Precision casting silica sol shell preparation process
A manufacturing process and technology of silica sol, applied in the directions of casting molds, casting mold components, manufacturing tools, etc., can solve the problems of high cost and long shell making cycle, achieve low cost, reduce the number of coating layers, and do not affect the air permeability. Effect
- Summary
- Abstract
- Description
- Claims
- Application Information
AI Technical Summary
Problems solved by technology
Method used
Examples
Embodiment 1
[0025] The present embodiment provides a process for manufacturing a precision casting silica sol mold shell, comprising the following steps:
[0026] S1. Surface layer shell making: Dip the cleaned wax mold into the prepared surface layer slurry to coat evenly, take it out and blow it evenly with an air gun, then put it into 80-120 mesh mullite and turn it over evenly, at a temperature of 22 ℃-24℃, humidity 50%-60% and dry for 14 hours; the surface layer slurry is made of 830 mesh silica sol, 320 mesh zircon powder, wetting agent, fatty acid glyceride defoamer, and the stirring time is 26 hour, the mass ratio of silica sol to zircon powder is 1: 2.8, every kilogram of silica sol is equipped with 5ml wetting agent and 3ml defoamer, and wetting agent is composed of heptadecyl imidazoline, polyoxyethylene fatty alcohol ether and propylene glycol The mass ratio is 10:6:4, and the viscosity of the surface layer slurry is 40 seconds.
[0027] S2. Transition layer shell making: Put...
Embodiment 2
[0032] The present embodiment provides a process for manufacturing a precision casting silica sol mold shell, comprising the following steps:
[0033] S1. Surface layer shell making: Dip the cleaned wax mold into the prepared surface layer slurry to coat evenly, take it out and blow it evenly with an air gun, then put it into 80-120 mesh mullite and turn it over evenly, at a temperature of 22 ℃-24℃, drying under the condition of humidity 60%-70% for 14 hours; the surface layer slurry is made of 800 mesh silica sol, 320 mesh zircon powder, wetting agent, polydimethylsiloxane defoamer, The stirring time is 26 hours, the mass ratio of silica sol to zircon powder is 1:3.0, 6ml of wetting agent and 5ml of defoamer are prepared per kilogram of silica sol, and the wetting agent is composed of heptadecyl imidazoline, polyoxyethylene fatty alcohol Ether and propylene glycol are compounded at a mass ratio of 10:7:3, and the viscosity of the surface layer slurry is 45 seconds.
[0034] ...
Embodiment 3
[0039] The present embodiment provides a process for manufacturing a precision casting silica sol mold shell, comprising the following steps:
[0040] S1. Surface layer shell making: Dip the cleaned wax mold into the prepared surface layer slurry to coat evenly, take it out and blow it evenly with an air gun, then put it into 80-120 mesh mullite and turn it over evenly, at a temperature of 22 ℃-24℃, humidity 55%-65% and dry for 14 hours; the surface layer slurry is made of 850 mesh silica sol, 280 mesh zircon powder, wetting agent, fatty acid glyceride defoamer, and the stirring time is 26 hours, the mass ratio of silica sol to zircon powder is 1:2.8, and 8ml of wetting agent and 4ml of defoaming agent are mixed with each kilogram of silica sol, and the wetting agent is composed of polyoxyethylene fatty alcohol ether and propylene glycol in a mass ratio of 8:2. It is formulated, and the viscosity of the surface layer slurry is 35 seconds.
[0041] S2. Transition layer shell m...
PUM
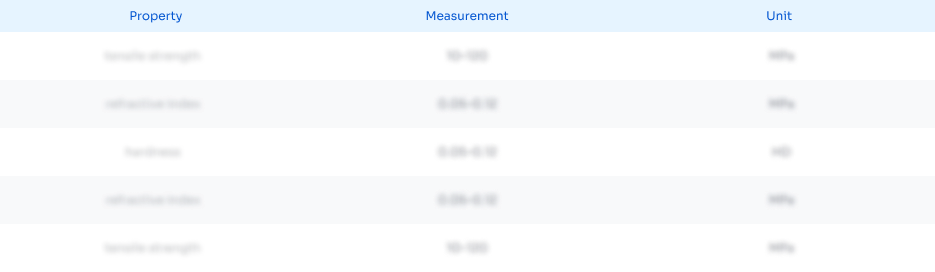
Abstract
Description
Claims
Application Information

- R&D
- Intellectual Property
- Life Sciences
- Materials
- Tech Scout
- Unparalleled Data Quality
- Higher Quality Content
- 60% Fewer Hallucinations
Browse by: Latest US Patents, China's latest patents, Technical Efficacy Thesaurus, Application Domain, Technology Topic, Popular Technical Reports.
© 2025 PatSnap. All rights reserved.Legal|Privacy policy|Modern Slavery Act Transparency Statement|Sitemap|About US| Contact US: help@patsnap.com