Method for producing globular casting tungsten carbide powder by atomising
A technology of casting tungsten carbide and tungsten carbide powder, which is applied in the direction of carbide, tungsten/molybdenum carbide, etc., can solve the problems of large influence on the quality of cooling plate rotation speed, low spheroidization rate, complex production process, etc., and achieve product quality Good quality and spheroidizing effect, good fluidity and filling performance, and convenient operation and control
- Summary
- Abstract
- Description
- Claims
- Application Information
AI Technical Summary
Problems solved by technology
Method used
Examples
Embodiment 1
[0014] In this example, tungsten carbide powder with a total weight of 40% and metal tungsten powder with a weight of 60% are used to prepare a mixed powder, and the particle size of the powder is ≤30 μm; the WC powder contains C: 6.0%, free C: 0.2%, Fe: 0.1%, Cr: 0.05%, V: 0.02%, Si: 0.02%, Ti: 0.05%, MO+CO+Ni: 0.1%; the contents (wt%) of the following elements in metal W powder are Fe: 0.5 , Cr: 0.3, V: 0.02, Si: 0.02, Ti: 0.05, MO+CO+Ni: 0.5;
[0015] In this embodiment, a double intermediate frequency graphite tube furnace is used as the melting furnace. The length of the furnace tube of the melting furnace is 1600mm, the inner diameter of the furnace tube is φ35mm, the diameter of the lower beam hole is φ10mm, the diameter of the inner nozzle is φ30mm, and the outer nozzle is an annular slit nozzle with an inner diameter of φ35mm. Diameter φ36mm, atomization gas adopts argon, pressure 1.5MPa, flow rate 0.25kg / s; intermediate frequency power supply frequency 1800HZ, power ...
Embodiment 2
[0018] In this embodiment, the production of -325 mesh spherical cast tungsten carbide powder is taken as an example. The preparation of raw materials and mixed powder and the melting furnace are the same as in Embodiment 1.
[0019] In this embodiment, the feeding rate during smelting is 10 kg / hour, the protective gas argon pressure is 0.12 MPa; the atomizing gas pressure is 3.0 MPa, and the flow rate is 0.40 kg / second. The molten melt is output from the inner nozzle in the form of melt droplets and is atomized into spherical fine powder under the action of the powerful inert gas flow from the outer nozzle; after passing through a 325 mesh sieve, the sieved product is -325 mesh spherical Cast tungsten carbide products.
PUM
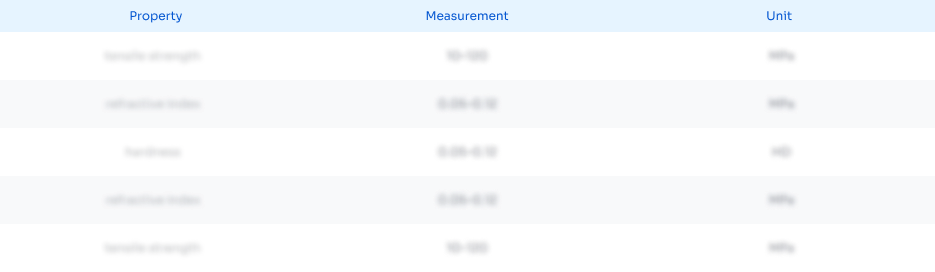
Abstract
Description
Claims
Application Information

- R&D
- Intellectual Property
- Life Sciences
- Materials
- Tech Scout
- Unparalleled Data Quality
- Higher Quality Content
- 60% Fewer Hallucinations
Browse by: Latest US Patents, China's latest patents, Technical Efficacy Thesaurus, Application Domain, Technology Topic, Popular Technical Reports.
© 2025 PatSnap. All rights reserved.Legal|Privacy policy|Modern Slavery Act Transparency Statement|Sitemap|About US| Contact US: help@patsnap.com