Method for manufacturing double-side flexible printed circuit board
一种制造方法、柔性印刷的技术,应用在印刷电路制造、印刷电路、印刷电路等方向,能够解决耐热性不理想、易收缩、贴合部位精度要求很高等问题
- Summary
- Abstract
- Description
- Claims
- Application Information
AI Technical Summary
Problems solved by technology
Method used
Image
Examples
Embodiment 1
[0073] The polyamic acid varnish obtained in the reference example was coated on the lower layer copper foil with a thickness of 12 μm, and the solvent was evaporated and removed in a continuous furnace at 80 to 170° C. to form a polyamic acid layer as a polyimide precursor layer.
[0074] Next, overlap the upper layer copper foil with a thickness of 12 μm on the polyamic acid layer, and use a 140°C vacuum hot press (surface pressure 70Kg / cm 2 ) for thermocompression bonding.
[0075] Next, after covering the surface of the lower layer copper foil with a protective film, a protective layer for the conductor circuit pattern is formed on the upper layer copper foil, and the upper layer copper foil is etched with an etching solution such as copper chloride aqueous solution to form an upper layer circuit layer. Subsequently, the protective layer and the protective film of the conductive circuit pattern are peeled off.
[0076] Next, put the laminate formed by the lower copper foi...
Embodiment 2
[0089] The polyamic acid varnish obtained in the reference example was coated on a 12 μm thick lower layer copper foil, and the solvent was evaporated in a continuous furnace at 80 to 170° C. to form a polyamic acid layer as a polyimide precursor layer.
[0090] Next, an upper wiring layer is formed on the polyamic acid layer by using a semi-additive method. That is, after the protective film is pasted on the surface of the lower copper foil, a 200 Å thick Ni layer is deposited on the polyamic acid layer by sputtering, and a 1000 Å thick Cu layer is deposited on this layer. A protective layer of conductive circuit patterns is formed on the film. Then use the electrolytic plating method to deposit an electrolytic copper plating layer with a thickness of 18 μm, and then peel off the protective layer of the conductive circuit pattern. The entire surface is subjected to soft etching with a mixed solution of hydrogen peroxide and sulfuric acid, whereby the upper wiring layer 23 is...
Embodiment 3
[0103] The polyamic acid varnish obtained in the reference example was coated on a 12 μm thick lower layer copper foil, and the solvent was evaporated in a continuous furnace at 80 to 170° C. as a polyimide precursor layer to form a polyamic acid layer.
[0104] Next, superimpose a 12 μm thick upper layer copper foil on the polyamic acid layer, and use a 200°C extrusion roll (surface pressure 60kg / cm 2 ) for hot pressing.
[0105] For the obtained laminated body consisting of lower layer copper foil / polyamic acid layer / upper layer copper foil, through-holes for through-holes are processed with an NC drill, and a copper layer is formed on the inner wall of the through-holes by a conventional method to obtain through-holes. , to ensure conduction between the upper copper foil and the lower copper foil.
[0106] Next, after covering the surface of the lower layer copper foil with a protective film, a protective layer of a conductor circuit pattern is formed on the upper layer co...
PUM
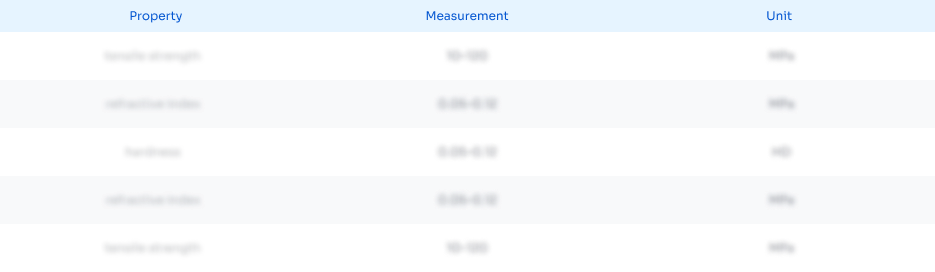
Abstract
Description
Claims
Application Information

- R&D Engineer
- R&D Manager
- IP Professional
- Industry Leading Data Capabilities
- Powerful AI technology
- Patent DNA Extraction
Browse by: Latest US Patents, China's latest patents, Technical Efficacy Thesaurus, Application Domain, Technology Topic, Popular Technical Reports.
© 2024 PatSnap. All rights reserved.Legal|Privacy policy|Modern Slavery Act Transparency Statement|Sitemap|About US| Contact US: help@patsnap.com