Activated sintering preparation method of fine crystalline non-magnetic wolfram-copper alloy
A technology of activating sintering and copper alloys, which is applied in the field of activating sintering preparation of fine-grained non-magnetic tungsten-copper alloys, can solve the problems that it is difficult to achieve uniform distribution of tungsten-copper phases, complex processes, and difficult industrialization, etc., and achieve excellent mechanical properties. Performance and thermal conductivity, simple process, no pollution effect
- Summary
- Abstract
- Description
- Claims
- Application Information
AI Technical Summary
Problems solved by technology
Method used
Image
Examples
Embodiment 1
[0038] Embodiment 1: prepare W-5Cu composite powder according to the preparation method of the tungsten-copper composite powder of high-density alloy whose application number is 200610124767.0, the average grain size of W in the composite powder is 250nm; the composite powder is compression molded, and the molding agent is 2wt.% solid paraffin, molding pressure is 20MPa, cold isostatic pressing, pressure is 200MPa, green body size is 30mm×10mm×6mm. The green body is sintered in a high temperature tube furnace. First, use high-purity nitrogen to discharge the air in the tube furnace, and then introduce hydrogen, the flow rate of hydrogen is 500ml / min, and the temperature is raised to 375°C at a heating rate of 5°C / min, and the molding agent is removed by keeping it for 1 hour; then, at 5°C Raise the temperature to 800°C at a heating rate of 5°C / min and keep it warm for 1 hour; continue to raise the temperature to 900°C at a heating rate of 5°C / min and keep warm for 1 hour; then...
Embodiment 2
[0039] Embodiment 2: Prepare W-15Cu composite powder according to the preparation method of the tungsten-copper composite powder of high-density alloy whose application number is 200610124767.0, the average grain size of W in the composite powder is 250nm; the composite powder is compression molded, and the forming agent is 1wt.% liquid paraffin, the molding pressure is 15MPa, cold isostatic pressing, the pressure is 180MPa, and the green body size is 30mm×10mm×6mm. The green body is sintered in a high temperature tube furnace. First, high-purity nitrogen is used to discharge the air in the tube furnace, and then a mixed gas of hydrogen and high-purity argon is introduced, the volume ratio is 5:1, the gas flow rate is 500ml / min, and the temperature is raised to 5°C / min. 380°C, hold for 1 hour to remove the molding agent; then raise the temperature to 800°C at a heating rate of 5°C / min, and hold for 1 hour; continue to raise the temperature to 900°C at a heating rate of 5°C / min...
Embodiment 3
[0040] Embodiment 3: prepare W-45Cu composite powder according to the preparation method of the tungsten-copper composite powder of high-density alloy whose application number is 200610124767.0, the average grain size of W in the composite powder is 250nm; the composite powder is compression molded, and the forming agent is 2wt.% polyvinyl alcohol, molding pressure is 40MPa, cold isostatic pressing treatment, pressure is 150MPa, green body size is 30mm×10mm×6mm. The green body is sintered in a high temperature tube furnace. First use high-purity nitrogen to discharge the air in the tube furnace, and then introduce a mixed gas of hydrogen and high-purity nitrogen, the volume ratio is 5:1, the gas flow rate is 500ml / min, and the temperature is raised to 400°C at a heating rate of 5°C / min. , keep warm for 1 hour to remove the molding agent; then raise the temperature to 800°C at a heating rate of 5°C / min, and keep warm for 1 hour; continue to raise the temperature to 900°C at a h...
PUM
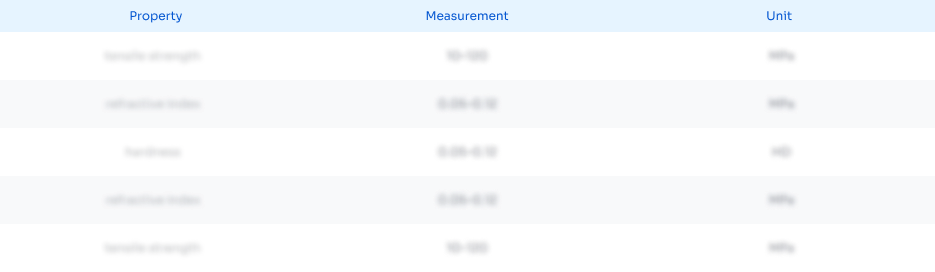
Abstract
Description
Claims
Application Information

- R&D
- Intellectual Property
- Life Sciences
- Materials
- Tech Scout
- Unparalleled Data Quality
- Higher Quality Content
- 60% Fewer Hallucinations
Browse by: Latest US Patents, China's latest patents, Technical Efficacy Thesaurus, Application Domain, Technology Topic, Popular Technical Reports.
© 2025 PatSnap. All rights reserved.Legal|Privacy policy|Modern Slavery Act Transparency Statement|Sitemap|About US| Contact US: help@patsnap.com