Composite grinding medium for grinding machine and preparation method of composite grinding medium
A grinding medium and grinding machine technology, applied in chemical instruments and methods, other chemical processes, cement production, etc., can solve the problems of poor dispersibility of raw material powder, high grinding cost, and poor hardness of ceramic grinding bodies.
- Summary
- Abstract
- Description
- Claims
- Application Information
AI Technical Summary
Problems solved by technology
Method used
Image
Examples
Embodiment 1
[0046] The present embodiment is a preparation method of modified silicon carbide, comprising the following steps:
[0047] S1: Add 10g of silicon carbide powder, 75mL of anhydrous ethanol and distilled water to a mixed solvent with a volume ratio of 1:5 and 0.15g of ethyl orthosilicate into a three-necked flask equipped with a stirrer and a thermometer, and then add Ammonia water with a mass fraction of 15% was used to adjust the pH of the mixed solvent to 9, and then the reaction was stirred for 3 hours at a temperature of 20 °C and a stirring rate of 300 r / min. After the reaction, the reaction product was washed twice with distilled water, and then placed in a vacuum. In a drying oven, drying to constant weight at a temperature of 70 °C to obtain pretreated silicon carbide;
[0048] S2: Add 10g of pretreated silicon carbide to 75mL of mixed solvent for ultrasonic dispersion for 30min, then add it to a three-necked flask equipped with a stirrer and a thermometer, then add 0....
Embodiment 2
[0050] The present embodiment is a preparation method of modified silicon carbide, comprising the following steps:
[0051] S1: Add 10g of silicon carbide powder, 100mL of anhydrous ethanol and distilled water according to the volume ratio of 1:5 mixed solvent and 0.35g of ethyl orthosilicate into a three-necked flask equipped with a stirrer and a thermometer, and then add Ammonia water with a mass fraction of 20% was used to adjust the pH of the mixed solvent to 10, and then the reaction was stirred for 4 hours at a temperature of 30 °C and a stirring rate of 400 r / min. After the reaction, the reaction product was washed three times with distilled water, and then placed in a vacuum In a drying oven, drying to constant weight at a temperature of 80 °C to obtain pretreated silicon carbide;
[0052] S2: Add 10g of pretreated silicon carbide to 100mL of mixed solvent for ultrasonic dispersion for 50min, then add it to a three-necked flask equipped with a stirrer and a thermometer...
Embodiment 3
[0054] The present embodiment is a preparation method of a ball milling accelerator, comprising the following steps:
[0055] S11: Add 0.1mol 4-nitroacetophenone and 30mL absolute ethanol into a three-necked flask equipped with a stirrer, a thermometer, a constant pressure dropping funnel and a reflux condenser, then at a temperature of 20°C and a stirring rate of 200r 13.5 mL of thionyl chloride was added dropwise with stirring at the condition of At room temperature, 120 mL of saturated ammonium chloride solution was added to continue stirring for 10 min, followed by vacuum filtration, the filter cake was placed in a vacuum drying oven, and dried to a constant weight at a temperature of 50 °C to obtain Intermediate A;
[0056] S12: add 10g of Intermediate A, 0.6g of 10% palladium-carbon and 100mL of absolute ethanol to a three-necked flask equipped with a stirrer, a thermometer, a constant-pressure dropping funnel and a reflux condenser, then at a temperature of 80°C, the st...
PUM
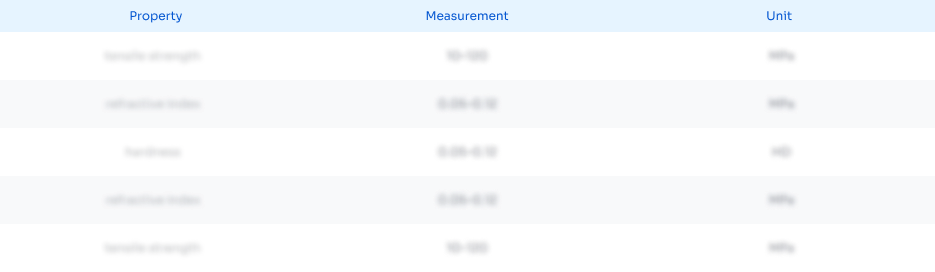
Abstract
Description
Claims
Application Information

- R&D
- Intellectual Property
- Life Sciences
- Materials
- Tech Scout
- Unparalleled Data Quality
- Higher Quality Content
- 60% Fewer Hallucinations
Browse by: Latest US Patents, China's latest patents, Technical Efficacy Thesaurus, Application Domain, Technology Topic, Popular Technical Reports.
© 2025 PatSnap. All rights reserved.Legal|Privacy policy|Modern Slavery Act Transparency Statement|Sitemap|About US| Contact US: help@patsnap.com