Preparation method of high-performance ceramic reinforced iron-based composite material
An iron-based composite material and composite material technology are applied in the field of high-performance ceramic reinforced iron-based composite materials and their preparation, and achieve the effects of good stress and load, good fluidity, and excellent shock resistance
- Summary
- Abstract
- Description
- Claims
- Application Information
AI Technical Summary
Problems solved by technology
Method used
Image
Examples
Embodiment 1
[0072] (1) The 5-micron alumina powder produced by Aladdin and the 500-nanometer zirconia powder produced by West Asia Pharmaceutical were uniformly ball-milled and mixed at a mass ratio of 1:1.5 to obtain the first mixture. Combine the mixture obtained in the first step with water reducer HPEG2400 and stabilizer Y 2 o 3 , thickener CMC, and deionized water were uniformly mixed according to the mass ratio: 120:1:8:3:100, and ball milled again for 3 hours to obtain a ceramic slurry with good fluidity.
[0073] Take 15ppi polyurethane foam and cut it into 50×50×20mm blocks, evenly coat the ceramic slurry on the 15ppi polyurethane foam template to obtain the first preform, and vacuumize for 10 minutes until there are no closed-cell bubbles on the surface of the polyurethane foam. Put the first preform into an oven, keep it warm at 40°C and 80°C for 24 hours, and fully dry it.
[0074] The three-dimensional network preform was heated to 1450° C. for 2 hours at a heating rate of ...
Embodiment 2
[0079] (1) The 3-micron alumina powder produced by Aladdin and the 1000-nanometer zirconia powder produced by West Asia Pharmaceutical were uniformly ball milled and mixed at a mass ratio of 1:1 to obtain the first mixture. Combine the mixture obtained in the first step with water reducer HPEG2400 and stabilizer Y 2 o 3 , thickener CMC, and deionized water were uniformly mixed according to the mass ratio: 120:0.5:6:3:100, and ball milled again for 4 hours to obtain a ceramic slurry with good fluidity.
[0080] Take 35ppi polyurethane foam and cut it into 60×60×15mm blocks, evenly coat the ceramic slurry on the 35ppi polyurethane foam template to obtain the first preform, and vacuumize for 20 minutes until there are no closed-cell bubbles on the surface of the polyurethane foam. Put the first preform into an oven, keep it warm at 40°C and 80°C for 48 hours, and fully dry it.
[0081] The three-dimensional network preform was heated to 1550° C. for 3 hours at a heating rate of...
Embodiment 3
[0086] (1) The 4-micron alumina powder produced by Aladdin and the 800-nanometer zirconia powder produced by West Asia Pharmaceutical were uniformly ball milled and mixed at a mass ratio of 1:2 to obtain the first mixture. Combine the mixture obtained in the first step with water reducer HPEG2400 and stabilizer Y 2 o 3 , thickener CMC, and deionized water were uniformly mixed according to the mass ratio: 120:0.8:7:3:100, and ball milled again for 3.5 hours to obtain a ceramic slurry with good fluidity.
[0087] Take 25ppi polyurethane foam and cut it into 50×50×15mm blocks, evenly coat the ceramic slurry on the 25ppi polyurethane foam template to obtain the first prefabricated body, and vacuumize for 15 minutes until there are no closed-cell bubbles on the surface of the polyurethane foam. Put the first preform into an oven, keep it warm at 40°C and 80°C for 36 hours, and fully dry it.
[0088] The three-dimensional network prefabricated body was heated to 1500 °C for 2.5 ho...
PUM
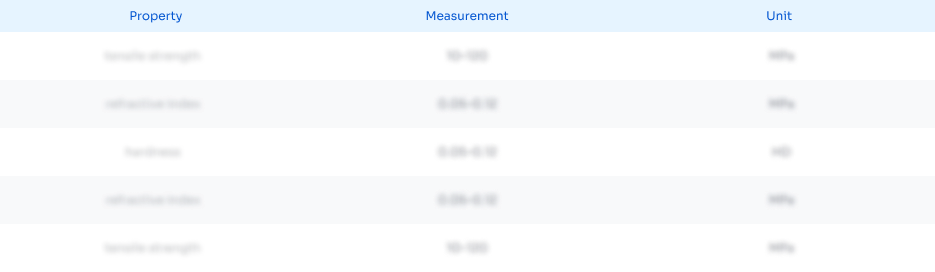
Abstract
Description
Claims
Application Information

- R&D
- Intellectual Property
- Life Sciences
- Materials
- Tech Scout
- Unparalleled Data Quality
- Higher Quality Content
- 60% Fewer Hallucinations
Browse by: Latest US Patents, China's latest patents, Technical Efficacy Thesaurus, Application Domain, Technology Topic, Popular Technical Reports.
© 2025 PatSnap. All rights reserved.Legal|Privacy policy|Modern Slavery Act Transparency Statement|Sitemap|About US| Contact US: help@patsnap.com