Epoxy/organosilicon/inorganic nano-hybrid material, and preparation method and application thereof
A technology of inorganic nano and hybrid materials, applied in the direction of epoxy resin coatings, applications, epoxy resin adhesives, etc., can solve the problems of difficult to obtain transparent inorganic nano-modified polymers, thermal stability, poor light resistance, and difficulties in solvent purification And other problems, to achieve high weather resistance, good heat resistance, good adhesion effect
- Summary
- Abstract
- Description
- Claims
- Application Information
AI Technical Summary
Problems solved by technology
Method used
Image
Examples
Embodiment 1
[0051] Epoxy / organosilicon / inorganic nano-hybrid material formula 1
[0052] Composition Dosage (parts)
[0053] Hydrogenated bisphenol A epoxy resin 100
[0054] Hydroxypolyphenylsilsesquioxane 70
[0055] Epoxysilane 20
[0056] Acid Nano Silica 60
[0057] In the reactor, add 50 parts of hydrogenated bisphenol A epoxy resin (EPONEX 1510), 70 parts of hydroxyl polyphenylsilsesquioxane with an average molecular weight of 5000, stir for 2 hours, add 20 parts of epoxy silane (GF-82 ), and continued to stir for 0.5 hours to obtain component A for use.
[0058] In the reactor, add 50 parts of hydrogenated bisphenol A epoxy resin (EPONEX 1510), 60 parts of acidic nano-silica, stir for 20 hours, add component A, and continue stirring for 1 hour to obtain epoxy / organic silicon / inorganic nanohybrid materials.
[0059] The epoxy / organosilicon / inorganic nano-hybrid material was heated at 150° C. for 2 hours, and cured in situ to obtain the epoxy / organic silicon / inorganic nano-hyb...
Embodiment 2
[0061] Epoxy / organosilicon / inorganic nano-hybrid material formula 2
[0062] Composition Dosage (parts)
[0063] Hydrogenated bisphenol A epoxy resin 100
[0064] Hydroxypolyphenylsilsesquioxane 2
[0065] Hydroxy silicone oil 5
[0066] Epoxysilane 2
[0067] Acidic nano aluminum oxide 15
[0068] In the reactor, add 50 parts of hydrogenated bisphenol A epoxy resin (GEST3000), 2 parts of hydroxyl polyphenylsilsesquioxane with an average molecular weight of 3500, and 5 parts of hydroxyl silicone oil with an average molecular weight of 10000, stir for 1 hour, and add 2 Part epoxy silane (GLYMO), continue to stir for 1 hour to get A component, stand-by.
[0069] In the reactor, add 50 parts of hydrogenated bisphenol A epoxy resin (GEST3000), 15 parts of acidic nano-alumina, stir for 10 hours, add component A, and continue stirring for 2 hours to obtain epoxy / organic silicon / inorganic nanohybrid materials.
[0070] The epoxy / organosilicon / inorganic nano-hybrid material was...
Embodiment 3
[0072] Epoxy / organosilicon / inorganic nano-hybrid material formulation 3
[0073] Composition Dosage (parts)
[0074] Cycloaliphatic epoxy resin 100
[0075] Hydroxy silicone oil 100
[0076] Nano aluminum dihydrogen phosphate 2
[0077] In the reactor, add 70 parts of cycloaliphatic epoxy resin (ERL-4221), 100 parts of hydroxyl silicone oil with an average molecular weight of 2000, and stir for 5 hours to obtain component A, which is ready for use.
[0078] In the reactor, add 30 parts of cycloaliphatic epoxy resin (ERL-4221), 2 parts of nano-aluminum dihydrogen phosphate, and stir for 2 hours to obtain component B.
[0079] Mix the above components A and B evenly, heat at 50°C for 5 hours, and cure in situ to obtain an epoxy / organic silicon / inorganic nano-hybrid material.
PUM
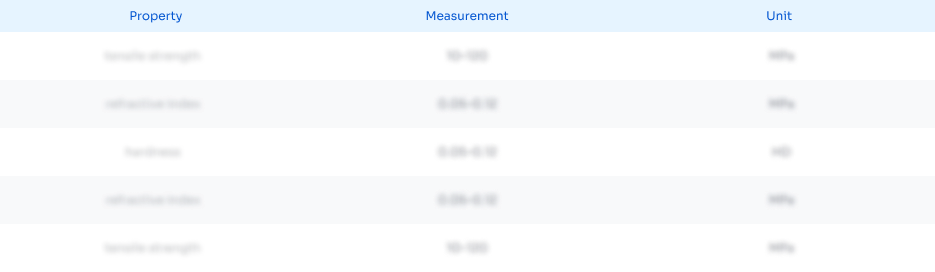
Abstract
Description
Claims
Application Information

- R&D
- Intellectual Property
- Life Sciences
- Materials
- Tech Scout
- Unparalleled Data Quality
- Higher Quality Content
- 60% Fewer Hallucinations
Browse by: Latest US Patents, China's latest patents, Technical Efficacy Thesaurus, Application Domain, Technology Topic, Popular Technical Reports.
© 2025 PatSnap. All rights reserved.Legal|Privacy policy|Modern Slavery Act Transparency Statement|Sitemap|About US| Contact US: help@patsnap.com