Method for treating cyanidation tailings by adopting anaerobic roasting-persulfate leaching combined technology
A technology of cyanide tailings and persulfate, applied in the field of metallurgy and beneficiation, can solve the problems of complex iron recovery process, low product value, neglect of recovery, etc., and achieve the effect of easy oxidation and dissolution and unstable chemical properties.
- Summary
- Abstract
- Description
- Claims
- Application Information
AI Technical Summary
Problems solved by technology
Method used
Image
Examples
Embodiment 1
[0055] The present embodiment adopts anaerobic roasting-persulfate leaching combined technology to process the method for cyanide tailings, comprising the following steps:
[0056] (1) Dry the cyanide tailings raw material at a drying temperature of 60° C. to ensure that the moisture content of the raw material is less than or equal to 3%.
[0057] (2) Take 15g of the dried sample, put it in a porcelain boat and place it in a quartz tube, put the quartz tube in a tube furnace, pass nitrogen for 20 minutes to discharge the air, and close the air inlet. Turn on the tube furnace for roasting, heat up to 600 °C, keep it for 1 hour, and then cool down to room temperature with the furnace. After cooling, collect the sulfur product on the quartz tube and the product collection bottle. Weigh the condensate and calcine respectively, and analyze the condensation. According to the S and Fe grades of calcine and calcine, the mass loss rate and S recovery rate during the roasting process a...
Embodiment 2
[0072] The present embodiment adopts anaerobic roasting-persulfate leaching combined technology to process the method for cyanide tailings, comprising the following steps:
[0073] (1) Dry the cyanide tailings raw material at a drying temperature of 62° C. to ensure that the moisture content of the raw material is less than or equal to 3%.
[0074] (2) Take 15g of the dried sample, put it in a porcelain boat and place it in a quartz tube, put the quartz tube in a tube furnace, pass nitrogen for 20 minutes to discharge the air, and close the air inlet. Turn on the tube furnace for roasting, heat up to 600°C, keep the temperature for 6 hours, and then cool down to room temperature with the furnace. After cooling, collect the sulfur product on the quartz tube and the product collection bottle. Weigh the condensate and calcine respectively, and analyze the condensation. The S and Fe grades of the calcined material and calcine were calculated, and the mass loss rate and S recovery ...
Embodiment 3
[0078] The present embodiment adopts anaerobic roasting-persulfate leaching combined technology to process the method for cyanide tailings, comprising the following steps:
[0079] (1) Dry the cyanide tailings raw material at a drying temperature of 58° C. to ensure that the moisture content of the raw material is less than or equal to 3%.
[0080] (2) Take 15g of the dried sample, put it in a porcelain boat and place it in a quartz tube, put the quartz tube in a tube furnace, pass nitrogen for 20 minutes to discharge the air, and close the air inlet. Turn on the tube furnace for roasting, heat up to 700 °C, keep it for 1 hour, and then cool down to room temperature with the furnace. After cooling, collect the sulfur product on the quartz tube and the product collection bottle. Weigh the condensate and calcine respectively, and analyze the condensation. The S and Fe grades of the calcined material and calcine were calculated, and the mass loss rate and S recovery rate during t...
PUM
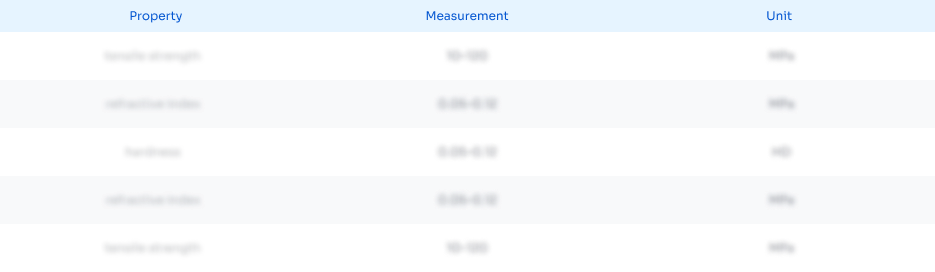
Abstract
Description
Claims
Application Information

- Generate Ideas
- Intellectual Property
- Life Sciences
- Materials
- Tech Scout
- Unparalleled Data Quality
- Higher Quality Content
- 60% Fewer Hallucinations
Browse by: Latest US Patents, China's latest patents, Technical Efficacy Thesaurus, Application Domain, Technology Topic, Popular Technical Reports.
© 2025 PatSnap. All rights reserved.Legal|Privacy policy|Modern Slavery Act Transparency Statement|Sitemap|About US| Contact US: help@patsnap.com