Aluminum-calcium-magnesium-cerium composite alloy used for strong desulfurization, final desoxidation, and quenching and tempering of liquid steel
A composite alloy and deep desulfurization technology, applied in the field of ferroalloys for steelmaking, can solve the problems of reducing steel performance, easily blocking nozzles, reducing steel toughness, etc., to achieve the effect of improving refining efficiency and effect, improving comprehensive performance, and improving performance.
- Summary
- Abstract
- Description
- Claims
- Application Information
AI Technical Summary
Problems solved by technology
Method used
Examples
Embodiment 1
[0027] (1) Alloy preparation
[0028]Composite international standard pure aluminum ingot 37% (mass ratio, the same below), calcium aluminum alloy 10%, calcium magnesium alloy 13%, titanium iron 7%, aluminum cerium alloy 20%, and the balance is pure ultra-low carbon scrap steel ingredients , the ingredients of the raw materials are shown in Table 1.
[0029] The raw material composition of table 1 embodiment 1
[0030] product name
Main ingredients (mass%)
Impurity elements (not more than mass%)
Calcium aluminum alloy
Ca 79, Al 20
Fe 0.03, Mg 0.2, Si 0.008, Mn 0.02, other traces
quantity
calcium magnesium alloy
Ca 19, Mg 80
Fe 0.1, Mn 0.1, Si 0.08, Cu 0.02, other traces
Ce 5.5 Al 94
Si 0.1, Fe 0.3, Ni, 0.05, Cu 0.01
Ferro-titanium alloy
Ti 60 Fe balance
1%, C 0.02, Si 0.03, Cu 0.01, Mn 0.01
[0031] Melt in 500kg intermediate frequency induction furnace after batchin...
Embodiment 2
[0040] 30% of pure aluminum ingots, 15% of calcium-aluminum alloys, 20% of calcium-magnesium alloys, 10% of aluminum-cerium alloys, 15% of ferro-molybdenum, and 5% of ferro-boron compounded with international standards, and the balance is pure ultra-low carbon scrap steel ingredients, raw materials The composition is shown in Table 2.
[0041] The raw material composition of table 2 embodiment 2
[0042] product name
Main ingredients (mass%)
Impurity elements (not more than mass%)
Calcium aluminum alloy
Ca 79, Al 20
Fe 0.03, Mg 0.2, Si 0.008, Mn 0.02, other traces
quantity
calcium magnesium alloy
Ca 19, Mg 80
Fe 0.1, Mn 0.1, Si 0.08, Cu 0.02, other traces
Ce 5.5 Al 94
Si 0.1, Fe 0.3, Ni, 0.05, Cu 0.01
[0043] product name
Main ingredients (mass%)
Impurity elements (not more than mass%)
Mo 60 Fe balance
1%, C 0.02, Si 0.03, Cu 0....
Embodiment 3
[0053] 12% of pure aluminum ingot, 20% of calcium-aluminum alloy, 30% of calcium-magnesium alloy, and 10% of aluminum-cerium alloy are compounded with international standards, and the balance is pure ultra-low carbon scrap steel. The composition of raw materials is shown in Table 3.
[0054] The raw material composition of table 3 embodiment 3
[0055] product name
Main ingredients (mass%)
Impurity elements (not more than mass%)
Calcium aluminum alloy
Ca 79, Al 20
Fe 0.03, Mg 0.2, Si 0.008, Mn 0.02, other traces
quantity
calcium magnesium alloy
Ca 19, Mg 80
Fe 0.1, Mn 0.1, Si 0.08, Cu 0.02, other traces
Al-Cerium Alloy
Ce 5.5 Al 94
Si 0.1, Fe 0.3, Ni, 0.05, Cu 0.01
[0056] Melt in 500kg intermediate frequency induction furnace after batching and make composite alloy, chemical composition (mass %) is:
[0057] Aluminum 20%, calcium 20%, magnesium 22%, cerium 0.55%, the balance is iron and unavoidab...
PUM
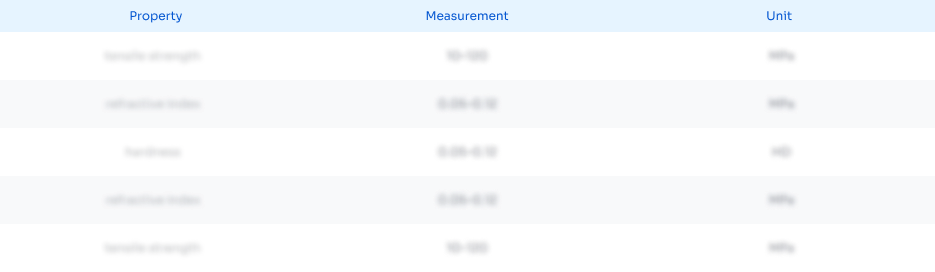
Abstract
Description
Claims
Application Information

- R&D
- Intellectual Property
- Life Sciences
- Materials
- Tech Scout
- Unparalleled Data Quality
- Higher Quality Content
- 60% Fewer Hallucinations
Browse by: Latest US Patents, China's latest patents, Technical Efficacy Thesaurus, Application Domain, Technology Topic, Popular Technical Reports.
© 2025 PatSnap. All rights reserved.Legal|Privacy policy|Modern Slavery Act Transparency Statement|Sitemap|About US| Contact US: help@patsnap.com