Method and device for ironmaking by smelting
A heat exchange device and a three-step technology, applied in the direction of fluidized bed furnace, etc., can solve the problems of insufficient utilization of heat energy, unused gas recycling, and low production efficiency, so as to achieve full utilization of heat energy, energy saving, and high production efficiency Effect
- Summary
- Abstract
- Description
- Claims
- Application Information
AI Technical Summary
Problems solved by technology
Method used
Image
Examples
Embodiment 1
[0022] The smelting reduction ironmaking device of the present invention is as figure 1 As shown, it includes a pre-reduction furnace 2, a gas treatment device 3, two final reduction furnaces 6, and a high-temperature heat exchange device 9. The pre-reduction furnace is a shaft furnace, and a feeding device 1 is arranged on the top of the pre-reduction furnace. The final reduction furnace is a sealed electric heating furnace (such as an induction heating furnace). There are electric heating facilities 7 around the furnace body. There are molten iron outlets 11 on the side of the furnace body. There are nozzles 13 on the upper part of the furnace body for injecting fuel. A screw conveyor 4 is provided between the pre-reduction furnace and the final reduction furnace, which is the passage for the products of the pre-reduction furnace to enter the final reduction furnace. The air intake pipe 5 is a gas channel through which the final reduction furnace gas enters the pre-reductio...
Embodiment 2
[0028] Another scheme of the present invention takes iron oxide (hematite or magnetite) as raw material, iron oxide ore is ground into ore powder and is made as Figure 6 The honeycomb-shaped non-carbon-containing molded object 35 shown is smelted and reduced in a smelting reduction device to produce molten iron or direct reduction molten steel. The smelting reduction device includes a pre-reduction furnace, a gas treatment device, two final reduction furnaces, and a high-temperature heat exchange device. Among them, the pre-reduction furnace is a shaft furnace, the final reduction furnace is an electric arc furnace 24, and the high-temperature heat exchange device is a regenerative heater 29
[0029] Such as image 3 As shown, the electric arc furnace includes a furnace body 24, a graphite electrode 25, a gas inlet 30 at the bottom of the electric arc furnace, and a molten iron outlet 11 on the side wall. The upper part of the electric arc furnace has a gas outlet 12 and a ...
Embodiment 3
[0034] Another solution of the present invention includes a pre-reduction furnace, a gas treatment device, a final reduction furnace and a high-temperature heat exchange device. The pre-reduction furnace is a shaft furnace, the high-temperature heat exchange device is a molten pool heating furnace, and the final reduction furnace is an electroslag furnace.
[0035] The molten pool is a body of furnace with molten iron, and its bottom or side wall is equipped with a spout 33. The molten pool heating furnace is airtightly connected with the final reduction furnace to isolate the air. The precipitated gas enters the molten iron pool from the nozzle, is heated to a high temperature, and then enters the final reduction furnace to be used as a heat carrier, protective gas or reducing agent. The molten pool heating furnace can be heated by electric heating, electric arc furnace, induction furnace, electroslag furnace or plasma furnace, and this embodiment is electric heating. Such a...
PUM
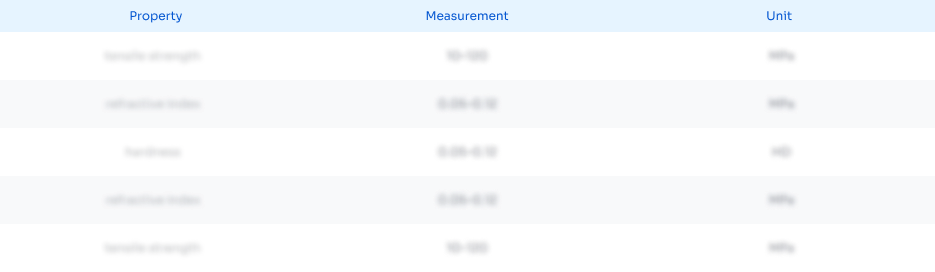
Abstract
Description
Claims
Application Information

- R&D
- Intellectual Property
- Life Sciences
- Materials
- Tech Scout
- Unparalleled Data Quality
- Higher Quality Content
- 60% Fewer Hallucinations
Browse by: Latest US Patents, China's latest patents, Technical Efficacy Thesaurus, Application Domain, Technology Topic, Popular Technical Reports.
© 2025 PatSnap. All rights reserved.Legal|Privacy policy|Modern Slavery Act Transparency Statement|Sitemap|About US| Contact US: help@patsnap.com