Multilayer line manufacturing process of wafer-level micro electromechanical system chip encapsulation technology
A technology of micro-electromechanical systems and chip packaging, which is applied in the process of producing decorative surface effects, micro-structure technology, metal material coating process, etc. Wait for the problem to achieve the effect of improving product yield
- Summary
- Abstract
- Description
- Claims
- Application Information
AI Technical Summary
Problems solved by technology
Method used
Examples
Embodiment
[0033] Embodiment: a kind of multi-layer circuit manufacturing process of wafer-level micro-electro-mechanical system chip packaging technology, with the IC face of the wafer as the wafer front, carry out according to the following process steps:
[0034] ①. Pre-process: Form a polymer resin photoresist surface on one side of the glass that matches the IC on the front side of the wafer, and bond the photoresist side of the glass to the front side of the wafer through a bonding machine;
[0035] ②.Wafer thinning: Grinding the wafer from the back to the thickness of the set size, and then performing plasma etching on the back of the wafer to remove the internal stress generated during grinding;
[0036] ③. Exposure and development: Baking after coating the photoresist on the back of the wafer, exposing and developing the photoresist on the back of the wafer according to the design, and developing the photoresist coated on the place to be etched on the back of the wafer;
[0037]...
PUM
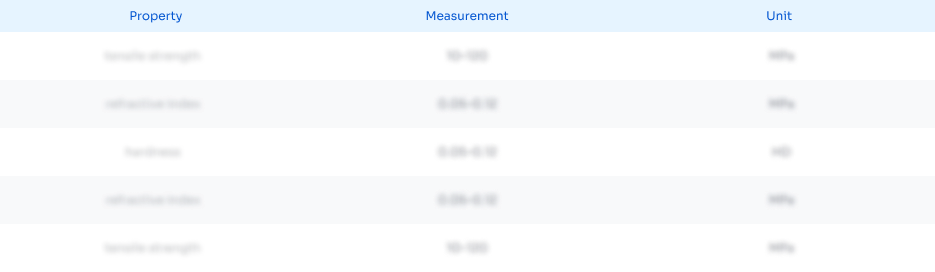
Abstract
Description
Claims
Application Information

- R&D
- Intellectual Property
- Life Sciences
- Materials
- Tech Scout
- Unparalleled Data Quality
- Higher Quality Content
- 60% Fewer Hallucinations
Browse by: Latest US Patents, China's latest patents, Technical Efficacy Thesaurus, Application Domain, Technology Topic, Popular Technical Reports.
© 2025 PatSnap. All rights reserved.Legal|Privacy policy|Modern Slavery Act Transparency Statement|Sitemap|About US| Contact US: help@patsnap.com