Modified hot setting resin and preparation method thereof
A thermosetting and resin technology, applied in the field of modified thermosetting resin and its preparation, can solve the problems of reduced strength, modulus and heat resistance, reduced polymer storage stability, and insignificant increase in toughness, etc., to achieve excellent dielectric properties , Outstanding thermal stability and good compatibility
- Summary
- Abstract
- Description
- Claims
- Application Information
AI Technical Summary
Problems solved by technology
Method used
Image
Examples
Embodiment 1
[0031] 1) Under stirring conditions, after adding 45.00g of γ-glycidoxypropyltrimethoxysilane, 5.15g of deionized water and 0.09g of tetramethylammonium hydroxide (20% aqueous solution) into a three-necked flask, at 40°C Reflux at a constant temperature for 2 hours to obtain solution A;
[0032] 2) Under stirring conditions, dissolve 30.89g of trimethylchlorosilane in a mixed solvent of 18.00mL of methanol and 36.00mL of pyridine to obtain solution B;
[0033] 3) Under the conditions of stirring and nitrogen protection, pour solution B into solution A at 60°C, and reflux at constant temperature at 60°C for 6 hours, and obtain the crude product after vacuum distillation;
[0034] 4) After the crude product is dissolved in dichloromethane, the insoluble matter is filtered off, and after vacuum distillation and vacuum drying, the hyperbranched silicone resin containing the active functional group is an epoxy group, and its structural formula is:
[0035]
[0036] Among them, ...
Embodiment 2
[0039] 1) Under stirring conditions, add 45.00g of γ-glycidoxypropyltrimethoxysilane, 3.43g of deionized water and 0.04g of KOH into a three-necked flask, and reflux at 90°C for 8 hours to obtain solution A;
[0040] 2) Under stirring conditions, dissolve 15.44g of hexamethyldisiloxane in a mixed solvent consisting of 5.00mL of n-butanol and 8.30mL of tetrahydrofuran to obtain solution B;
[0041] 3) Under the conditions of stirring and nitrogen protection, pour solution B into solution A at 60-90°C, and reflux at 90°C for 8 hours, and obtain the crude product after vacuum distillation;
[0042] 4) After the crude product is dissolved in dichloromethane, the insoluble matter is filtered off, and after vacuum distillation and vacuum drying, a hyperbranched silicone resin containing an epoxy group as an active functional group is obtained.
[0043] 5) By weight, 100g epoxy resin (E-51), 50g novolak resin, 100g hyperbranched silicone resin containing epoxy group obtained above, 15g...
Embodiment 3
[0045] 1) Under the conditions of stirring and nitrogen protection, add 45.00g of γ-glycidoxypropyltrimethoxysilane, 4.46g of deionized water and 0.05g of p-toluenesulfonic acid into a three-necked flask, and reflux at 65°C for 4 Hour, obtain solution A;
[0046] 2) Under the conditions of stirring and nitrogen protection, 23.22g of hexamethyldisiloxane was dissolved in a mixed solvent composed of 20.00mL of ethanol and 10.00mL of pyridine to obtain solution B;
[0047] 3) Under the conditions of stirring and nitrogen protection, pour solution B into solution A at 60-65 ° C, reflux at 65 ° C for 7 hours, and obtain the crude product after vacuum distillation;
[0048] 4) After the crude product is dissolved in dichloromethane, the insoluble matter is filtered off, and after vacuum distillation and vacuum drying, a hyperbranched silicone resin containing an epoxy group as an active functional group is obtained.
[0049] 5) By weight, 100 g of phenolic resin, 50 g of the hyperb...
PUM
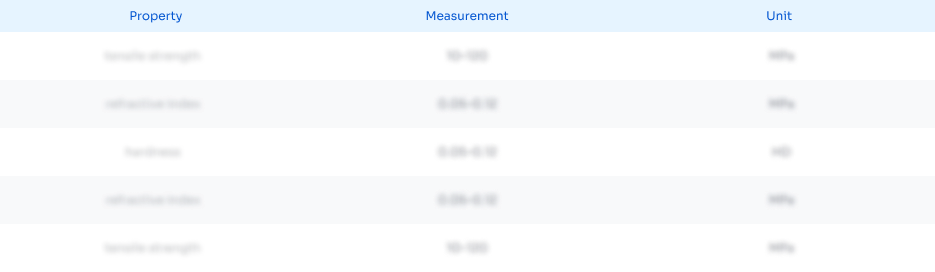
Abstract
Description
Claims
Application Information

- Generate Ideas
- Intellectual Property
- Life Sciences
- Materials
- Tech Scout
- Unparalleled Data Quality
- Higher Quality Content
- 60% Fewer Hallucinations
Browse by: Latest US Patents, China's latest patents, Technical Efficacy Thesaurus, Application Domain, Technology Topic, Popular Technical Reports.
© 2025 PatSnap. All rights reserved.Legal|Privacy policy|Modern Slavery Act Transparency Statement|Sitemap|About US| Contact US: help@patsnap.com