Digital ink jet fabric-treating process
A treatment process, digital inkjet technology, applied in textiles, papermaking, dyeing, etc., can solve the problems of easy photooxidation, troublesome operation, poor light fastness, etc., and achieve the effect of bright colors, good washing, and clear patterns
- Summary
- Abstract
- Description
- Claims
- Application Information
AI Technical Summary
Problems solved by technology
Method used
Examples
Embodiment 1
[0017] Because cotton and wool fabrics have good water holding capacity and the patterns are not easy to permeate, inkjet printing can be carried out directly. It should be noted when printing, because this kind of fabric has poor light reflection ability, the color brightness should be adjusted in terms of image processing. To improve the vividness and color depth of the pattern, you can use the following treatment solution formula for treatment:
[0018] Cationic dye fixing agent 1%
[0019] Water 99%
[0020] Process flow: the fabric is dried after two dips and two rolls (with a reduction rate of 70%), and then inkjet printing is performed. After the printing is finished, the finished product is baked at 150°C for 3 minutes.
Embodiment 2
[0022] Polyester fabric has poor water absorption, and direct water-based pigment ink inkjet printing is prone to bleeding. The following treatment solutions can be used for treatment:
[0023] Polyvinyl alcohol 1%
[0024] Polyethylene glycol 0.2%
[0025] Cetyl trimethyl ammonium chloride 0.3%
[0026] Water 98.5%
[0027] Process flow: the fabric is dried after two dips and two rolls (50% surplus rate), inkjet printing, and then heat-set at 180°C for 30 seconds to obtain the finished product.
[0028] Because polyester has good light reflectivity, the pattern generally does not require special treatment. After the fabric is digitally inkjet printed, it can be rolled with a blanket-type thermal transfer machine at 150°C for 1 minute to get a better hand feeling.
Embodiment 3
[0030] Although the water absorption of silk fabric is good, its water holding capacity is poor, so it can be treated with the following treatment liquid:
[0031] Polyacrylic acid thickener 2%
[0032] Water 98%
[0033] Technological process: the fabric is dried after coating, inkjet printing, and then baked at 130°C for 3 minutes to obtain the finished product.
[0034] The smoothness of silk fabric is better, so the image in inkjet printing is generally focused on highlighting layering. After the digital inkjet printing is finished, it can also be rolled with a blanket-type heat transfer machine at 110°C for 1 min to get a better hand feeling.
PUM
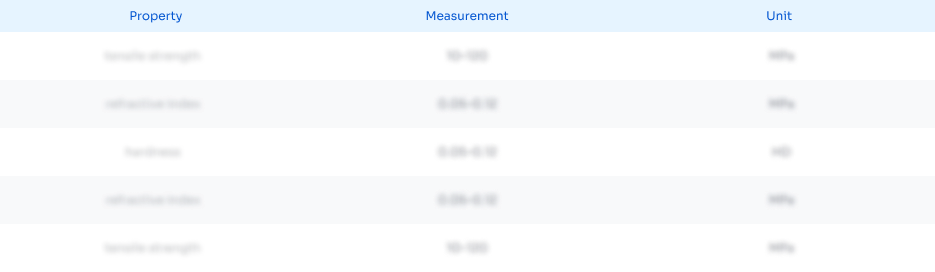
Abstract
Description
Claims
Application Information

- R&D Engineer
- R&D Manager
- IP Professional
- Industry Leading Data Capabilities
- Powerful AI technology
- Patent DNA Extraction
Browse by: Latest US Patents, China's latest patents, Technical Efficacy Thesaurus, Application Domain, Technology Topic, Popular Technical Reports.
© 2024 PatSnap. All rights reserved.Legal|Privacy policy|Modern Slavery Act Transparency Statement|Sitemap|About US| Contact US: help@patsnap.com