Electrophoresis coating technique for fasteners
An electrophoretic coating and fastener technology, applied in electrolytic coatings, electrophoretic plating, coatings, etc., can solve the problems of high cost, no wear resistance, and no environmental protection, and achieve improved corrosion resistance and suitable friction coefficient. Effect
- Summary
- Abstract
- Description
- Claims
- Application Information
AI Technical Summary
Problems solved by technology
Method used
Examples
Embodiment 1
[0027] Adopt process plan 1: the friction coefficient of the paint film is suitable, and does not affect product assembly; such as: fasteners for engines, gearboxes, and wheels.
[0028] The process steps are:
[0029] 1. Zinc phosphating: carried out in a phosphating tank,
[0030] Process parameters: temperature 35±5°C, time 3-5 minutes, keep shaking the sample, washing with water, drying at 80-100°C for 20 minutes,
[0031] 2. Cathodic electrophoresis: carried out in the electrophoresis tank, the bath temperature is 30±2°C, the electrophoresis time is 2-3 minutes, the coating voltage is 140-180 volts, washed with water,
[0032] 3. Drying: Dry at 170-180°C for 40 minutes;
Embodiment 2
[0034] Adopt process plan 2: Except for fasteners with strict torque requirements, it will not affect product assembly; such as: fasteners for connecting brackets.
[0035] The process steps are:
[0036] 1. Electrogalvanizing: coating thickness 6-8μm, electroplating solution temperature 10-40℃, electroplating time 2-3 minutes, cathode current density: 0.8-3A / dm 2 ,
[0037] 2. Cathodic electrophoresis: carried out in the electrophoresis tank, the bath temperature is 30±2°C, the electrophoresis time is 2-3 minutes, the coating voltage is 100-140 volts, washed with water,
[0038] 3. Drying: Dry at 170-180°C for 40 minutes;
Embodiment 3
[0040] Process plan 3: It is suitable for fasteners without torque requirements, such as: fasteners for connecting glove boxes inside the cab.
[0041] The process steps are:
[0042] 1. Electrogalvanizing: coating thickness 6-8μm, electroplating solution temperature 10-40℃, electroplating time 2-3 minutes, cathode current density: 0.8-3A / dm 2 .
[0043] 2. Zinc phosphating: carried out in a phosphating tank,
[0044] Process parameters: temperature 35±5°C, time 3-5 minutes, keep shaking the sample, washing with water, drying at 80-100°C for 20 minutes.
[0045] 3. Cathodic electrophoresis: carried out in the electrophoresis tank, the bath temperature is 30±2°C, the electrophoresis time is 2-3 minutes, the coating voltage is 140-180 volts, washed with water,
[0046] 4. Drying: Dry at 170-180°C for 40 minutes.
PUM
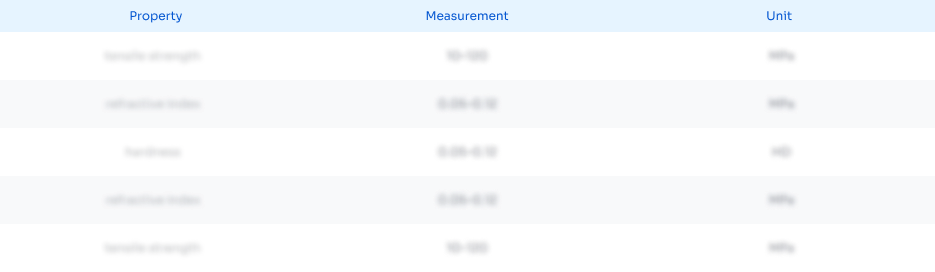
Abstract
Description
Claims
Application Information

- R&D
- Intellectual Property
- Life Sciences
- Materials
- Tech Scout
- Unparalleled Data Quality
- Higher Quality Content
- 60% Fewer Hallucinations
Browse by: Latest US Patents, China's latest patents, Technical Efficacy Thesaurus, Application Domain, Technology Topic, Popular Technical Reports.
© 2025 PatSnap. All rights reserved.Legal|Privacy policy|Modern Slavery Act Transparency Statement|Sitemap|About US| Contact US: help@patsnap.com