Short-flow rotary hearth furnace continuous steelmaking method comprehensively utilizing resources
A rotary hearth furnace and short-process technology, applied in the field of iron and steel metallurgy, can solve the problems of high production cost, high comprehensive energy consumption, and failure to achieve the effect of high-efficiency energy utilization and high-efficiency reuse, and achieve small footprint and low operating costs. Low, high energy efficiency effect
- Summary
- Abstract
- Description
- Claims
- Application Information
AI Technical Summary
Problems solved by technology
Method used
Image
Examples
Embodiment Construction
[0009] A short-process rotary hearth furnace continuous steelmaking method that comprehensively utilizes energy, including material ball milling, batching, pelletizing, pelletizing shaft furnace preheating, rotary hearth furnace pre-reduction, continuous steelmaking, molten steel refining, continuous casting, and rolling Become a material, the steps are as follows:
[0010] 1) The iron-containing materials are pelletized and processed into pellets after ball milling and batching.
[0011] 2) The pellets obtained in step 1) are preheated to 3500-450°C by the 850-950°C exhaust gas discharged from the oxygen-enriched air preheater of the rotary hearth furnace in the preheating device and sent to the rotary hearth furnace.
[0012] 3) In the rotary hearth furnace, the pellets are burned and heated by high-temperature reformed gas at 800-850°C to obtain pre-reduced metallized pellets with a metallization rate of 85-95% and a furnace temperature of 1000-1200°C for continuous steelma...
PUM
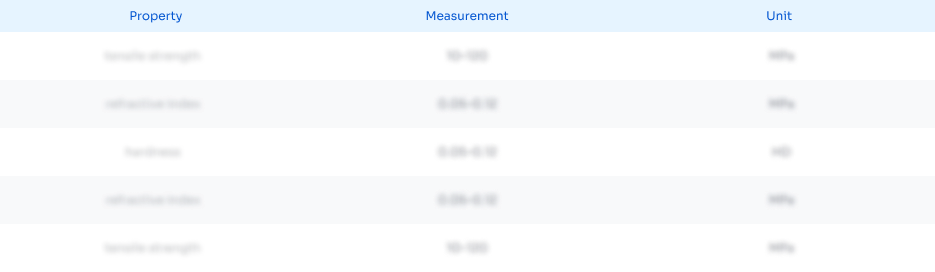
Abstract
Description
Claims
Application Information

- Generate Ideas
- Intellectual Property
- Life Sciences
- Materials
- Tech Scout
- Unparalleled Data Quality
- Higher Quality Content
- 60% Fewer Hallucinations
Browse by: Latest US Patents, China's latest patents, Technical Efficacy Thesaurus, Application Domain, Technology Topic, Popular Technical Reports.
© 2025 PatSnap. All rights reserved.Legal|Privacy policy|Modern Slavery Act Transparency Statement|Sitemap|About US| Contact US: help@patsnap.com