Method for preparing high-purity silicon by recovering diamond wire cutting silicon powder through electric field coupling directional solidification technology
A diamond wire cutting and directional solidification technology, applied in chemical instruments and methods, single crystal growth, single crystal growth and other directions, can solve the problems of low yield and insufficient purity, and achieve improved yield, improved purity, and guaranteed Effects of impurities and temperature uniformity
- Summary
- Abstract
- Description
- Claims
- Application Information
AI Technical Summary
Problems solved by technology
Method used
Image
Examples
Embodiment 1
[0025] Take 2005.5g of solid waste from diamond wire cutting silicon powder, grind it into a waste powder with a particle size of 20um; mix hydrofluoric acid, water and ethanol according to HF:H 2 O:C 2 H 5 The ratio of OH=1:3:1 is configured as a pickling solution, and the waste powder is pickled with the pickling solution under the action of a magnetic stirrer, and the mass ratio of the waste powder to the pickling solution is is 5:1, the acid washing reaction temperature is 40° C., and the acid washing time is 150 min; the stirring rate of the magnetic stirrer is 1400 r / min. The waste powder mixed solution obtained after the above-mentioned pickling treatment is subjected to solid-liquid separation by centrifugal mode, continuously rinsed with deionized water and centrifuged for 6 times until the pH value of the washing solution is neutral to obtain preliminarily purified silicon powder; The dried silicon powder is dried in a vacuum drying oven. The drying oven is set to ...
Embodiment 2
[0027]Take 2601.8g of solid waste from diamond wire cutting silicon powder, and grind it into a waste powder with a particle size of 10um; hydrofluoric acid, water and ethanol are mixed according to HF:H 2 O:C 2 H 5 The ratio of OH=1:3:1 is configured as a pickling solution, and the waste powder is pickled with the pickling solution under the action of a magnetic stirrer, and the mass ratio of the waste powder to the pickling solution is is 4:1, the acid washing reaction temperature is 50° C., and the acid washing time is 140 min; the stirring rate of the magnetic stirrer is 1100 r / min. The waste powder mixed solution obtained after the above-mentioned pickling treatment is subjected to solid-liquid separation by centrifugation, continuously rinsed with deionized water and centrifuged for 4 times until the pH value of the washing solution is neutral to obtain preliminarily purified silicon powder; The dried silicon powder is dried in a vacuum drying oven. The drying oven is ...
Embodiment 3
[0029] The electric field coupled directional solidification equipment described in the present invention is as attached figure 1 As shown, it includes a furnace shell 3, the top of the furnace shell 3 is provided with a flange 2, the flange 2 and the bottom center of the furnace shell 3 are oppositely provided with two conductive molybdenum wires 1, the conductive The molybdenum wire 1 is connected with the applied electric field 13; the bottom of the furnace shell 3 is provided with a crucible propelling support 10, the upper part of the crucible propelling support 10 is fixedly installed with a crucible base 9, and a crucible sleeve is arranged on the crucible base 9 Tube 8, a graphite crucible 5 is installed inside the crucible sleeve 8, a thermal insulation layer 7 is arranged between the graphite crucible 5 and the crucible sleeve 8, and an insulating sleeve 4 is installed inside the graphite crucible 5 ; The upper and lower parts of the furnace shell 3 are respectively ...
PUM
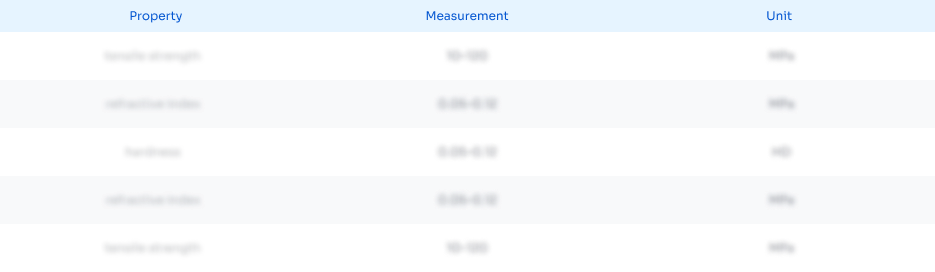
Abstract
Description
Claims
Application Information

- R&D
- Intellectual Property
- Life Sciences
- Materials
- Tech Scout
- Unparalleled Data Quality
- Higher Quality Content
- 60% Fewer Hallucinations
Browse by: Latest US Patents, China's latest patents, Technical Efficacy Thesaurus, Application Domain, Technology Topic, Popular Technical Reports.
© 2025 PatSnap. All rights reserved.Legal|Privacy policy|Modern Slavery Act Transparency Statement|Sitemap|About US| Contact US: help@patsnap.com