Skull pot for melting or refining inorganic substances
A slag shell smelting and smelting furnace technology, applied in glass melting devices, furnaces, boilers, etc., can solve problems such as copper corrosion, melt dyeing, and insufficiency, and achieve the effects of increased service life, high surface temperature, and increased output
- Summary
- Abstract
- Description
- Claims
- Application Information
AI Technical Summary
Problems solved by technology
Method used
Image
Examples
Embodiment Construction
[0039] As shown, the melting furnace in Fig. 1 is basically mushroom-shaped. It includes a cylindrical furnace wall. It consists of vertical metal tubes arranged in a circle. The vertical metal tube is bent by 90° at its upper end, which overall forms a flange collar 2 .
[0040] The bottom 3 of the smelting furnace is made of brick-like refractory materials. Optionally, the base can also be made of cooled metal tubes or rings. This is particularly advantageous at very high melting temperatures. It can be seen that it has an outlet 3.1 for releasing the finished glass melt.
[0041] An upper furnace wall 4 is mounted on the outer edge of the collar 2 . It is formed as a cylindrical ring of ceramic refractory material. The top cover 5 is likewise made of refractory material. The upper furnace 6 is surrounded by the upper furnace wall 4 , the top cover 5 and the molten liquid surface 7 .
[0042] A burner nozzle 8 extends into the upper furnace 6 .
[0043] An induction...
PUM
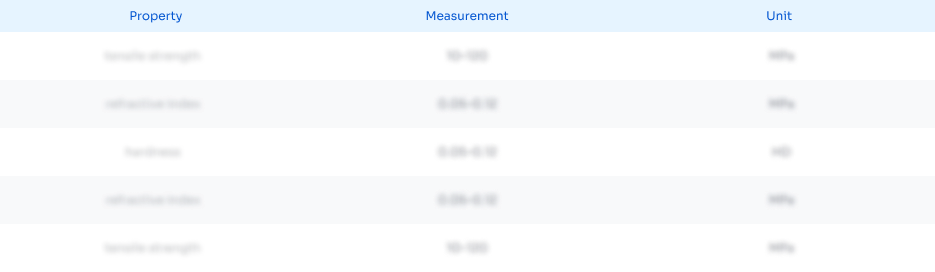
Abstract
Description
Claims
Application Information

- R&D
- Intellectual Property
- Life Sciences
- Materials
- Tech Scout
- Unparalleled Data Quality
- Higher Quality Content
- 60% Fewer Hallucinations
Browse by: Latest US Patents, China's latest patents, Technical Efficacy Thesaurus, Application Domain, Technology Topic, Popular Technical Reports.
© 2025 PatSnap. All rights reserved.Legal|Privacy policy|Modern Slavery Act Transparency Statement|Sitemap|About US| Contact US: help@patsnap.com