Alkaline oxygen converter steelmaking slagging fluxing agent and its preparing method and slagging method
An oxygen converter and flux technology, which is applied in the direction of manufacturing converters, etc., can solve the problems of the converter lining refractory being subjected to more, unfavorable CaO smelting effect, and unfavorable converter smelting efficiency, so as to reduce the consumption of lime, shorten the smelting cycle, improve the The effect of steelmaking efficiency
- Summary
- Abstract
- Description
- Claims
- Application Information
AI Technical Summary
Problems solved by technology
Method used
Image
Examples
Embodiment 1
[0021] Implementation example 1 - low-silicon hot metal smelting high-carbon steel The amount of slag-forming flux added is 10kg / t steel, replacing all the fluorite and bauxite in the original slag-making materials:
[0022] The slagging flux is prepared from boron mud and industrial reagents from a borax factory in Dandong, Liaoning. The preparation process is as follows: boron mud is sintered in a sintering kiln at 200-400 ° C for 1 hour, fully dehydrated, and its composition is determined by chemical analysis method: B 2 o 3 4.1%, CaO 44.9%, MgO 25.5%, Al 2 o 3 15.3%, Fe 2 o 3 10.2%, take anhydrous boric anhydride with a boron mud content of 1.9%, grind it and mix it with boron mud, grind it into a fine powder below 0.1mm, granulate it to make a spherical material of 5-30mm, and dry it at 200°C. use.
[0023] On 100 tons of converters, the slagging flux (composed of: B) prepared above is adopted 2 o 3 6%, MgO 25%, CaO 44%, Al 2 o 3 15%, Fe 2 o 3 10%) slag,...
Embodiment 2
[0027] Implementation example 2 - high-silicon hot metal smelting high-carbon steel The amount of slag-forming flux added is 6kg / t steel, replacing all the fluorite and bauxite in the original slag-making materials:
[0028] The slagging flux is prepared from borax mud and industrial reagents from a borax factory in Dandong. The preparation process is as follows: boron mud is sintered in a sintering kiln at 200-400°C for about 1 hour, fully dehydrated, and its composition is determined by chemical analysis method: B 2 o 3 4.1%, CaO 44.9%, MgO 25.5%, Al 2 o 3 15.3%, Fe 2 o 3 10.2%, take anhydrous boric anhydride with boron mud content of 0.9%, grind it and mix it with boron mud, grind it into a fine powder below 0.1mm, granulate it into a spherical material of 5-30mm, and dry it at 200°C. use.
[0029] On the 100-ton converter, the above-mentioned slagging flux (composed of: B 2 o 3 5%, CaO 45%, MgO 25%, Al 2 o 3 15%, Fe 2 o 3 10%) slag, when the initial Si con...
Embodiment 3
[0034] Implementation Example 3 - Addition amount of low-carbon steel slag-forming flux in high-silicon hot metal smelting 2kg / t steel for low-carbon steel, 3-5kg / t steel for medium-carbon steel, replacing all fluorite and iron in the original slag-making materials Bauxite:
[0035] The preparation method and process of fluxing agent: by industrial reagent: boric anhydride (B 2 o 3 ) 10%, quicklime (CaO) 45%, magnesia (MgO) 20%, corundum powder (Al 2 o 3 ) 15% and iron scale (Fe 2 o 3 ) 10% preparation. The raw materials are weighed and dried at 200°C. After weighing, batching, crushing, mixing, and grinding into fine powders below 0.1mm, granulate to make spherical materials of 5-30mm, and dry them for use;
[0036] On a 100-ton converter, using the above-mentioned slagging flux to dissolve slag, when the initial Si content in molten steel is 0.7% (high-silicon molten iron), smelting 45 # For steel (medium carbon steel, C content 0.45%), the loading amount of metal mat...
PUM
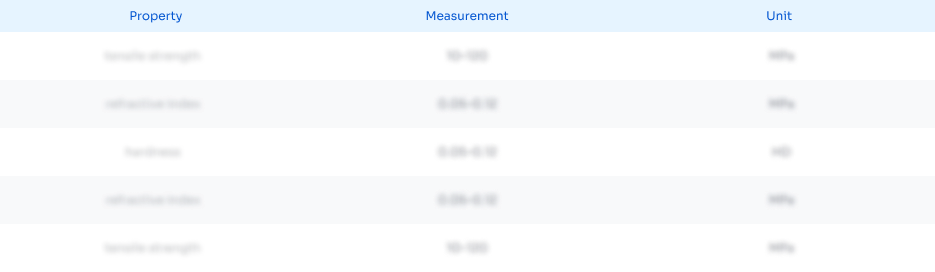
Abstract
Description
Claims
Application Information

- R&D
- Intellectual Property
- Life Sciences
- Materials
- Tech Scout
- Unparalleled Data Quality
- Higher Quality Content
- 60% Fewer Hallucinations
Browse by: Latest US Patents, China's latest patents, Technical Efficacy Thesaurus, Application Domain, Technology Topic, Popular Technical Reports.
© 2025 PatSnap. All rights reserved.Legal|Privacy policy|Modern Slavery Act Transparency Statement|Sitemap|About US| Contact US: help@patsnap.com