Aramid fiber reinforced PPESK base composite material interfacial modifying method
A polyaryl ether sulfone ketone, aramid fiber technology, applied in the fiber type, fiber treatment, ultrasonic/sonic fiber treatment and other directions, can solve the problems of low lateral strength and easy fracture
- Summary
- Abstract
- Description
- Claims
- Application Information
AI Technical Summary
Problems solved by technology
Method used
Image
Examples
Embodiment 1
[0023] Wrap the Armoc aramid fiber evenly on the glass frame, place it in the central area of the cavity of the radio frequency inductively coupled microwave plasma (ICP) device, turn on the vacuum pump to draw the vacuum of the plasma cavity below 1Pa, and adjust the gas inlet The mass flow controller makes the oxygen flow rate to be 60-90sccm, and the air pressure is kept at 30-40Pa, and the plasma output power is 200W for 10 minutes, and the fiber is quickly taken out by continuous winding method and polyarylether sulfone ketone resin (PPESK) solution is compounded to make unidirectional fiber prepreg, and the Armoc aramid fiber reinforced PPESK unidirectional composite material is prepared according to the following process:
[0024] Armoc aramid fiber→plasma treatment→prepreg→drying→
[0025] Fiber prepreg sheet → hot pressing → demoulding → unidirectional board → test piece
[0026] The process of making fiber prepreg is as follows:
[0027] resin concentrat...
Embodiment 2
[0032] Wrap the Armoc aramid fiber evenly on the glass frame, place it in the central area of the cavity of the radio frequency inductively coupled microwave plasma (ICP) device, turn on the vacuum pump to draw the vacuum of the plasma cavity below 1Pa, and adjust the gas inlet The mass flow controller makes the oxygen flow rate to be 60-90sccm, and the air pressure is kept at 30-40Pa, and the plasma output power is 200W for 10 minutes, and the fiber is quickly taken out by continuous winding method and polyarylether sulfone ketone resin (PPESK) solution compounded into a unidirectional fiber prepreg, and the Armoc aramid fiber reinforced PPESK unidirectional composite material was prepared according to the process flow of Example 1.
[0033] The process of making fiber prepreg is as follows:
[0034] resin concentration
Dipping temperature
traction speed
Squeegee stick spacing
drying temperature
drying time
50%
...
Embodiment 3
[0038] Wrap the Armoc aramid fiber evenly on the glass frame, place it in the central area of the cavity of the radio frequency inductively coupled microwave plasma (ICP) device, turn on the vacuum pump to draw the vacuum of the plasma cavity below 1Pa, and adjust the gas inlet The mass flow controller keeps the air flow at 60-90sccm and the air pressure at 30-40Pa, and treats it for 10 minutes under the plasma output power of 200W, and takes out the fiber rapidly by continuous winding method and polyarylether sulfone ketone resin (PPESK) solution compounded into a unidirectional fiber prepreg, and the Armoc aramid fiber reinforced PPESK unidirectional composite material was prepared according to the process flow of Example 1.
[0039] The process of making fiber prepreg is as follows:
[0040] resin concentration
Dipping temperature
traction speed
Squeegee stick spacing
drying temperature
5-50%
1.0m / ...
PUM
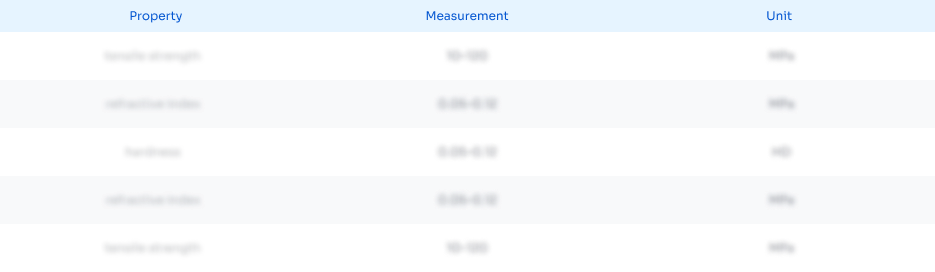
Abstract
Description
Claims
Application Information

- Generate Ideas
- Intellectual Property
- Life Sciences
- Materials
- Tech Scout
- Unparalleled Data Quality
- Higher Quality Content
- 60% Fewer Hallucinations
Browse by: Latest US Patents, China's latest patents, Technical Efficacy Thesaurus, Application Domain, Technology Topic, Popular Technical Reports.
© 2025 PatSnap. All rights reserved.Legal|Privacy policy|Modern Slavery Act Transparency Statement|Sitemap|About US| Contact US: help@patsnap.com