PBAT composite material and preparation method and application thereof
A technology of composite materials and raw materials, which is applied in the field of PBAT composite materials and its preparation, can solve problems such as limitations, poor compatibility, and poor mechanical properties of composite materials
- Summary
- Abstract
- Description
- Claims
- Application Information
AI Technical Summary
Problems solved by technology
Method used
Image
Examples
preparation example Construction
[0035] The preparation method of the PBAT composite material according to the present invention comprises the following steps: (1) mix the raw materials of the new plasticizer according to the proportion at 80° C., heat at a constant temperature for 1-4 hours and filter to obtain a transparent liquid, which is the new plasticizer (2) mix the antibacterial agent with the new plasticizer described in (1) according to the ratio, and then heat it at a constant temperature of 80°C for 30 minutes to obtain a mixed solvent; (3) bake the bio-based filler at 80°C for 8-12h , after removing the water therein, (2) the mixed solvent and the bio-based filler are mixed evenly and heated at a constant temperature of 70-90°C for 4-8h before use; (4) the PBAT is baked at 60-80°C for 8- 12h, according to the weight fraction, the PBAT, the bio-based filler, and the mixed solvent are added to the equipment and mixed evenly, and the composite material masterbatch is obtained by single-screw / twin-sc...
Embodiment 1
[0040] This example provides a preparation method of a new type of PBAT composite material: (1) mix choline chloride and glycerin at a ratio of 2:1 at 80°C, heat at a constant temperature for 2 hours and filter to obtain a transparent liquid. new plasticizer; (2) mix benzalkonium chloride with the new plasticizer described in (1) according to the ratio, and then heat at 80°C for 30 minutes to obtain a mixed solvent; (3) starch at 80°C After drying for 10 hours and removing the moisture, mix (2) the mixed solvent with it evenly and heat it at a constant temperature at 80°C for 6 hours before use; (4) bake PBAT at 80°C for 10 hours, add 100 parts of PBAT and 20 parts of starch , 12 parts of new plasticizer, 0.1 part of antibacterial agent, add in equipment and mix 30min, by single-screw granulation, make composite master batch;
Embodiment 2
[0042] This example provides a preparation method of a new type of PBAT composite material: (1) mix choline chloride and thiourea at a ratio of 2:1 at 80°C, heat at a constant temperature for 2 hours and filter to obtain a transparent liquid that is It is a new type of plasticizer; (2) mix benzalkonium chloride with the new type of plasticizer according to (1) according to the ratio, and then heat it at a constant temperature of 80°C for 30 minutes to obtain a mixed solvent; (3) mix the starch at 80°C After drying for 10 hours and removing the water, mix the mixed solvent with (2) uniformly and heat at 80°C for 6 hours before use; (4) bake PBAT at 80°C for 10 hours, mix 100 parts of PBAT, part, 12 parts of new plasticizer, 0.1 part of antibacterial agent, add in equipment and mix 30min, by single-screw granulation, make composite material master batch; (5) described master batch is made novel PBAT composite material by tabletting machine .
PUM
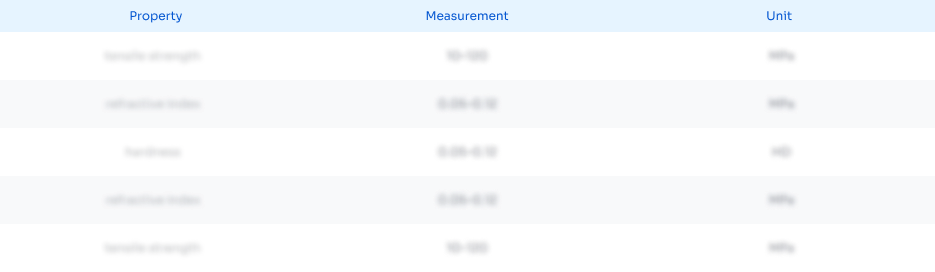
Abstract
Description
Claims
Application Information

- R&D Engineer
- R&D Manager
- IP Professional
- Industry Leading Data Capabilities
- Powerful AI technology
- Patent DNA Extraction
Browse by: Latest US Patents, China's latest patents, Technical Efficacy Thesaurus, Application Domain, Technology Topic, Popular Technical Reports.
© 2024 PatSnap. All rights reserved.Legal|Privacy policy|Modern Slavery Act Transparency Statement|Sitemap|About US| Contact US: help@patsnap.com