Producing method of PU divert film
A production method and film technology, applied in chemical instruments and methods, lamination auxiliary operations, lamination devices, etc., can solve the problems that imitation leather cannot be used for synthetic leather, hand feeling, appearance without real leather effect, etc.
- Summary
- Abstract
- Description
- Claims
- Application Information
AI Technical Summary
Problems solved by technology
Method used
Image
Examples
Embodiment 1
[0029] A. Impregnated water repellent formula:
[0030] 100 parts of pure water;
[0031] Water-repellent agent RF-5020 (30% solid content) 3 parts.
[0032] B. Wet slurry formula:
[0033] Polyether, polycarbon type polyurethane resin (model HX-3025A) 100 parts;
[0034] 50 parts of DMF solvent;
[0035] Solvent colorant JQ-512 3 parts;
[0036] Wood powder (model FD600 / 30) 5 parts.
[0037] C. Dry slurry process formula:
[0038] Top coat:
[0039] 100 parts of polycarbonate polyurethane resin;
[0040] Solvent (DMF60%, MEK40%) 10 parts;
[0041] 15 parts of colorant;
[0042] Leveling agent 1 part.
[0043] Primer:
[0044] 100 parts of polycarbonate polyurethane resin;
[0045] Solvent (DMF25%, MEK75%) 10 parts;
[0046] 10 parts of colorant;
[0047] Leveling agent 1 part.
Embodiment 2
[0049] A. Impregnated water repellent formula:
[0050] 100 parts of pure water;
[0051] Water-repellent agent RF-5020 (solid content 30%) 10 parts.
[0052] The prescription of B and C is with embodiment 1.
Embodiment 3
[0054] A. Impregnated water repellent formula:
[0055] 100 parts of pure water;
[0056] Water-repellent agent RF-5020 (30% solid content) 3 parts.
[0057] B. Wet slurry formula:
[0058] 30 parts of polyester polyurethane resin (model HX-7060AHV);
[0059] 70 parts of polyester polyurethane resin (model HX-7025BHV);
[0060] 50 copies of DMF;
[0061] 2 parts of solvent-based colorant RW500J;
[0062] Wood powder (model FD600 / 30) 5 parts.
[0063] C. Dry slurry process formula:
[0064] Top coat:
[0065] 100 parts of polyester polyurethane resin (HX-8030);
[0066] Solvent (DMF83%, MEK17%) 50 parts;
[0067] 10 parts of colorant;
[0068] Leveling agent 1 part.
[0069] Primer:
[0070] 100 parts of polyester polyurethane resin (HX-930);
[0071] Solvent (DMF30%, MEK70%) 40 parts;
[0072] 10 parts of colorant;
[0073] Leveling agent 1 part.
PUM
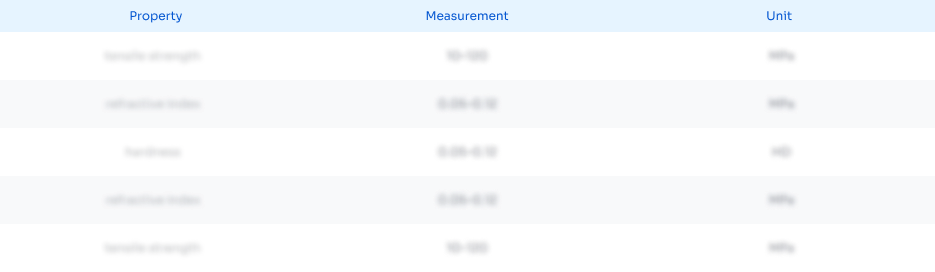
Abstract
Description
Claims
Application Information

- R&D
- Intellectual Property
- Life Sciences
- Materials
- Tech Scout
- Unparalleled Data Quality
- Higher Quality Content
- 60% Fewer Hallucinations
Browse by: Latest US Patents, China's latest patents, Technical Efficacy Thesaurus, Application Domain, Technology Topic, Popular Technical Reports.
© 2025 PatSnap. All rights reserved.Legal|Privacy policy|Modern Slavery Act Transparency Statement|Sitemap|About US| Contact US: help@patsnap.com