Method of preparing ordered porous titanium oxide doped with nitrogen
A technology of porous titanium dioxide and titanium oxide, applied in the direction of titanium dioxide, chemical instruments and methods, titanium oxide/hydroxide, etc., can solve the problems of uneven pore size of porous titanium dioxide, complex preparation process, poor stability of powder catalyst, etc. Poor stability, simple preparation process, and the effect of overcoming easy poisoning
- Summary
- Abstract
- Description
- Claims
- Application Information
AI Technical Summary
Problems solved by technology
Method used
Image
Examples
Embodiment 1
[0019] Disperse 1.5g of monodisperse PS microspheres in 15g of formamide. After the PS microspheres are fully dispersed, add 5g of hexane and 0.01g of butyl titanate, stir thoroughly for 6h, and then volatilize naturally in the air to remove the hexane. Then add 5g of water to hydrolyze butyl titanate. After the hydrolysis is completed, use a G4 sand core funnel to carry out suction filtration. Put the composite of titanium dioxide and monodisperse PS microspheres obtained after suction filtration into a vacuum oven and dry at 60°C. 12h, and then sintered at 500°C for 5h to remove monodisperse PS microspheres to obtain ordered porous titanium dioxide micropowders; then put the ordered porous titanium dioxide micropowders into a microwave plasma generator, and evacuate to a vacuum degree of 45 mm Hg, Pass nitrogen gas into the microwave plasma generator, adjust the nitrogen flow rate to 10cm 3 / min, microwave power 200W, temperature 500°C, and irradiation treatment for 60min, t...
Embodiment 2
[0021] Disperse 1.1 g of monodisperse PS microspheres in 20 g of formamide. After the PS microspheres are fully dispersed, add 4 g of hexane and 0.01 g of methyl titanate, stir thoroughly for 6 hours, and then volatilize naturally in the air to remove the hexane. Then add 7g of water to hydrolyze methyl titanate. After the hydrolysis is completed, use a G4 sand core funnel to carry out suction filtration. Put the composite of titanium dioxide and monodisperse PS microspheres obtained after suction filtration into a vacuum oven and dry at 60°C. 12h, and then sintered at 500°C for 5h to remove monodisperse PS microspheres to obtain ordered porous titanium dioxide micropowders; then put the ordered porous titanium dioxide micropowders into a microwave plasma generator, and evacuate to a vacuum degree of 45 mm Hg, Pass nitrogen gas into the microwave plasma generator, adjust the nitrogen flow rate to 20cm 3 / min, microwave power 500W, temperature 500°C, and irradiation treatment f...
Embodiment 3
[0023] Disperse 0.1g of monodisperse PMMA microspheres in 12g of formamide. After the PMMA microspheres are fully dispersed, add 3g of hexane and 0.02g of ethyl titanate, stir thoroughly for 6h, and then volatilize naturally in the air to remove hexane. Then add 5g of water to hydrolyze the ethyl titanate. After the hydrolysis is completed, use a G4 sand core funnel to carry out suction filtration. Put the composite of titanium dioxide and monodisperse PMMA microspheres obtained after suction filtration into a vacuum oven and dry at 60°C. 12h, and then sintered at 500°C for 5h to remove monodisperse PMMA microspheres to obtain ordered porous titanium dioxide micropowders; then put the ordered porous titanium dioxide micropowders into a microwave plasma generator, and evacuate to a vacuum degree of 45 mm Hg, Pass nitrogen gas into the microwave plasma generator, adjust the nitrogen flow rate to 30cm 3 / min, microwave power 600W, temperature 300°C, and irradiation treatment for ...
PUM
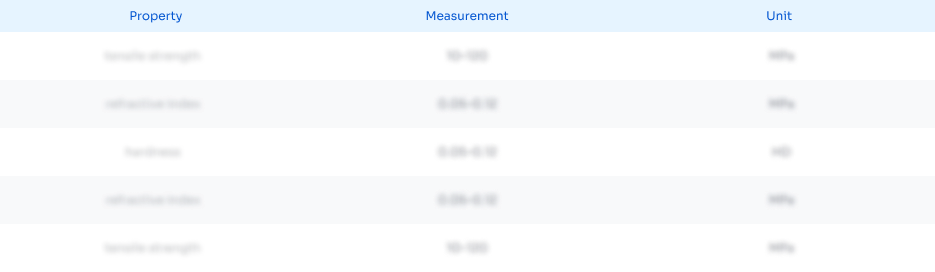
Abstract
Description
Claims
Application Information

- Generate Ideas
- Intellectual Property
- Life Sciences
- Materials
- Tech Scout
- Unparalleled Data Quality
- Higher Quality Content
- 60% Fewer Hallucinations
Browse by: Latest US Patents, China's latest patents, Technical Efficacy Thesaurus, Application Domain, Technology Topic, Popular Technical Reports.
© 2025 PatSnap. All rights reserved.Legal|Privacy policy|Modern Slavery Act Transparency Statement|Sitemap|About US| Contact US: help@patsnap.com