Preparation of hexanediamine by hydrogenation of hexane dinitrile
A technology for producing hexamethylenediamine and adiponitrile, applied in chemical instruments and methods, preparation of amino compounds, preparation of organic compounds, etc., can solve problems such as inconvenient operation, large amount of catalyst used, low catalyst activity and selectivity, and achieve Continuous and simple process, low catalyst consumption and good hydrogenation effect
- Summary
- Abstract
- Description
- Claims
- Application Information
AI Technical Summary
Problems solved by technology
Method used
Examples
Embodiment 1
[0019] This example illustrates the preparation of a catalyst useful in the present invention.
[0020] Add 48 grams of nickel, 48 grams of aluminum, 1.5 grams of iron, and 2.5 grams of chromium into the quartz tube, heat it in a high-frequency furnace to above 1300 ° C to melt, and alloy it, and then use inert gas to remove the alloy liquid from The nozzle under the quartz tube is sprayed onto a copper roller with a rotating speed of 800 rpm. Cooling water is passed through the copper roller. After rapid cooling, the alloy liquid is thrown out along the tangent of the copper roller to form scale-like strips. After grinding to a particle diameter of less than 70 microns, a master alloy is obtained. The master alloy is heat-treated in a hydrogen environment, the temperature of the heat treatment is 600° C., and the constant temperature time is 3 hours. The heat-treated master alloy was slowly added into a three-neck flask filled with 500 g of 20% sodium hydroxide aqueous solut...
Embodiment 2
[0022] This example illustrates the preparation of a catalyst useful in the present invention.
[0023] Add 44 grams of nickel, 52 grams of aluminum, 2.5 grams of iron, and 1.5 grams of chromium into the quartz tube, heat it in a high-frequency furnace to above 1300 ° C to melt, and alloy it, and then use inert gas to remove the alloy liquid from The nozzle under the quartz tube is sprayed onto a copper roller with a rotating speed of 800 rpm. Cooling water is passed through the copper roller. After rapid cooling, the alloy liquid is thrown out along the tangent of the copper roller to form scale-like strips. After grinding to a particle diameter of less than 70 microns, a master alloy is obtained. The master alloy is heat treated in a hydrogen atmosphere, the heat treatment temperature is 700° C., and the constant temperature time is 2 hours. The heat-treated master alloy was slowly added into a three-neck flask filled with 1000 g of 20% sodium hydroxide aqueous solution, an...
Embodiment 3
[0025] This example illustrates the preparation of a catalyst useful in the present invention.
[0026] Add 48 grams of nickel, 48 grams of aluminum, 2.5 grams of iron, and 1.5 grams of molybdenum into the quartz tube, heat it in a high-frequency furnace to above 1300 ° C to melt, make it alloyed, and then use inert gas to remove the alloy liquid from The nozzle under the quartz tube is sprayed onto a copper roller with a rotating speed of 800 rpm. Cooling water is passed through the copper roller. After rapid cooling, the alloy liquid is thrown out along the tangent of the copper roller to form scale-like strips. After grinding to a particle diameter of less than 70 microns, a master alloy is obtained. The master alloy is heat treated in a hydrogen atmosphere, the heat treatment temperature is 700° C., and the constant temperature time is 2 hours. The heat-treated master alloy was slowly added into a three-neck flask filled with 1000 g of 20% sodium hydroxide aqueous solutio...
PUM
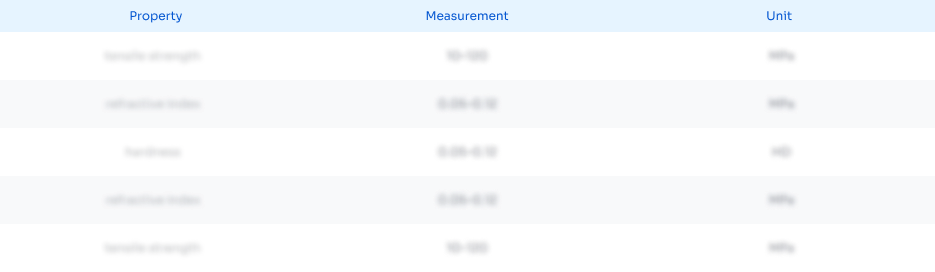
Abstract
Description
Claims
Application Information

- R&D Engineer
- R&D Manager
- IP Professional
- Industry Leading Data Capabilities
- Powerful AI technology
- Patent DNA Extraction
Browse by: Latest US Patents, China's latest patents, Technical Efficacy Thesaurus, Application Domain, Technology Topic, Popular Technical Reports.
© 2024 PatSnap. All rights reserved.Legal|Privacy policy|Modern Slavery Act Transparency Statement|Sitemap|About US| Contact US: help@patsnap.com