Preparation method of vanadium sodium fluophosphate cathode material of hybrid ion battery
A technology of sodium vanadium fluorophosphate and positive electrode materials, applied in battery electrodes, circuits, electrical components, etc., can solve problems such as easy sintering of lithium ions, unsuitable for high-rate current charging and discharging, production and application restrictions, and achieve large-scale production. High stability, improved electrochemical performance, easy to control and realize the effect
- Summary
- Abstract
- Description
- Claims
- Application Information
AI Technical Summary
Problems solved by technology
Method used
Image
Examples
Embodiment 1
[0028] Firstly, accurately weigh 2.5g of raw materials and 0.125g of conductive agent acetylene black, the acetylene black as conductive agent is 5% of the total weight of raw materials, put them in a mortar and grind them for 2.5h to obtain a uniformly mixed precursor . The raw material part includes 0.567g NaF, 0.802g V 2 o 5 , 1.025g NH 4 h 2 PO 4 and 0.106g reducing agent acetylene black (V:P:F molar ratio is about 2:2:3). The well-ground precursor powder was placed in a tube furnace, and the temperature was gradually raised to 350°C at a rate of 3°C / min under an argon protective atmosphere, and kept at this temperature for 8 hours, and a solid mixture was obtained after natural cooling. After the solid powder is completely transferred to the mortar and fully ground again, the set temperature is reached at a heating rate of 3°C / min. Carry out calcination in the range of 550-750°C, keep warm in argon atmosphere for 8 hours, and cool naturally to obtain sodium vanadium...
Embodiment 2
[0031] Accurately weigh 2.5g of raw materials and 0.125g of conductive agent acetylene black. The acetylene black used as conductive agent is 5% of the total weight of the raw materials. They are placed in a mortar and ground for 2.5 hours to obtain a uniformly mixed precursor. The raw material part includes 0.567g NaF, 0.802g V 2 o 5 , 1.128g NH 4 h 2 PO 4 and 0.106g reducing agent acetylene black (V:P:F molar ratio is about 2:2.2:3). The well-ground precursor powder was placed in a tube furnace, and the temperature was gradually raised to 350°C at a rate of 3°C / min under an argon protective atmosphere, and kept at this temperature for 8 hours, and a solid mixture was obtained after natural cooling. Completely transfer the solid powder to a mortar and fully grind it again, then calcinate at 550-750°C with a heating rate of 3°C / min, keep it in an argon atmosphere for 8 hours, and cool naturally with the furnace to obtain sodium vanadium phosphate. Other steps are the same...
Embodiment 3
[0033] Accurately weigh 2.5g of raw materials and 0.075g of conductive agent acetylene black. The acetylene black used as conductive agent is 3% of the total weight of raw materials. They are placed in a mortar and thoroughly ground for 2.5 hours to obtain a uniformly mixed precursor. The raw material part includes 0.567g NaF, 0.802g V 2 o 5 , 1.025g NH 4 h 2 PO 4 and 0.106g reducing agent acetylene black (V:P:F molar ratio is about 2:2:3). The well-ground precursor powder was placed in a tube furnace, and the temperature was gradually raised to 350°C at a rate of 3°C / min under an argon protective atmosphere, and kept at this temperature for 8 hours, and a solid mixture was obtained after natural cooling. Completely transfer the solid powder to a mortar and fully grind it again, then calcinate at 550-750°C with a heating rate of 3°C / min, keep it in an argon atmosphere for 8 hours, and cool naturally with the furnace to obtain sodium vanadium phosphate. Other steps are the...
PUM
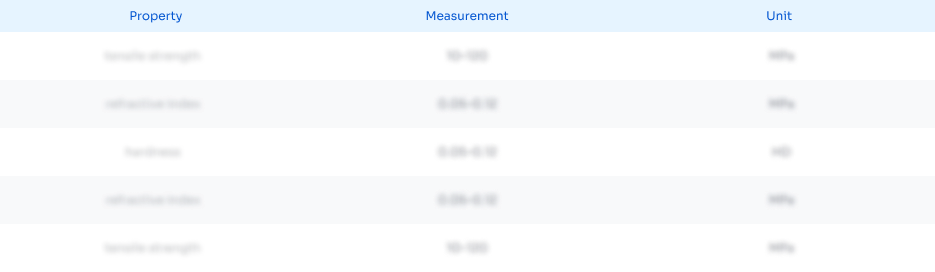
Abstract
Description
Claims
Application Information

- R&D
- Intellectual Property
- Life Sciences
- Materials
- Tech Scout
- Unparalleled Data Quality
- Higher Quality Content
- 60% Fewer Hallucinations
Browse by: Latest US Patents, China's latest patents, Technical Efficacy Thesaurus, Application Domain, Technology Topic, Popular Technical Reports.
© 2025 PatSnap. All rights reserved.Legal|Privacy policy|Modern Slavery Act Transparency Statement|Sitemap|About US| Contact US: help@patsnap.com