Preparation method of modified graphene oxide and method for preparing epoxy resin composite material by using modified graphene oxide
A composite material and epoxy resin technology, applied in chemical instruments and methods, carbon compounds, inorganic chemistry, etc., can solve the problems of high brittleness and poor impact toughness of epoxy resin, and achieve improved elongation at break and toughness , Improve the effect of nano-enhanced effect
- Summary
- Abstract
- Description
- Claims
- Application Information
AI Technical Summary
Problems solved by technology
Method used
Image
Examples
Embodiment 1
[0042] (1) Preparation of aminated graphene oxide
[0043] Weigh 30g of 3-aminopropyltriethoxysilane, 108g of ethanol and 12g of water into a 250ml three-necked flask and stir for 10-15min, then add 1.5g of graphene oxide and sonicate for 1-1.5h. It was reacted at 60° C. for 6 hours, and after cooling to room temperature, the slurry reaction mixture was centrifuged and washed with ethanol and distilled water to remove residual 3-aminopropyltriethoxysilane and achieve neutrality. Finally, freeze-dry and collect the resulting product. Infrared spectroscopy of the reactant graphene oxide, see figure 1 Middle a curve, 910cm -1 The absorption peak at is the epoxy group absorption peak, which can prove that the reactant used in the experiment is graphene oxide. The above-mentioned reaction product is carried out the spectroscopic test of infrared, see appendix figure 1 Middle b curve, 1027cm -1 The absorption peak at is the absorption peak of C-O-Si, indicating that the silane ...
Embodiment 2
[0056] (1) Preparation of aminated graphene oxide
[0057] Weigh 30g of 3-aminopropyltriethoxysilane, 108g of ethanol and 12g of water into a 250ml three-necked flask and stir for 10-15min, then add 1.5g of graphene oxide and sonicate for 1-1.5h. It was reacted at 60° C. for 6 hours, and after cooling to room temperature, the slurry reaction mixture was centrifuged and washed with ethanol and distilled water to remove residual 3-aminopropyltriethoxysilane and achieve neutrality. Finally, freeze-dried and collected to obtain aminated graphene oxide.
[0058] (2) Preparation of bromine-terminated graphene oxide
[0059] Weigh 1.5g of aminated graphene oxide and 100ml of toluene into a 250ml three-necked flask, add 0.3g of 4-dimethylaminopyridine, 0.5ml of triethylamine, ice bath for 30min, slowly add 4ml of 2- bromoisobutyryl bromide, then the reaction mixture was stirred at room temperature for 24h. After the reaction, wash with excess acetone / water solution (v / v, 1 / 1) and t...
Embodiment 3
[0069] (1) Preparation of aminated graphene oxide
[0070] Weigh 30g of 3-aminopropyltriethoxysilane, 108g of ethanol and 12g of water into a 250ml three-necked flask and stir for 10-15min, then add 1.5g of graphene oxide and sonicate for 1-1.5h. It was reacted at 60° C. for 6 hours, and after cooling to room temperature, the slurry reaction mixture was centrifuged and washed with ethanol and distilled water to remove residual 3-aminopropyltriethoxysilane and achieve neutrality. Finally, freeze-dried and collected to obtain aminated graphene oxide.
[0071] (2) Preparation of bromine-terminated graphene oxide
[0072] Weigh 1.5g of aminated graphene oxide and 100ml of toluene into a 250ml three-necked flask, add 0.3g of 4-dimethylaminopyridine, 0.5ml of triethylamine, ice bath for 30min, slowly add 4ml of 2- bromoisobutyryl bromide, then the reaction mixture was stirred at room temperature for 24h. After the reaction, wash with excess acetone / water solution (v / v, 1 / 1) and t...
PUM
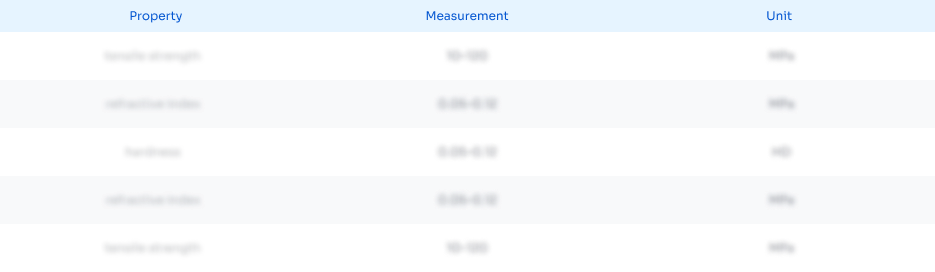
Abstract
Description
Claims
Application Information

- Generate Ideas
- Intellectual Property
- Life Sciences
- Materials
- Tech Scout
- Unparalleled Data Quality
- Higher Quality Content
- 60% Fewer Hallucinations
Browse by: Latest US Patents, China's latest patents, Technical Efficacy Thesaurus, Application Domain, Technology Topic, Popular Technical Reports.
© 2025 PatSnap. All rights reserved.Legal|Privacy policy|Modern Slavery Act Transparency Statement|Sitemap|About US| Contact US: help@patsnap.com