Composite hollow fiber braided tube filter membrane for fuel cells as well as preparation method and application of composite hollow fiber braided tube filter membrane
A fiber braided tube and fuel cell technology, which is applied to fuel cells, chemical instruments and methods, membranes, etc., can solve the problems of limiting the long-term stability of humidification membranes, unfavorable normal operation of fuel cells, and difficulty in water vapor escape. Achieve the effect of low material price, excellent moisturizing effect and maintaining stability
- Summary
- Abstract
- Description
- Claims
- Application Information
AI Technical Summary
Problems solved by technology
Method used
Image
Examples
Embodiment 1
[0039] S11, stirring and dissolving polyether polyurethane, dimethyl sulfoxide, and ammonium bicarbonate with a solid content of 22 wt% at 70° C. for 12 hours, and filtering and defoaming for 24 hours, to obtain a polyurethane-based high molecular polymer casting solution;
[0040] S12. Stir and dissolve polyethersulfone, dimethylsulfoxide, PEG1000, and sulfonated polyethersulfone with a solid content of 22wt% at 70°C for 12 hours, filter and defoam for 24 hours to obtain a polysulfone-based polymer Casting solution;
[0041] S13. Using a three-hole spinneret, the polyurethane-based polymer casting solution and the polysulfone-based polymer casting solution are sequentially placed outside the hollow fiber braided tube; at 1.0MPa, polyether polyurethane / The polyethersulfone double modifier and the hollow fiber braided tube are extruded from the spinneret, and after gelation in an external coagulation bath, continuous water washing, and rapid drying, the composite hollow fiber ...
Embodiment 2
[0044] S21. Stir and dissolve polyester polyurethane with a solid content of 16wt%, N,N-dimethylformamide, and azodicarbonamide at 60°C for 8 hours, and filter and defoam for 10 minutes to obtain a polyurethane polymer polymer film casting solution;
[0045] S22. Stir and dissolve polyarylethersulfone with a solid content of 16wt%, N,N-dimethylformamide, PEG2000, and polyethyleneimine at 60°C for 8 hours, and filter and defoam for 12 hours to obtain polysulfone Polymer-like casting solution;
[0046] S23. Using a three-hole spinneret, the polyurethane-based high-molecular polymer casting solution and the polysulfone-based high-molecular polymer casting solution are placed on the outside of the hollow fiber braided tube in sequence; Polyaryl polyether sulfone double modifier and hollow fiber braided tube are extruded from the spinneret, and after gelation in an external coagulation bath, continuous water washing, and rapid drying, the composite hollow fiber braided tube filter...
Embodiment 3
[0049] S31. Stir and dissolve polyether polyurethane with a solid content of 24wt%, N,N-dimethylacetamide, and azodicarbonamide at 90°C for 24 hours, and filter and defoam for 48 hours to obtain a polyurethane polymer polymer film casting solution;
[0050] S32. Stir and dissolve sulfonated polysulfone with a solid content of 24wt%, N,N-dimethylacetamide, PEG200, and titanium dioxide at 90°C for 24 hours, and filter and defoam for 48 hours to obtain polysulfone polymers film casting solution;
[0051] S33. Using a three-hole spinneret, the polyurethane-based high-molecular polymer casting solution and the polysulfone-based high-molecular polymer casting solution are placed on the outside of the hollow fiber braided tube in sequence; The sulfonated polysulfone double modifier and the hollow fiber braided tube are extruded from the spinneret, and after gelation in an external water coagulation bath, continuous water washing, and rapid drying, the composite hollow fiber braided ...
PUM
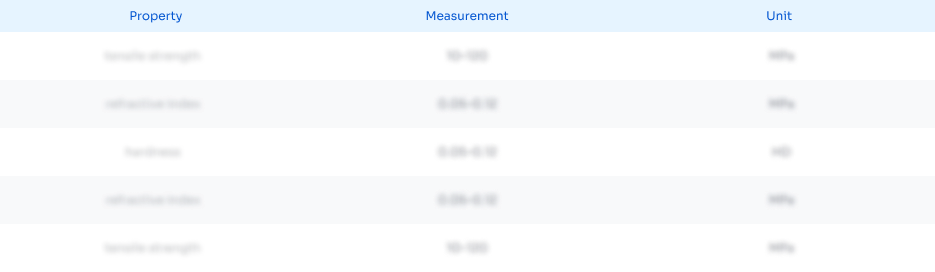
Abstract
Description
Claims
Application Information

- Generate Ideas
- Intellectual Property
- Life Sciences
- Materials
- Tech Scout
- Unparalleled Data Quality
- Higher Quality Content
- 60% Fewer Hallucinations
Browse by: Latest US Patents, China's latest patents, Technical Efficacy Thesaurus, Application Domain, Technology Topic, Popular Technical Reports.
© 2025 PatSnap. All rights reserved.Legal|Privacy policy|Modern Slavery Act Transparency Statement|Sitemap|About US| Contact US: help@patsnap.com