Ultra high-temperature resistant nickel-chrome alloy and manufacturing method thereof
A technology of nickel-chromium alloy and manufacturing method, which is applied in the field of high-temperature-resistant nickel-chromium alloy and its manufacturing, and can solve the problem of insufficient stability of quality indicators such as high-temperature resistance and tensile strength, materials that cannot withstand high temperatures, and insufficient control of copper elements in parameter control Accuracy and other issues, to achieve the effect of comprehensive performance improvement, high cost-effectiveness, and metallographic structure improvement
- Summary
- Abstract
- Description
- Claims
- Application Information
AI Technical Summary
Problems solved by technology
Method used
Image
Examples
Embodiment 1
[0022] Example 1: The formula of high temperature resistant nickel-chromium alloy consists of: C: 0.1 (weight percent, the same below), Si: 0.5, Mn: 1.0, S: 0.014, Cr: 21, Ni: 58, Al: 1.0, Cu: 1, Fe is the balance.
[0023] After batching according to the above alloy components, smelting is carried out; the second step is secondary refining; the third step is thermal processing, first heated to 900 ° C, and after 40 minutes of heat preservation, forging is carried out; the fourth step is cold processing; Five steps, using water cooling for heat treatment.
Embodiment 2
[0024] Example 2: The formula of high temperature resistant nickel-chromium alloy consists of: C: 0.08 (weight percent, the same below), Si: 0.5, Mn: 1.0, S: 0.014, Cr: 25, Ni: 63, Al: 1.7, Cu: 0.5, Fe is the balance.
[0025] After batching according to the above alloy composition, smelting is carried out; the second step is secondary refining; the third step is thermal processing, first heated to 1200 ° C, and after 10 minutes of heat preservation, forging is carried out; the fourth step is cold processing; Five steps, using water cooling for heat treatment.
Embodiment 3
[0026] Example 3: The formula of high temperature resistant nickel-chromium alloy consists of: C: 0.05 (weight percent, the same below), Si: 0.1, Mn: 0.3, S: 0.008, Cr: 23, Ni: 60, Al: 1.01, Cu: 0.51, Fe is the balance.
[0027] After batching according to the above alloy components, smelting is carried out; the second step is secondary refining; the third step is thermal processing, first heated to 950 ° C, and after 15 minutes of heat preservation, forging is carried out; the fourth step is cold processing; Five steps, using water cooling for heat treatment.
PUM
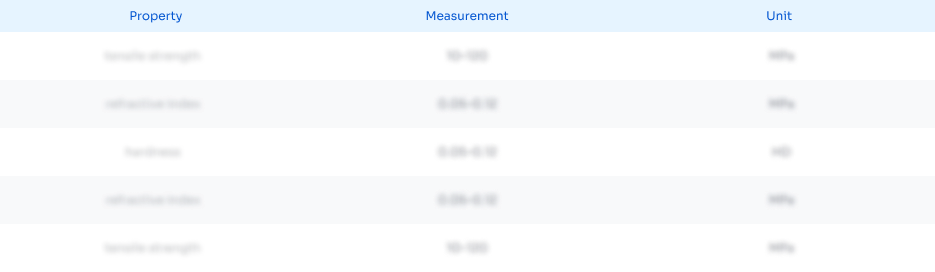
Abstract
Description
Claims
Application Information

- R&D
- Intellectual Property
- Life Sciences
- Materials
- Tech Scout
- Unparalleled Data Quality
- Higher Quality Content
- 60% Fewer Hallucinations
Browse by: Latest US Patents, China's latest patents, Technical Efficacy Thesaurus, Application Domain, Technology Topic, Popular Technical Reports.
© 2025 PatSnap. All rights reserved.Legal|Privacy policy|Modern Slavery Act Transparency Statement|Sitemap|About US| Contact US: help@patsnap.com