PatSnap. All rights reserved.Legal|Privacy policy|Modern Slavery Act Transparency Statement|Sitemap|About US| Contact US: help@patsnap.com