Low temperature decrease steel ladle pouring method
A ladle pouring and low temperature technology, which is applied in the direction of casting molten material containers, manufacturing tools, metal processing equipment, etc., can solve the problems of steel performance degradation, high superheat of molten steel in the tundish, etc., and achieve the effect of reducing the consumption of refractory materials
- Summary
- Abstract
- Description
- Claims
- Application Information
AI Technical Summary
Problems solved by technology
Method used
Image
Examples
Embodiment Construction
[0022] The invention will be further described below in conjunction with the accompanying drawings
[0023] 1. Install the cantilever crane
[0024] A cantilever crane is installed near the turret of the continuous casting ladle, and the function of the cantilever crane is to lift the ladle cover with the burner. When the cantilever is hoisted to a high position, ensure that there is a free space of 500mm between the ladle cover and the upper edge of the ladle sitting on the high position of the turntable of the casting machine. After the cantilever crane is lowered, the ladle cover can be covered on the ladle.
[0025] 2. Make the heating bag cover
[0026] The heating burner is installed in the center of the cover. The high-efficiency burner is used to improve the heating efficiency of the flame and ensure the effective heating of the molten steel after the liquid level is lowered. The cover is lined with light-weight refractory materials to reduce the weight of the cover ...
PUM
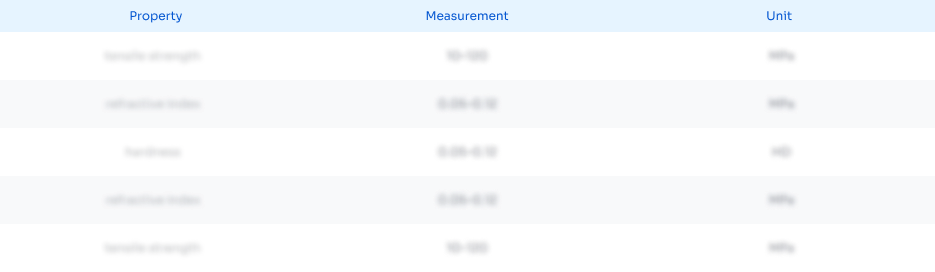
Abstract
Description
Claims
Application Information

- R&D
- Intellectual Property
- Life Sciences
- Materials
- Tech Scout
- Unparalleled Data Quality
- Higher Quality Content
- 60% Fewer Hallucinations
Browse by: Latest US Patents, China's latest patents, Technical Efficacy Thesaurus, Application Domain, Technology Topic, Popular Technical Reports.
© 2025 PatSnap. All rights reserved.Legal|Privacy policy|Modern Slavery Act Transparency Statement|Sitemap|About US| Contact US: help@patsnap.com