Method for preparing surface patterned SiO2 high molecular composite microsphere
A technology of silicon dioxide and composite microspheres, applied in the field of chemistry or physics, can solve the problems of complex preparation process of layer-by-layer assembly method, difficult to form single type particles, difficult to form structural composite materials, etc., and achieves feasible process and low quality. , the effect of short response time
- Summary
- Abstract
- Description
- Claims
- Application Information
AI Technical Summary
Problems solved by technology
Method used
Image
Examples
Embodiment 1
[0040] 1. Preparation of mixed surfactants
[0041] Mix Span-80 and Tween-80 at a weight ratio of 5:1 to prepare a mixed surfactant.
[0042] 2. Preparation of synthetic template oil phase
[0043] Add the mixed surfactant prepared in step 1 into a three-necked flask filled with n-heptane, and mix the mixed surfactant and n-heptane at a weight ratio of 1:122 to prepare a synthetic template oil phase.
[0044] 3. Preparation of emulsion
[0045] Put the synthetic template oil phase prepared in step 2 into a three-necked flask, stir with a stirrer at a stirring speed of 360-400 rpm, and inject N at a flow rate of 2-3 mL / min. 2 , emulsified at 25°C for 40-60 minutes to make an emulsion.
[0046] 4. Preparation of water phase
[0047] Mix N,N'-methylene dienamide, ammonium persulfate, and N-isopropylacrylamide in a molar ratio of 1:1.17:28.3, stir evenly, and prepare solution A. The molar ratio of acrylic acid and NaOH is 1:0.6 to prepare acrylic acid aqueous solution with a ...
Embodiment 2
[0057] In this embodiment, in step 2 of the process of preparing the synthetic template oil phase, the mixed surfactant and n-heptane were mixed at a weight ratio of 1:115 to prepare the synthetic template oil phase. In the process step 3 of preparing the emulsion, the emulsification temperature is 18°C. In step 4 of the preparation of the aqueous phase, the molar ratio of acrylic acid and NaOH is 1:0.3 to prepare an aqueous acrylic acid solution with a concentration of 23%. In Step 6 of the process for preparing the swollen copolymerized microgel, the microgel was swelled with ammonia water at a concentration of 9%. In step 8 of the process of preparing surface-patterned silica polymer composite microspheres, the reaction temperature is 18°C. Other processing steps are identical with embodiment 1.
Embodiment 3
[0059] In this embodiment, in step 2 of the process of preparing the synthetic template oil phase, the mixed surfactant and n-heptane were mixed at a weight ratio of 1:130 to prepare the synthetic template oil phase. In the process step 3 of preparing the emulsion, the emulsification temperature is 30°C. In step 4 of the preparation of the aqueous phase, the molar ratio of acrylic acid and NaOH is 1:1 to prepare an aqueous acrylic acid solution with a concentration of 23%. In step 6 of the process of preparing the swollen copolymerized microgel, the microgel was swollen with ammonia water at a concentration of 28%. In step 8 of the process of preparing surface-patterned silica polymer composite microspheres, the reaction temperature is 34°C. Other processing steps are identical with embodiment 1.
[0060] In order to determine the best processing step of the present invention, the inventor has carried out a large amount of laboratory research tests, and various test situatio...
PUM
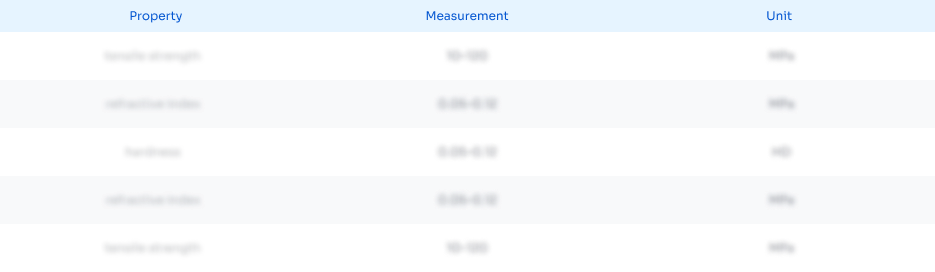
Abstract
Description
Claims
Application Information

- R&D Engineer
- R&D Manager
- IP Professional
- Industry Leading Data Capabilities
- Powerful AI technology
- Patent DNA Extraction
Browse by: Latest US Patents, China's latest patents, Technical Efficacy Thesaurus, Application Domain, Technology Topic, Popular Technical Reports.
© 2024 PatSnap. All rights reserved.Legal|Privacy policy|Modern Slavery Act Transparency Statement|Sitemap|About US| Contact US: help@patsnap.com