Porous high oil adsorption resin and its preparation method
A technology of oleoresin and porosity, which is applied in the field of porous high oil-absorbing resin and its preparation, can solve the problems that there is no industrialization report, and the oil absorption rate and oil absorption ratio of high oil-absorbing resin cannot meet the requirements at the same time, so as to avoid secondary Pollution, high absorption rate, good selectivity effect
- Summary
- Abstract
- Description
- Claims
- Application Information
AI Technical Summary
Problems solved by technology
Method used
Image
Examples
Embodiment 1
[0023] Add dispersant gelatin to water to prepare 0.3-5.0% aqueous solution, stir at 30--50°C to dissolve and cool. Then add 20---30 parts of butyl methacrylate, 70---80 parts of 2-ethylhexyl acrylate and 0.1%-0.6% of the total monomer amount of 1,4-butanediacrylate under stirring. Alcohol ester, benzoyl peroxide with 0.5%-1.6% of the total amount of monomers and carbon tetrachloride as a solvent, are heated up while stirring under the protection of nitrogen, and when the temperature reaches 70-100°C, the polymerization reaction starts. The reaction was maintained at this temperature for 5-7 hours. After the reaction is completed, the product is cooled, filtered, washed several times with hot water at 60-80°C, extracted with methanol as the solvent carbon tetrachloride, and dried in an oven at 50-70°C to obtain a porous super oil-absorbing resin.
[0024] The primary oil absorption rate (g / g) of the resin: 25 for benzene and 16 for cyclohexane; oil retention rate of 90%, oil ...
Embodiment 2
[0026] Add dispersant gelatin to water to prepare 0.3-5.0% aqueous solution, stir at 30--50°C to dissolve and cool. Then add 20---30 parts of butyl methacrylate, 70---80 parts of butyl acrylate, 0.1%--0.6% of the total amount of monomers, 1,4-butylene glycol diacrylate, mono 0.5%-1.6% of the total amount of benzoyl peroxide and ethyl acetate as a solvent, and the temperature is raised while stirring under the protection of nitrogen. When the temperature reaches 70-100°C, the polymerization reaction starts. The reaction was maintained at this temperature for 5-7 hours. After the reaction is completed, the product is cooled, filtered, washed several times with hot water at 60-80°C, extracted with methanol as the solvent ethyl acetate, and dried in an oven at 50-70°C to obtain a porous super oil-absorbing resin.
[0027] The primary oil absorption rate (g / g) of the resin: 25 for benzene and 15 for cyclohexane; the oil retention rate is 89%, and the oil absorption speed (time to ...
Embodiment 3
[0029] Add dispersant gelatin to water to prepare 0.3-5.0% aqueous solution, stir at 30--50°C to dissolve and cool. Then add 20---30 parts of isobutyl methacrylate, 70---80 parts of 2-ethylhexyl acrylate and 0.1%--0.6% of the total monomer amount of 1,4-butyl diacrylate under stirring. Glycol ester, benzoyl peroxide with 0.5%-1.6% of the total amount of monomers and toluene as a solvent, are heated up while stirring under nitrogen protection, and the polymerization reaction starts when the temperature reaches 70-100°C. The reaction was maintained at this temperature for 5-7 hours. After the reaction is completed, the product is cooled, filtered, washed several times with hot water at 60-80°C, extracted with methanol as the solvent toluene, and dried in an oven at 50-70°C to obtain a porous super oil-absorbing resin.
[0030] The primary oil absorption rate (g / g) of the resin: 21 for benzene and 12 for cyclohexane; the oil retention rate is 89%, and the oil absorption speed (t...
PUM
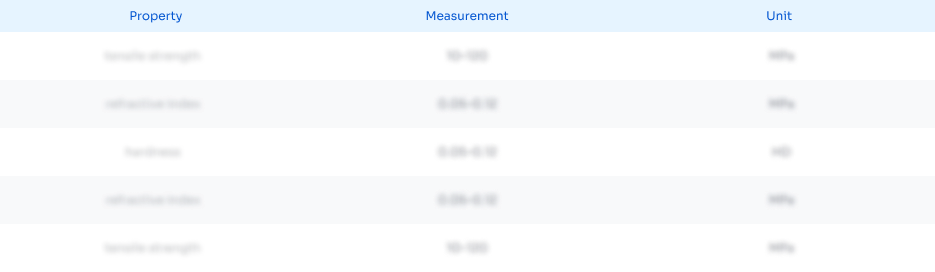
Abstract
Description
Claims
Application Information

- Generate Ideas
- Intellectual Property
- Life Sciences
- Materials
- Tech Scout
- Unparalleled Data Quality
- Higher Quality Content
- 60% Fewer Hallucinations
Browse by: Latest US Patents, China's latest patents, Technical Efficacy Thesaurus, Application Domain, Technology Topic, Popular Technical Reports.
© 2025 PatSnap. All rights reserved.Legal|Privacy policy|Modern Slavery Act Transparency Statement|Sitemap|About US| Contact US: help@patsnap.com