Flue gas desulfurization process for comprehensively utilizing sintering flue gas
A technology of sintering flue gas and desulfurization process, which is applied to the improvement of process efficiency, waste heat treatment, lighting and heating equipment, etc. It can solve the problems of adverse impact on the atmospheric environment, waste of resources and energy, increased costs and burdens, and achieve the protection of the atmosphere Environmental quality, saving energy and resources, beneficial to the effect of dilution and diffusion
- Summary
- Abstract
- Description
- Claims
- Application Information
AI Technical Summary
Problems solved by technology
Method used
Image
Examples
Embodiment
[0024] Such as Figure 5 Shown is the flue gas desulfurization process of the present invention, which is used for the flue gas desulfurization of the iron ore sintering process. Sintering machine (effective sintering area is 360m 2 ) The roasted sinter passes through the ring cooler (the cooling air volume is about 2300000Nm 3 / h) After cooling, the grains are sized and then sent to the blast furnace by a belt conveyor. The sintering flue gas (130°C ~ 180°C) discharged from the sintering process of the sintering machine is sent to the regeneration tower after being pressurized by the booster fan. In the regeneration tower, the desulfurization-rich liquid is indirectly heated by the sintering flue gas to decompose sulfur dioxide with a purity of 99.5%. The decomposed sulfur dioxide is drawn out from the top of the regeneration tower along with a large amount of water vapor. concentrated sulfuric acid). The desulfurization-rich liquid is converted into absorption liquid aft...
PUM
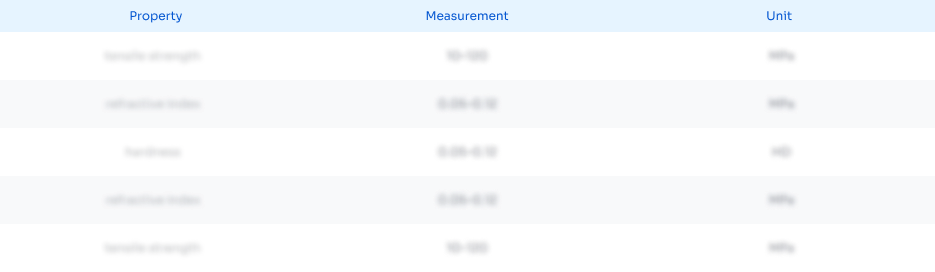
Abstract
Description
Claims
Application Information

- R&D
- Intellectual Property
- Life Sciences
- Materials
- Tech Scout
- Unparalleled Data Quality
- Higher Quality Content
- 60% Fewer Hallucinations
Browse by: Latest US Patents, China's latest patents, Technical Efficacy Thesaurus, Application Domain, Technology Topic, Popular Technical Reports.
© 2025 PatSnap. All rights reserved.Legal|Privacy policy|Modern Slavery Act Transparency Statement|Sitemap|About US| Contact US: help@patsnap.com