Nano level cementing material in use for foundry sand, preparation method and usage
A binder and casting mold technology, applied in casting molding equipment, casting molds, cores, etc., can solve the problems of fast curing rate, insufficient strength to meet the needs of production, low strength, etc., and achieve uniform and dense internal structure. Worker health and good heat resistance
- Summary
- Abstract
- Description
- Claims
- Application Information
AI Technical Summary
Problems solved by technology
Method used
Examples
Embodiment 1
[0038] In the three-necked bottle of 3000ml, add 490 grams of mixed phenol liquid (phenol: cresol=13: 1, weight ratio is the same below), open electric stirrer, add active potassium acetate 20 grams when temperature is 55 ℃ ± 2; When the temperature rises to 63°C, add the first batch of potassium hydroxide (50%, the concentration is the same below) 150 grams, and at the same time add dropwise 850 grams of formaldehyde (37%, the concentration is the same below), and the addition time is controlled at no less than 30 minutes; Then add 65 grams of sodium bentonite, 150 grams of the second batch of potassium hydroxide (50%) and continue to heat up, react at 75-80 ° C for 2.5 hours; add the third batch of potassium hydroxide (50%) 150 grams, and heat up React at 95°C for 1 hour, during which the temperature is controlled within 100-105°C, then use a rotational viscometer to measure the viscosity of the system, once every 10 minutes, until it reaches 50-55 (centipoise / 25°C), and cool...
Embodiment 2
[0041] Add 600 grams of phenol into a 3000ml three-necked bottle, turn on the electric stirrer, add 20 grams of active potassium acetate and 70 grams of sodium bentonite when the temperature is 55 °C ± 2; add the first batch of hydrogen when the temperature rises to 63 °C Potassium oxide (50%) 150 grams, add dropwise formaldehyde (37%) 1000 grams simultaneously, the addition time is controlled at not less than 30 minutes; React at -80°C for 2.5 hours; then add 150 grams of the third batch of potassium hydroxide (50%), heat up to 95°C and react for 1 hour, during which the temperature is controlled within 100-105°C, and then measure the viscosity of the system with a rotational viscometer , once every 10 minutes, until the viscosity reaches 50-55 (centipoise / 25°C), cool down to below 45°C, add 13 grams of silane coupling agent and stir for 30 minutes to obtain alkali phenolic resin.
[0042] temperature(℃)
[0043] Available time (minutes)
Embodiment 3
[0045] Add 480 grams of mixed phenol liquid (phenol:cresol=13:1) in a 3000ml three-necked bottle, turn on the electric stirrer, and add 20 grams of active potassium acetate when the temperature is 55°C±2; continue to heat up and add the first batch Potassium hydroxide (50%) 150 grams, when temperature rises to 63 ℃, start to drop 850 grams of paraformaldehyde (37%), and the addition time is controlled at not less than 30 minutes; Then add calcium-based bentonite 65 grams, the second Continue to heat up after 150 grams of two batches of potassium hydroxide (50%), and react for 2 hours at 75-80°C; add 150 grams of the third batch of potassium hydroxide (50%), and heat up to 95°C for 1 hour, during which Control it within 100-105°C, then measure the viscosity of the system with a rotational viscometer, once every 10 minutes, until the viscosity reaches 50-55 (centipoise / 25°C), cool down to below 40°C, and add 12 grams of silane coupling agent Stir for 30 minutes to obtain alkali ...
PUM
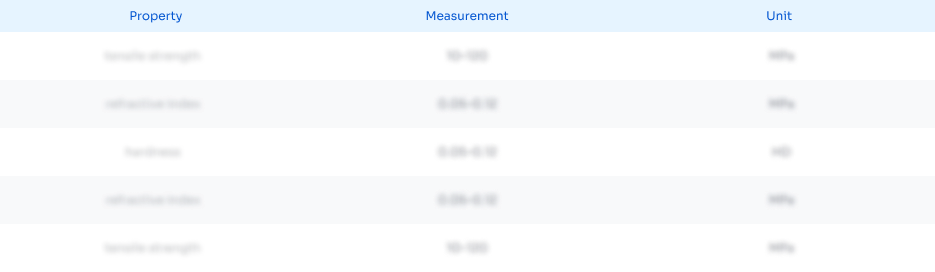
Abstract
Description
Claims
Application Information

- Generate Ideas
- Intellectual Property
- Life Sciences
- Materials
- Tech Scout
- Unparalleled Data Quality
- Higher Quality Content
- 60% Fewer Hallucinations
Browse by: Latest US Patents, China's latest patents, Technical Efficacy Thesaurus, Application Domain, Technology Topic, Popular Technical Reports.
© 2025 PatSnap. All rights reserved.Legal|Privacy policy|Modern Slavery Act Transparency Statement|Sitemap|About US| Contact US: help@patsnap.com