Mechanical catalysis method for preparing hydrogen and carbon through methane cracking
A methane gas and mechanical technology, which is applied in the field of mechanocatalysis for producing hydrogen and carbon by cracking methane, can solve the problems of high reaction energy consumption, deactivation of cracking catalyst, etc., and achieve low investment cost, prolong service life and reduce carbon deposition stacked effect
- Summary
- Abstract
- Description
- Claims
- Application Information
AI Technical Summary
Problems solved by technology
Method used
Examples
Embodiment 1
[0029] The pretreated metal nickel balls (diameter 1cm) were immersed in chloroplatinic acid (0.1M) solution for 1h ultrasonic treatment according to the ratio of 500g: 200mL solution, then the nickel balls were taken out and dried in a 90 ℃ oven for 2h, and finally The platinum-nickel alloy catalyst was synthesized by calcining nickel balls in air at 600℃ for 6h and calcining them in hydrogen at 800℃ for 6h.
[0030] Fill 300g Pt / Ni metal balls in a 2L mechanical reactor, feed 100mL / min methane gas, and react for 100h under the conditions of 400°C and 200Hz vibration frequency, the reactor pressure is 0.15MPa, and the mechanical reactor is above and below the mechanical reactor. The vibration method drives the metal alloy catalyst to generate mechanical force, the methane conversion rate is 20%, and the hydrogen selectivity is >99%.
Embodiment 2
[0032] The pretreated nickel-iron alloy balls (diameter 2cm) were immersed in chloroiridic acid (0.1M) and chloroplatinic acid (0.1M) solution for ultrasonic treatment for 1 h according to the ratio of 500g: 300mL solution, and then the nickel-iron balls were taken out and washed. After drying in an oven at 90 °C for 6 h, the nickel-iron balls were finally calcined at 650 °C in air for 6 h and calcined at 900 °C in hydrogen for 4 h to synthesize platinum-nickel alloy catalysts.
[0033] Fill 500g IrPt / NiFe metal balls in a 1.5L mechanical reactor, pass 50mL / min methane gas, and react for 100h under the conditions of 450℃ and 500Hz vibration frequency, the reactor pressure is 0.1MPa, and the mechanical reactor is The method of left and right vibration drives the metal alloy catalyst to generate mechanical force, the methane conversion rate is 40%, and the hydrogen selectivity is >99%.
Embodiment 3
[0035] The pretreated copper-iron alloy balls (diameter 3cm) were immersed in palladium nitrate (0.1M) and nickel acetate (0.1M) solution for 2h ultrasonic treatment according to the ratio of 500g: 300mL solution, and then the copper-iron balls were taken out and placed at 90 ℃. After drying in an oven at ℃ for 6 hours, the copper-iron balls were finally calcined at 700 ℃ in air for 5 h and calcined at 700 ℃ in hydrogen for 6 h to synthesize PdNi / CuFe alloy catalysts.
[0036] Fill 500g PdNi / CuFe metal balls in a 1L mechanical reactor, pass 80mL / min methane gas, and react for 100h under the conditions of 600℃ and 1000Hz vibration frequency, the reactor pressure is 0.1MPa, and the mechanical reactor is at the center The rotating shaft squeezes the grinding medium to drive the metal alloy catalyst to generate mechanical force, the methane conversion rate is 40%, and the hydrogen selectivity is >99%.
PUM
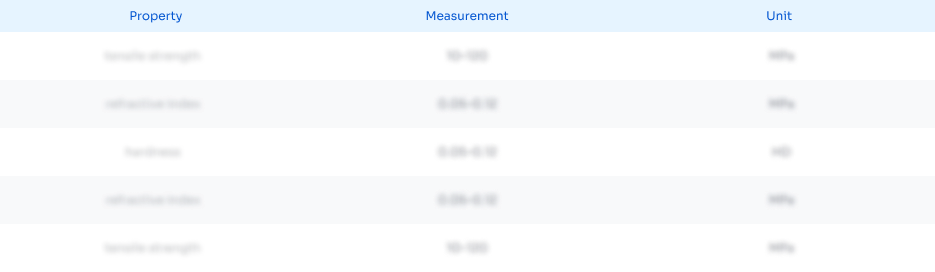
Abstract
Description
Claims
Application Information

- R&D
- Intellectual Property
- Life Sciences
- Materials
- Tech Scout
- Unparalleled Data Quality
- Higher Quality Content
- 60% Fewer Hallucinations
Browse by: Latest US Patents, China's latest patents, Technical Efficacy Thesaurus, Application Domain, Technology Topic, Popular Technical Reports.
© 2025 PatSnap. All rights reserved.Legal|Privacy policy|Modern Slavery Act Transparency Statement|Sitemap|About US| Contact US: help@patsnap.com