Method for preparing modified PBS copolyester by using camphor alcohol
A copolyester and modification technology, which is applied in the field of preparing modified PBS copolyester with camphor alcohol, can solve the problems of low elongation at break, low glass transition temperature, slow degradation speed, etc., and achieve good thermal stability , easy to operate, and reduce the effect of dependence
- Summary
- Abstract
- Description
- Claims
- Application Information
AI Technical Summary
Problems solved by technology
Method used
Image
Examples
Embodiment 1
[0022] Embodiment 1: the preparation of TCDM monomer
[0023] After camphoric acid (10 g) and 156 mL of anhydrous tetrahydrofuran were mixed and dissolved, lithium aluminum tetrahydrogen (5.85 g) was slowly added to the solution under ice-cooling, stirred at room temperature for 4 hours, and then heated to reflux at 70° C. for 0.5 h. Afterwards, water (125 mL) and hydrochloric acid solution (250 mL, 2M) were added successively, extracted with dichloromethane, washed with saturated sodium bicarbonate, and dried over anhydrous magnesium sulfate. Suction filtration and removal of the solvent under reduced pressure gave the crude product. The obtained product was recrystallized with a mixed solvent of dichloromethane and n-hexane to obtain 6 g of pure product with a yield of 72.1%.
Embodiment 2
[0024] Embodiment 2: prepare PTS polyester with TCDM
[0025] Add 4g (23.22mmol) TCDM and 3.08g (21.11mmol) dimethyl succinate to a 100mL airtight there-necked flask to obtain a mixed solution, the molar number of TCDM is 1.1 times that of dimethyl succinate, add catalyst titanic acid Tetrabutyl ester 0.63 mg, slowly inject nitrogen and continue to stir, heat to 130°C, react at this temperature for 4 hours, remove the nitrogen protection, change the vacuum to 0.03-0.06mbar, and continue polycondensation at 240-250°C reaction. After the reaction mixture was cooled to room temperature, 10 mL of chloroform was added to dissolve it, and then methanol was added for precipitation, and the precipitated solid was suction-filtered and fully dried to obtain a copolyester.
Embodiment 3
[0026] Embodiment 3: prepare random PBS copolyester by TCDM, butanediol, dimethyl succinate
[0027] Add 1g (5.80mmol) TCDM, 4.71g (52.24mmol) 1,4-butanediol and 8.48g (58.05mmol) dimethyl succinate into a 100mL airtight three-necked flask to obtain a mixed solution, add catalyst tetrabutyl titanate Esters 0.63 mg, nitrogen was slowly introduced and continued to stir, heated to 130°C, reacted at this temperature for 4 hours, removed the nitrogen protection, changed to vacuum to 0.03-0.06mbar, and continued the polycondensation reaction at 240-250°C. After the reaction mixture was cooled to room temperature, 10 mL of chloroform was added to dissolve it, and then methanol was added for precipitation, and the precipitated solid was suction-filtered and fully dried to obtain a copolyester.
PUM
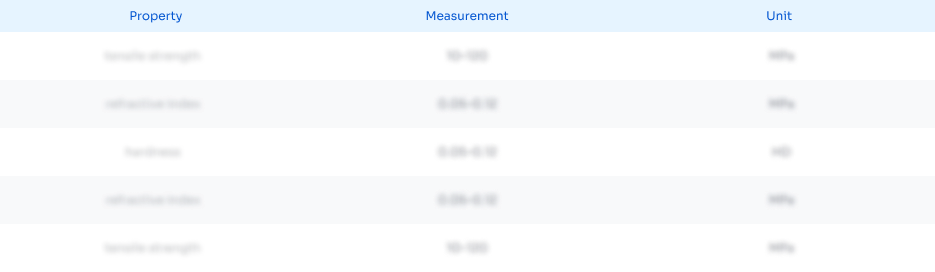
Abstract
Description
Claims
Application Information

- R&D
- Intellectual Property
- Life Sciences
- Materials
- Tech Scout
- Unparalleled Data Quality
- Higher Quality Content
- 60% Fewer Hallucinations
Browse by: Latest US Patents, China's latest patents, Technical Efficacy Thesaurus, Application Domain, Technology Topic, Popular Technical Reports.
© 2025 PatSnap. All rights reserved.Legal|Privacy policy|Modern Slavery Act Transparency Statement|Sitemap|About US| Contact US: help@patsnap.com