Aluminium front cover and manufacturing process thereof
A manufacturing process and aluminum alloy technology, which is applied in the field of aluminum alloy front cover and its manufacturing process, can solve the problems of high engine temperature, non-dense internal structure, and many pores, so as to improve work performance, reduce production costs, and compact internal structure Effect
- Summary
- Abstract
- Description
- Claims
- Application Information
AI Technical Summary
Problems solved by technology
Method used
Examples
Embodiment Construction
[0007] The aluminum alloy front cover material of the present invention (brand is RM-AC4B) chemical composition is calculated by weight, and it is constituted as: 7.8-8.2% silicon (Si), 2.6-3.0% copper (Cu), 0.25-0.35% magnesium (Mg) , 0.28-0.38% manganese (Mn), and the balance is aluminum (Al).
[0008] The chemical composition of the aluminum alloy front cover is calculated by weight, and its impurity content is not more than: 0.45% iron (Fe), 0.3% zinc (Zn), 0.2% lead (Pb), 0.2% chromium (Cr), 0.1% Tin (Sn), 0.1% nickel (Ni), 0.1% titanium (Ti).
[0009] The manufacturing process of the above-mentioned aluminum alloy front cover is as follows: first prepare the mold of the front cover (the mold can be reused more than 80,000 times) and its water circulation channel sand core (including No. 1, No. 2, and No. 3 water circulation channel sand cores, It can only be used once) to be used; then the aluminum alloy raw material prepared according to the above ratio is directly sme...
PUM
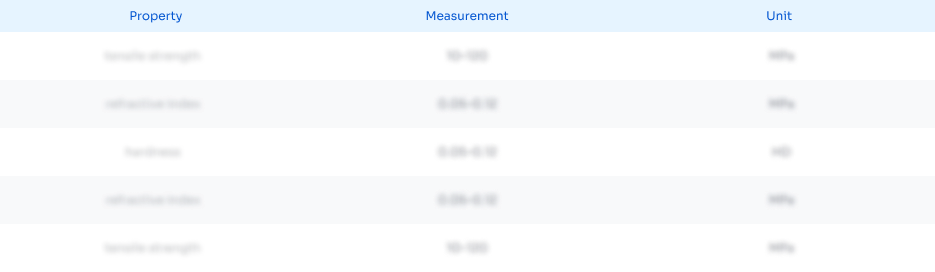
Abstract
Description
Claims
Application Information

- R&D
- Intellectual Property
- Life Sciences
- Materials
- Tech Scout
- Unparalleled Data Quality
- Higher Quality Content
- 60% Fewer Hallucinations
Browse by: Latest US Patents, China's latest patents, Technical Efficacy Thesaurus, Application Domain, Technology Topic, Popular Technical Reports.
© 2025 PatSnap. All rights reserved.Legal|Privacy policy|Modern Slavery Act Transparency Statement|Sitemap|About US| Contact US: help@patsnap.com