Preparation method of high-strength and high-toughness stainless steel powder for selective laser melting additive manufacturing
A technology of selective laser melting and additive manufacturing, applied in additive manufacturing, processing manufacturing, additive processing, etc., can solve the problems of poor atomization effect, short service life, residue, etc., and achieve environmental protection in the preparation process, improved fluidity, Good atomization effect
- Summary
- Abstract
- Description
- Claims
- Application Information
AI Technical Summary
Problems solved by technology
Method used
Image
Examples
Embodiment 1
[0035] A method for preparing high-strength and high-toughness stainless steel powder for selective laser melting additive manufacturing, the steps of which are as follows:
[0036] S1: Select metal element materials that conform to the composition design for batching. The vacuum in the furnace is less than 500Pa. The raw materials are vacuum induction heated and melted. The melting temperature is 1300-1800°C. Soak, the charge is completely cleared until the liquid level is calm, keep for 2-10min, the molten metal is poured into the heat preservation crucible of the tundish, and flows into the supersonic gas atomization nozzle through the bottom guide tube of the heat preservation crucible;
[0037] S2: Inject high-pressure inert argon gas, accelerate through the Laval structure cavity, form a supersonic airflow, the gas pressure is 3Mpa-8Mpa, impact and break the metal liquid falling into the atomization area, and atomize it into fine metal droplets;
[0038] S3: The liquid d...
Embodiment 2
[0046] A method for preparing high-strength and high-toughness stainless steel powder for selective laser melting additive manufacturing, the steps of which are as follows:
[0047] S1: Select metal element materials that conform to the composition design for batching. The vacuum in the furnace is less than 500Pa. The raw materials are vacuum induction heated and melted. The melting temperature is 1300-1800°C. Soak, the charge is completely cleared until the liquid level is calm, keep for 2-10min, the molten metal is poured into the heat preservation crucible of the tundish, and flows into the supersonic gas atomization nozzle through the bottom guide tube of the heat preservation crucible;
[0048] S2: Inject high-pressure inert argon gas, accelerate through the Laval structure cavity, form a supersonic airflow, the gas pressure is 3Mpa-8Mpa, impact and break the metal liquid falling into the atomization area, and atomize it into fine metal droplets;
[0049] S3: The liquid d...
Embodiment 3
[0057] A method for preparing high-strength and high-toughness stainless steel powder for selective laser melting additive manufacturing, the steps of which are as follows:
[0058] S1: Select metal element materials that conform to the composition design for batching. The vacuum in the furnace is less than 500Pa. The raw materials are vacuum induction heated and melted. The melting temperature is 1300-1800°C. Soak, the charge is completely cleared until the liquid level is calm, keep for 2-10min, the molten metal is poured into the heat preservation crucible of the tundish, and flows into the supersonic gas atomization nozzle through the bottom guide tube of the heat preservation crucible;
[0059] S2: Inject high-pressure inert argon gas, accelerate through the Laval structure cavity, form a supersonic airflow, the gas pressure is 3Mpa-8Mpa, impact and break the metal liquid falling into the atomization area, and atomize it into fine metal droplets;
[0060] S3: The liquid d...
PUM
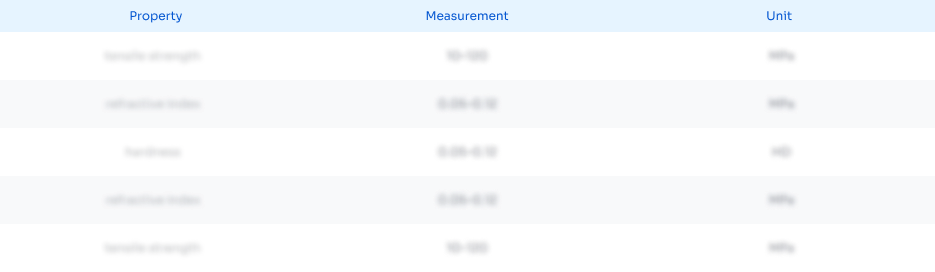
Abstract
Description
Claims
Application Information

- R&D Engineer
- R&D Manager
- IP Professional
- Industry Leading Data Capabilities
- Powerful AI technology
- Patent DNA Extraction
Browse by: Latest US Patents, China's latest patents, Technical Efficacy Thesaurus, Application Domain, Technology Topic, Popular Technical Reports.
© 2024 PatSnap. All rights reserved.Legal|Privacy policy|Modern Slavery Act Transparency Statement|Sitemap|About US| Contact US: help@patsnap.com