Modified polyurethane composition and preparation thereof
A technology of composition and polyurethane, which is applied in the direction of building structure, building components, building insulation materials, etc., can solve the problem that the mechanical strength and dielectric strength of the product cannot fully reach the best state, poor electrical insulation performance, and low dielectric strength and other issues, to achieve the effect of wide source of raw materials, improved flame retardancy, and high dielectric strength
- Summary
- Abstract
- Description
- Claims
- Application Information
AI Technical Summary
Problems solved by technology
Method used
Examples
specific Embodiment approach 1
[0013] First, 150 grams of propylene oxide homopolyether-2000; 8 grams of ethylenediamine polyether-403; 80 grams of castor oil are added in a 500ml reaction kettle equipped with a stirrer, a temperature controller and a water cooler, and heated Stir to heat up and start vacuuming. When the temperature rises to 140-150°C, keep the vacuum degree greater than 700mmHg, continue vacuuming for 2.0-3.0 hours, and then cool to room temperature; add 60 grams of trichloroethylene; toluene diisocyanate (TDI- 80) 90 g; Stir and heat up to 60°C-80°C, react at constant temperature for 2.0-3.0 hours and cool down to obtain component A, which is sealed and stored.
[0014] Secondly, in a 500ml reactor equipped with a stirrer, a temperature controller and a water cooler, add 140 grams of 3,3'-dichloro-4,4'diphenyldiaminomethane; Then add 340 grams of tetrahydrofuran to dissolve it, add 20 grams of hard coal tar pitch, stir and dissolve, then take 80 grams of dimethyl methylphosphonate; for di...
specific Embodiment approach 2
[0016] According to the method of specific embodiment 1, propylene oxide homopolyether-2000 140 grams in A component; Ethylenediamine polyether-403 6 grams; Castor oil 70 grams; Trichlorethylene 50 grams; Toluene diisocyanate (TDI-80) 80 grams; 130 grams of 3,3-dichloro-4,4'diphenyldiaminomethane in component B; 80 grams of dimethyl methylphosphonate; 7 grams of adipic acid; 40 grams of modified resin additives; 300 grams of tetrahydrofuran; 10 grams of hard coal tar pitch to obtain high dielectric strength polyurethane resin products.
specific Embodiment approach 3
[0017] According to the method of Embodiment 1, 160 grams of polyether-2000 in component A; 10 grams of amine ether-403; 90 grams of castor oil, 70 grams of trichlorethylene; 100 grams of toluene diisocyanate (TDI-80) 150 grams of 3,3'-dichloro-4,4'diphenyldiaminomethane in component B; 100 grams of dimethyl methylphosphonate; 10 grams of adipic acid; 640 grams of resin additives , 400 grams of tetrahydrofuran, and 30 grams of hard coal pitch to obtain high dielectric strength polyurethane resin composition products.
PUM
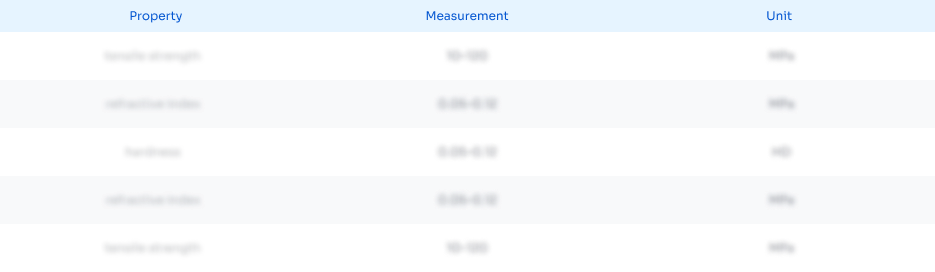
Abstract
Description
Claims
Application Information

- Generate Ideas
- Intellectual Property
- Life Sciences
- Materials
- Tech Scout
- Unparalleled Data Quality
- Higher Quality Content
- 60% Fewer Hallucinations
Browse by: Latest US Patents, China's latest patents, Technical Efficacy Thesaurus, Application Domain, Technology Topic, Popular Technical Reports.
© 2025 PatSnap. All rights reserved.Legal|Privacy policy|Modern Slavery Act Transparency Statement|Sitemap|About US| Contact US: help@patsnap.com