TiN two-layer film cladding for cutting tool material surface and its preparing method
A double-layer film and cutting tool technology, which is applied in the coating process of metal materials, turning equipment, tool holder accessories, etc., to achieve good wear resistance, eliminate adverse effects, and relieve stress changes.
- Summary
- Abstract
- Description
- Claims
- Application Information
AI Technical Summary
Problems solved by technology
Method used
Image
Examples
Embodiment 1
[0029] AIP---01 type multi-arc ion coating machine is adopted, and a magnetic filter device is attached to the coating machine. Both the coating machine and the magnetic filtering device can be purchased from the market, and the magnetic filtering device is manufactured by the Institute of Low Energy Nuclear Physics of Beijing Normal University; The multi-arc ion coating machine is manufactured by Shenyang Yuankehang Company; the workpiece used is the finished high-speed steel tool purchased from Harbin Renji Measuring Tool Factory, and then cut into 12×12×6mm squares by wire.
[0030] (1) First, the workpiece is mechanically ground and polished and cleaned before plating, that is, the workpiece is placed in a 10% NaOH solution and cleaned with ultrasonic waves for 30 minutes to remove the oil on the surface of the workpiece; Remove rust and activate the surface at the same time; dehydrate and dry with alcohol;
[0031] (2) Put the dried workpiece into the AIP---01 multi-arc i...
Embodiment 2
[0038] Device and workpiece are with embodiment 1.
[0039] (1) First, the workpiece is mechanically ground and polished and cleaned before plating, that is, the workpiece is placed in a 10% NaOH solution and cleaned with ultrasonic waves for 30 minutes to remove the oil on the surface of the workpiece; Remove rust and activate the surface at the same time; dehydrate and dry with alcohol;
[0040] (2) Put the dried workpiece into the AIP---01 multi-arc ion coating machine, and put the polished side of the workpiece at 100mm from the outlet of the magnetic filter elbow, and let the plasma bombard the surface of the sample;
[0041] (3) Set the temperature range of the heating tube in the vacuum chamber to 240°C to 260°C, and then use mechanical pumps, Roots pumps, and diffusion pumps to evacuate step by step. When the pressure in the vacuum chamber drops to 6.5×10 -3 When Pa or above, turn on the power cooling water and coating power supply, adjust the cleaning bias to -800V, ...
PUM
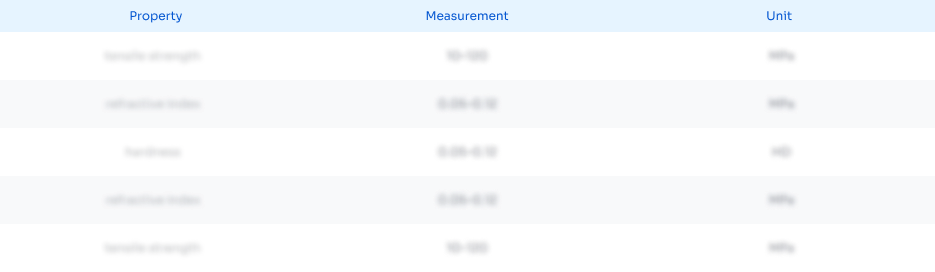
Abstract
Description
Claims
Application Information

- Generate Ideas
- Intellectual Property
- Life Sciences
- Materials
- Tech Scout
- Unparalleled Data Quality
- Higher Quality Content
- 60% Fewer Hallucinations
Browse by: Latest US Patents, China's latest patents, Technical Efficacy Thesaurus, Application Domain, Technology Topic, Popular Technical Reports.
© 2025 PatSnap. All rights reserved.Legal|Privacy policy|Modern Slavery Act Transparency Statement|Sitemap|About US| Contact US: help@patsnap.com