Preparation method of rough rolling high-speed steel working roll for full endless rolling of sheet billets
A technology of endless rolling and high-speed steel, which is applied in the field of materials, can solve problems such as the inability to meet the needs of rolling lines and serious cracks in the lower machine, achieve excellent thermal crack resistance and cold and heat fatigue performance, prolong the machine cycle, Effect of increasing stability against tempering
- Summary
- Abstract
- Description
- Claims
- Application Information
AI Technical Summary
Problems solved by technology
Method used
Image
Examples
preparation example Construction
[0026] A method for preparing rough rolling high-speed steel work rolls for full endless rolling of thin slabs, comprising the following steps:
[0027] Step A, using steel scrap, ferronickel, ferrovanadium, ferrochromium, ferromolybdenum, ferrotungsten, and electrode powder as raw materials, ferronickel can be replaced by nickel plate, ferrotungsten can be replaced by tungsten wire or tungsten alloy, ferromolybdenum can be replaced by alloy molybdenum , the above-mentioned materials can also be compounds of multi-element alloys, as long as the composition ratio meets the requirements of the alloy range. The outer layer molten iron and the core molten iron are smelted by a power frequency furnace; the chemical composition of the outer layer molten iron is: C: 0.6-1.8%, Si: 0.5-1.5%, Mn: 0.2-1.2%, P≤0.10%, S≤0.1 %, Cr: 4.0-10.0%, Ni: 0.5-3.0%, Mo: 2.0-7.0%, V: 0.5-4.0, W: 0.5-2.0, Nb≤1.0%, the balance is Fe; the core chemical composition range C: 2.3~4.0%, Si: 1.0~4.0%, Mn: 0....
Embodiment 1
[0034] Using scrap steel, ferronickel, ferrovanadium, ferrochromium, ferromolybdenum, ferrotungsten, and electrode powder as raw materials, it is smelted in an intermediate frequency furnace to reach the design composition range of high-speed steel: outer layer molten iron C: 0.6%, Si: 0.85%, Mn: 0.9%, P: 0.05%, S: 0.06%, Cr: 8.9%, Ni: 2.1%, Mo: 0.85%, V: 1.01%, W: 0.5%, the balance is Fe; core molten iron C: 3.01% , Si: 1.5%, Mn: 0.8%, P: 0.08%, S: 0.09%, Cr: 0.05%, Ni: 0.1%, Mo: 0.1%, W+V+Nb=0.06%, and the balance is Fe. The outer layer is smelted at a temperature of 1550°C. After the composition reaches the standard, it is heated to 1650°C and released from the furnace, blown with argon for 5 minutes, standing for 3 minutes, and cooled to 1553°C for centrifugal casting; the melting temperature of the core molten steel is 1406°C, heated to 1553°C and blown with argon for 6 minutes. Stand still for 3 minutes, the temperature drops to 1456 ℃ and start pouring, 150 hours after ...
Embodiment 2
[0036] Using scrap steel, ferronickel, ferrovanadium, ferrochrome, ferromolybdenum, ferrotungsten, and electrode powder as raw materials, it is smelted in an intermediate frequency furnace to reach the design composition range of high-speed steel: outer layer molten iron C: 0.8%, Si: 0.85%, Mn: 0.91%, P: 0.05%, S: 0.06%, Cr: 8.8%, Ni: 2.1%, Mo: 2.88%, V: 1.03%, W: 0.6%, the balance is Fe; core molten iron C: 2.95% , Si: 1.45%, Mn: 0.75%, P: 0.06%, S: 0.08%, Cr: 0.03%, Ni: 0.25%, Mo: 0.05%, W+V+Nb=0.03%, and the balance is Fe. The outer layer is smelted at a temperature of 1550°C. After the composition reaches the standard, the temperature is raised to 1650°C and then released from the furnace. Argon is blown for 4 minutes, left for 2 minutes, and the temperature is lowered to 1558°C for centrifugal casting. The melting temperature of the core molten steel is 1409°C. Stand still for 3 minutes, the temperature drops to 1453 ° C to start pouring, 180 hours after the pouring is co...
PUM
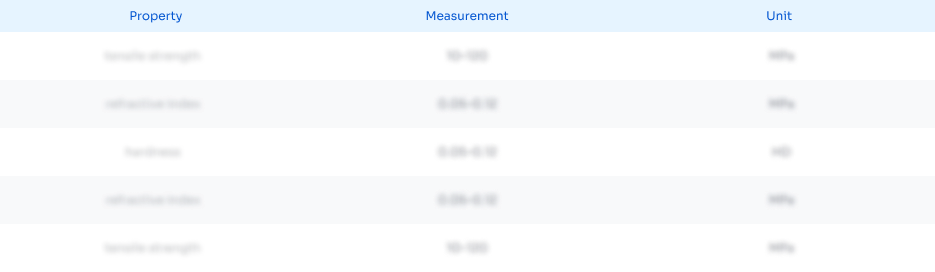
Abstract
Description
Claims
Application Information

- R&D
- Intellectual Property
- Life Sciences
- Materials
- Tech Scout
- Unparalleled Data Quality
- Higher Quality Content
- 60% Fewer Hallucinations
Browse by: Latest US Patents, China's latest patents, Technical Efficacy Thesaurus, Application Domain, Technology Topic, Popular Technical Reports.
© 2025 PatSnap. All rights reserved.Legal|Privacy policy|Modern Slavery Act Transparency Statement|Sitemap|About US| Contact US: help@patsnap.com