High-temperature-resistant synchronous motor magnetic steel and preparation method thereof
A technology for synchronous motors and high temperature resistance, which is applied in the manufacture of inductors/transformers/magnets, circuits, magnetic objects, etc., and can solve problems such as poor high temperature resistance, large temperature coefficient, and low Curie temperature of sintered NdFeB magnets , to achieve the effect of improving magnetic properties, high mechanical strength, improving grain size and grain morphology
- Summary
- Abstract
- Description
- Claims
- Application Information
AI Technical Summary
Problems solved by technology
Method used
Image
Examples
Embodiment 1-4
[0031] A high temperature resistant synchronous motor magnetic steel is prepared according to the following method with reference to the ratio in Table 1:
[0032] S1. Put the raw materials of the alloy main body into a vacuum reactor, smelt at 1650 ° C, cast into 0.5mm thick slabs after smelting, and crush the slabs into coarse powder by hydrogen breaking reaction in a hydrogen breaking furnace, Then add gasoline accounting for 0.03% of the total mass of the coarse powder as a lubricant to carry out jet milling, and jet milling until the median particle size of the main alloy powder is 4 μm;
[0033] S2. Add silicon nitride powder accounting for 0.3% of the total mass of the alloy body powder to the alloy body powder, mix evenly, then add gasoline accounting for 0.02% of the total mass of the alloy body powder as a lubricant, and add 0.02% of the total weight of the alloy body powder. The phosphite is used as an antioxidant, and the mixture is uniformly mixed. Under the prote...
Embodiment 5
[0038] A high temperature resistant synchronous motor magnetic steel, the proportion of each component of the alloy body is prepared by the following method with reference to Example 3:
[0039] S1. Put the raw materials of the alloy main body into a vacuum reactor, smelt at 1800 ° C, cast into 0.75mm thick slabs after smelting, and crush the slabs into coarse powder by hydrogen breaking reaction in a hydrogen breaking furnace, Then add gasoline accounting for 0.05% of the total mass of the coarse powder as a lubricant to carry out jet milling, and jet milling until the median particle size of the main alloy powder is 5 μm;
[0040] S2. Add silicon nitride powder accounting for 0.3% of the total mass of the alloy body powder to the alloy body powder, mix evenly, then add gasoline accounting for 0.04% of the total mass of the alloy body powder as a lubricant, and add 0.05% of the total weight of the alloy body powder. Phosphite is used as antioxidant, mixed evenly, under the pr...
Embodiment 6
[0043] A high temperature resistant synchronous motor magnetic steel, the proportion of each component of the alloy body is prepared by the following method with reference to Example 3:
[0044] S1. Put the raw materials of the alloy main body into a vacuum reactor, smelt at 1700 ° C, cast into a 0.75mm thick slab after smelting, and crush the slab into coarse powder by hydrogen breaking reaction in a hydrogen breaking furnace, Then add gasoline accounting for 0.03% of the total mass of the coarse powder as a lubricant to carry out jet milling, and jet milling until the median particle size of the main alloy powder is 5 μm;
[0045] S2. Add silicon nitride powder accounting for 0.3% of the total mass of the main alloy powder to the main alloy powder, mix evenly, then add gasoline accounting for 0.03% of the total mass of the main alloy powder as a lubricant, and add 0.04% of the total mass of the main alloy powder. The phosphite is used as an antioxidant, and the mixture is un...
PUM
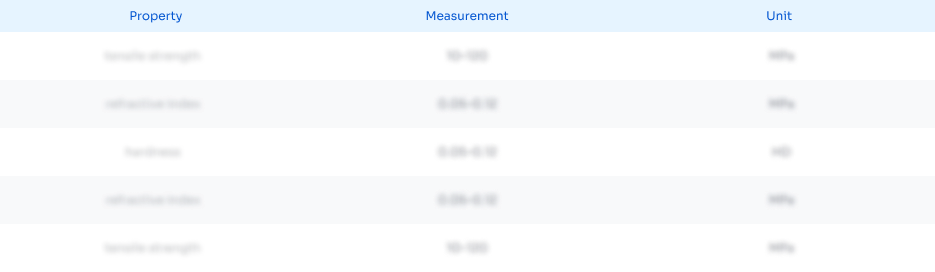
Abstract
Description
Claims
Application Information

- R&D
- Intellectual Property
- Life Sciences
- Materials
- Tech Scout
- Unparalleled Data Quality
- Higher Quality Content
- 60% Fewer Hallucinations
Browse by: Latest US Patents, China's latest patents, Technical Efficacy Thesaurus, Application Domain, Technology Topic, Popular Technical Reports.
© 2025 PatSnap. All rights reserved.Legal|Privacy policy|Modern Slavery Act Transparency Statement|Sitemap|About US| Contact US: help@patsnap.com