Method for preparing roadbed material by curing hard rock shield muck
A road base and shield technology, which is applied to roads, roads, buildings, etc., can solve the problems of low strength of road base materials, large use of organic curing agents, and high content of residual foaming agents.
- Summary
- Abstract
- Description
- Claims
- Application Information
AI Technical Summary
Problems solved by technology
Method used
Image
Examples
Embodiment 1
[0025] The method for preparing road base material by solidifying hard rock shield dregs of the present invention comprises the following steps:
[0026] During shield construction, add high-efficiency defoamer solution to the shield dregs at the front end of the screw conveyor of the shield machine at a volume ratio of 0.2%, and use the high-efficiency defoamer to The solution and the shield dregs are evenly mixed, and then spray the antifoam solution and the viscosifier solution to the shield dregs at the mud outlet of the screw conveyor of the shield machine according to the volume ratio of 0.2% and 0.3%, respectively. During the belt conveying process of the belt conveyor of the shield machine, the shield muck, the antifoaming agent solution and the tackifier solution are mixed, and then the composite curing agent is added to the shield muck at the end of the belt conveyor of the shield machine, The dosage of composite curing agent is 20kg / m 3 , and finally send it into t...
Embodiment 2
[0039] The method for preparing road base material by solidifying hard rock shield dregs of the present invention comprises the following steps:
[0040] During shield construction, add a high-efficiency defoamer solution to the shield dregs at the front end of the screw conveyor of the shield machine at a volume ratio of 0.6%, and use the screw conveying process of the screw conveyor of the shield machine to transfer the high-efficiency defoamer The solution and the shield dregs are evenly mixed, and then spray the antifoam solution and the viscosifier solution to the shield dregs at the mud outlet of the screw conveyor of the shield machine according to the volume ratio of 0.35% and 0.55%, respectively. During the belt conveying process of the belt conveyor of the shield machine, the shield muck, the antifoaming agent solution and the tackifier solution are mixed, and then the composite curing agent is added to the shield muck at the end of the belt conveyor of the shield mac...
Embodiment 3
[0055] The method for preparing road base material by solidifying hard rock shield dregs of the present invention comprises the following steps:
[0056] During shield construction, add high-efficiency defoamer solution to the shield dregs at a volume ratio of 1% at the front end of the screw conveyor of the shield machine, and use the high-efficiency defoamer to The solution and the shield dregs are evenly mixed, and then spray the antifoam solution and the viscosifier solution into the shield dregs at the mud outlet of the screw conveyor of the shield machine according to the volume ratio of 0.5% and 0.8%, respectively. During the belt conveying process of the belt conveyor of the shield machine, the shield muck, the antifoaming agent solution and the tackifier solution are mixed, and then the composite curing agent is added to the shield muck at the end of the belt conveyor of the shield machine, The dosage of composite curing agent is 50kg / m 3 , and finally send it into t...
PUM
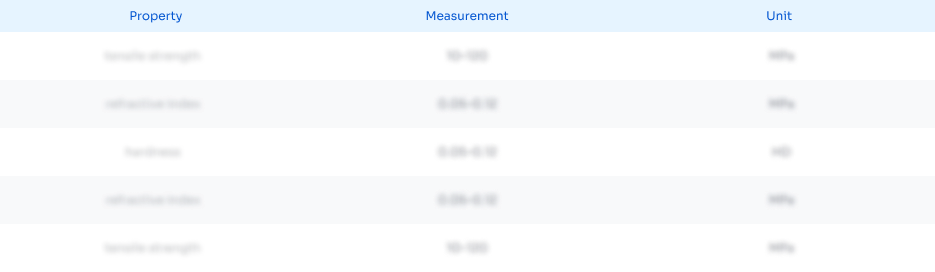
Abstract
Description
Claims
Application Information

- R&D
- Intellectual Property
- Life Sciences
- Materials
- Tech Scout
- Unparalleled Data Quality
- Higher Quality Content
- 60% Fewer Hallucinations
Browse by: Latest US Patents, China's latest patents, Technical Efficacy Thesaurus, Application Domain, Technology Topic, Popular Technical Reports.
© 2025 PatSnap. All rights reserved.Legal|Privacy policy|Modern Slavery Act Transparency Statement|Sitemap|About US| Contact US: help@patsnap.com